What Is Gravity Casting
Gravity casting is a process of manufacturing castings from metal materials and pouring molten metal into a mold under gravity to obtain castings. Because a pair of metal molds can be poured hundreds to tens of thousands of times, metal mold casting is also called permanent mold casting. Metal mold casting is not only suitable for mass production of non-ferrous alloy castings such as aluminum alloys and magnesium alloys with complex shapes, but also for the production of iron and steel metal castings and ingots.Gravity casting can be divided into sand casting and metal casting according to the material of the mold. The precision casting factory is handy with both casting processes, and designs and manufactures these two types of casting molds by themselves.
Casting can also be divided into gravity casting and pressure casting according to the casting process of molten metal. Gravity casting refers to a process in which molten metal is injected into a mold under the action of the earth’s gravity, also known as casting. Gravity casting in a broad sense includes sand casting, metal casting, investment casting, lost foam casting, mud casting, etc.; gravity casting in a narrow sense refers to metal casting. Die casting refers to a process in which molten metal is injected into a mold under the action of other external forces (excluding gravity). Die casting in a broad sense includes pressure casting and vacuum casting of die casting machines, low pressure casting, centrifugal casting, etc.; pressure casting in a narrow sense refers to metal die casting of die casting machines, referred to as die casting.BE-CU Precision foundry has long been engaged in gravity casting of sand and metal molds. These casting processes are the most commonly used in non-ferrous metal casting and have the lowest relative prices.
Gravity Casting Manufacturer – Gravity Die Casting Suppliers
A wide variety of Metal Gravity Castings are provided, the built-in chromium oxide layer of the casting parts provides excellent corrosion resistance, which makes metal castings ideal for mechanical, industrial, military, and more industries and fields. Custom manufacturer of pressure die and investment castings made from zinc, copper, aluminum, magnesium, lead, pewter, brass and steel. Capable of making complex, medium and large parts and precision parts by CNC machines for post-processing. Surface finishing such as sandblasting, powder coating, polishing, plating and painting offered. Other services include CNC machining, injection molding, extrusion, sheet metal prototyping, vacuum casting, rapid tooling and surface finishing. For OEM Aluminum Gravity Castings, we’ll work closely with our customers to reduce unnecessary costs and minimize the lead time, also ensure the consistency in quality of casting parts. Metal castings are distinguished from other casts by the enhanced corrosion and oxidation resistance, they can also work at elevated temperatures. BE-CU Precision foundry is able to offer a high level of accuracy and repeatability for precision casting parts, the lost wax casting and sand casting process makes near-net-shape metal parts and requires little secondary processing.
Reasons For The Deformation Of Gravity Casting Machine Castings
When using a gravity casting machine to produce a schedule, sometimes unexpected things happen, and the produced castings are deformed is one of them. Although some deformed castings can be corrected, they still need to be avoided to avoid increasing production costs. If you want to avoid it, you must first know the cause. Let BE-CU Precision foundry tell you the reason for the deformation of the casting.
In fact, the deformation of the casting is the result of gravity casting stress. If the casting stress generated during the cooling process of the casting exceeds the yield strength of the alloy at this temperature, residual deformation will occur;
if it exceeds the tensile strength, cracks will form; It is manifested as residual stress, which may change the design strength, and even cause the casting to deform or crack during storage or use.
To put it simply, the gravity casting machine gave the casting a force it could not bear during production, so that the casting could not bear and was deformed.
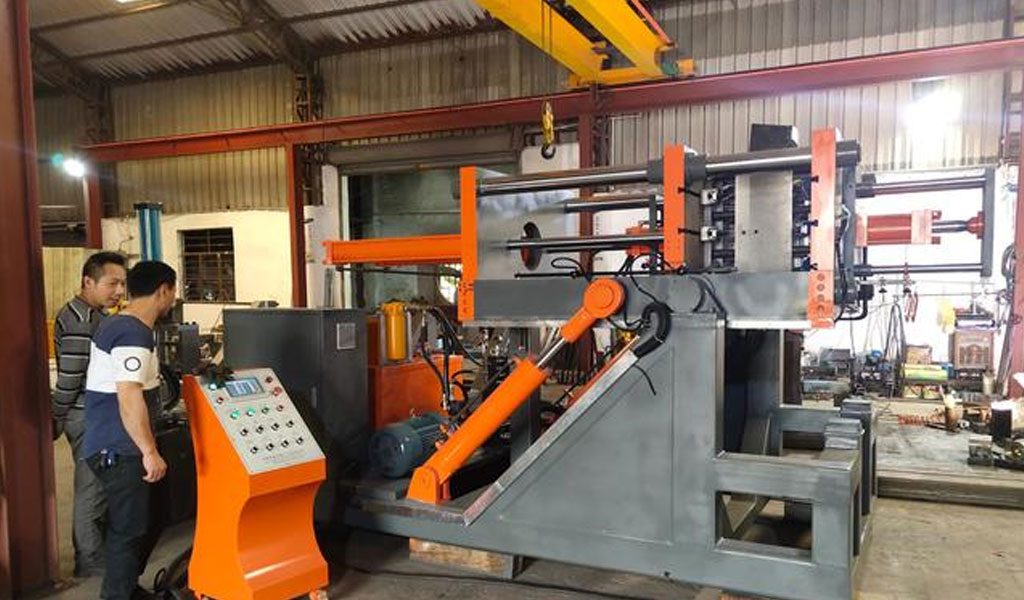
However, the deformation of castings such as steel, non-ferrous metals and ductile iron, and even some iron, can be corrected by mechanical methods, in the process of heating or heat treatment. In production, it is necessary to make the structure of the casting as reasonable as possible, and the use of reverse deformation in the production of gravity casting molds can properly control the generation of casting stress, so that the deformation of the casting can be avoided as much as possible.
The Difference Between Die Casting And Gravity Casting
Aluminum alloy casting processes are roughly divided into two types: gravity casting and pressure casting.Aluminum alloy pressure casting refers to the process in which molten metal is injected into the mold under the action of other external forces (excluding gravity). Die casting is divided into high pressure casting and low pressure casting.
High pressure casting is what we usually call die casting. The aluminum liquid is poured into the pressure chamber, and the mold cavity is filled at high speed through its pressure, and the aluminum liquid is solidified under pressure to form an aluminum casting.The characteristics of aluminum alloy die castings are:
- The surface finish of the product is good, generally reaching Ra6.3 or even Ra1.6.
- No heat treatment.
- The product has high air tightness, high casting strength and surface hardness, but low elongation.
- The mold cost is high and the service life is short.
- High production efficiency.
- Thin-walled parts can be produced with small machining allowance.
Aluminum alloy gravity casting refers to the process of injecting molten aluminum into the mold under the action of the earth’s gravity. Gravity casting is divided into: sand casting, metal mold (steel mold) casting, lost foam casting, etc.The most widely used metal mold (steel mold) casting is made of heat-resistant alloy steel. The strength, size and appearance of the cast aluminum casting are higher than those of other casting processes.
The molten aluminum of gravity casting is generally poured into the gate manually. It relies on the self-weight of the molten metal to fill the cavity, exhaust, cool, and open the mold to obtain the sample. The process flow is generally: molten aluminum smelting, casting filling, exhausting , cooling, mold opening, production cleaning, heat treatment, processing.The characteristics of aluminum alloy gravity castings are:
- The surface finish of the product is not high, and pits are easily generated after shot blasting.
- There are few pores in the aluminum casting, and heat treatment can be performed.
- The product has low density and slightly poor strength, but high elongation.
- The mold cost is low and the mold service life is long.
- The production efficiency is low, thereby increasing the production cost.
- The process is relatively simple, and it is not suitable for the production of thin-walled parts.
When choosing which process to produce the product, it is mainly based on the wall thickness of the workpiece. When the wall thickness of the product is greater than 8mm, die casting will cause a lot of pores to be stored in the wall, so the product with thicker wall thickness can choose the gravity casting process