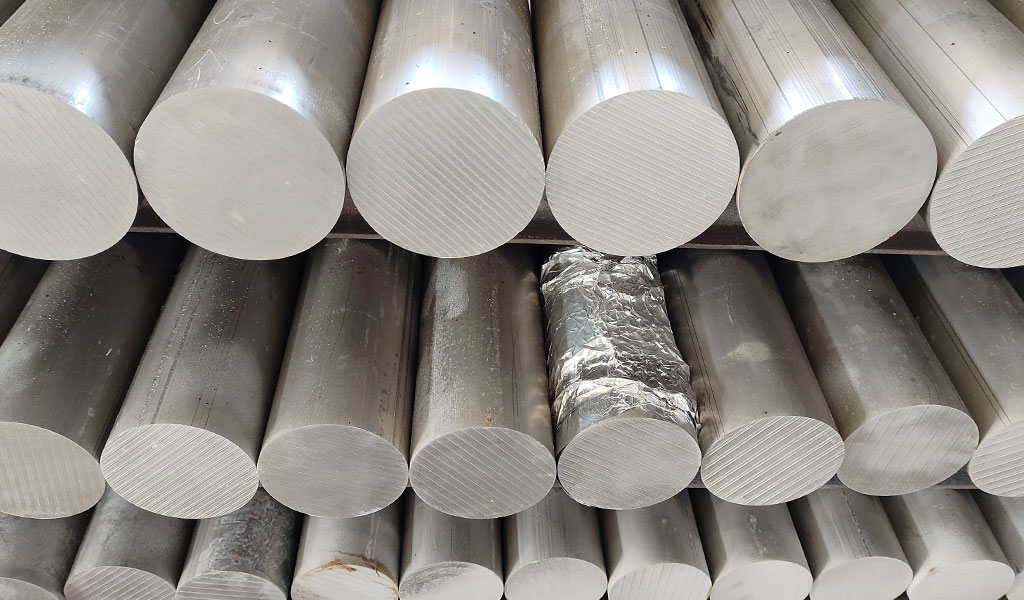
Magnesium alloys are widely recognized for their lightweight properties, which make them ideal for applications in industries such as automotive, aerospace, and electronics. Their high strength-to-weight ratio, coupled with good machinability, has made them increasingly popular in the production of components such as die castings. However, one of the major challenges faced in the CNC machining of magnesium alloy die castings is corrosion. Corrosion is a complex phenomenon that affects the performance, longevity, and reliability of components, and magnesium alloys, due to their electrochemical properties, are particularly susceptible to various types of corrosion. This article explores the corrosion problems encountered during CNC machining of magnesium alloy die castings, investigating the causes, types, prevention methods, and the impact of machining processes on corrosion resistance.
Introduction to Magnesium Alloys
Magnesium alloys are a class of metals in which magnesium is the primary metal, typically alloyed with elements such as aluminum, zinc, manganese, or rare earth metals. These alloys are known for their low density, high specific strength, and good machinability, making them ideal for high-performance applications where weight reduction is crucial. The most commonly used magnesium alloys include AZ91D (composed primarily of magnesium, aluminum, and zinc) and AM60B (composed of magnesium and aluminum). These alloys are frequently used in die casting, a manufacturing process that involves injecting molten metal into a mold under high pressure to create complex shapes with high dimensional accuracy.
Corrosion Mechanism of Magnesium Alloys
Corrosion in magnesium alloys occurs when the material undergoes a chemical reaction with its environment, typically in the presence of moisture or other corrosive agents. This reaction can lead to the degradation of the material’s properties and, in severe cases, the failure of the component. Magnesium, as a highly electropositive metal, is prone to corrosion when exposed to environmental conditions such as moisture, salts, or atmospheric gases. The primary forms of corrosion in magnesium alloys include galvanic corrosion, pitting corrosion, stress corrosion cracking, and uniform corrosion.
- Galvanic Corrosion: Galvanic corrosion occurs when two different metals are in electrical contact with each other and are exposed to an electrolyte, such as water or salt. In the case of magnesium alloys, if they are in contact with more noble metals like aluminum, copper, or steel, magnesium will act as the anode and corrode preferentially. This type of corrosion is often observed in applications where magnesium components are assembled with other metals, leading to accelerated degradation of the magnesium.
- Pitting Corrosion: Pitting corrosion is a localized form of corrosion that occurs when small areas of the metal surface are attacked, resulting in the formation of pits or cavities. In magnesium alloys, pitting corrosion is often exacerbated by the presence of chloride ions, such as those found in seawater or de-icing salts. These ions penetrate the protective oxide layer on the surface of the magnesium, leading to localized breakdown and further corrosion.
- Stress Corrosion Cracking (SCC): Stress corrosion cracking is a form of corrosion that occurs under the combined influence of tensile stress and a corrosive environment. Magnesium alloys, particularly those that have been machined or subjected to residual stresses, are susceptible to SCC. This type of corrosion can cause brittle fracture and failure of components, even when the material is subjected to relatively low levels of stress.
- Uniform Corrosion: Uniform corrosion is characterized by the even loss of material from the surface of the magnesium alloy, typically due to exposure to acidic or basic environments. This form of corrosion can lead to a gradual thinning of the material, weakening its structural integrity over time.
Corrosion Issues in CNC Machining of Magnesium Alloy Die Castings
CNC machining of magnesium alloy die castings introduces additional challenges that can exacerbate the corrosion susceptibility of the material. These challenges stem from both the inherent properties of magnesium alloys and the machining processes themselves.
1. Heat Generation During Machining
One of the primary factors influencing corrosion in CNC machining of magnesium alloys is the heat generated during the machining process. Magnesium alloys have low thermal conductivity, meaning that the heat produced during cutting or grinding remains concentrated at the tool-workpiece interface. This heat can lead to the formation of an oxide layer on the surface of the material, which, while protective in some cases, can also act as a site for localized corrosion if it is not uniform or adequately managed.
The thermal stress generated during machining can also induce microstructural changes in the magnesium alloy, leading to areas of weakness or high reactivity. These areas are more prone to corrosion, particularly when exposed to humid or saline environments.
2. Tooling and Surface Finish
The surface finish of machined magnesium die castings plays a significant role in the material’s corrosion resistance. During CNC machining, tools can introduce surface defects such as microcracks, scratches, or burrs, which create sites for localized corrosion. The finer the surface finish, the less likely these sites are to form, and the more uniform the oxide layer will be. Conversely, a rougher surface finish can promote the formation of pits or cracks, leading to increased susceptibility to corrosion.
Additionally, the type of cutting tool used in CNC machining can influence corrosion. Tools with high reactivity, such as certain types of carbide or high-speed steel, may leave behind residues or particles that can interact with the magnesium alloy, accelerating corrosion. The presence of these tool residues is particularly problematic when machining components for applications exposed to corrosive environments.
3. Lubricants and Coolants
CNC machining typically involves the use of lubricants and coolants to reduce friction, dissipate heat, and prolong tool life. However, many standard machining fluids can be detrimental to the corrosion resistance of magnesium alloys. Water-based coolants, in particular, can introduce moisture into the machining process, leading to the formation of corrosive environments on the surface of the alloy. Furthermore, some lubricants may contain chlorine or other halogens that can exacerbate pitting corrosion when they come into contact with the magnesium surface.
To mitigate these effects, it is important to use lubricants and coolants that are specifically formulated for use with magnesium alloys. These fluids should be free of chlorides and should provide a protective barrier to moisture, helping to prevent the onset of corrosion.
4. Post-Machining Treatments
After CNC machining, magnesium alloy die castings may require additional surface treatments to enhance their corrosion resistance. These treatments can include anodizing, passivation, or applying protective coatings. Anodizing, in particular, is a common technique used to form a protective oxide layer on the surface of the magnesium alloy, increasing its resistance to corrosion. However, the effectiveness of anodizing is heavily dependent on the quality of the surface finish and the presence of machining-induced defects.
Passivation treatments can also be used to enhance the corrosion resistance of magnesium alloys. These treatments involve the formation of a thin, protective oxide layer on the surface, which helps to prevent further corrosion. However, it is essential to note that passivation is not a cure-all solution; it must be combined with proper machining practices to be effective.
In some cases, coatings such as electroless nickel plating, chromate conversion coatings, or organic coatings may be applied to magnesium die castings to improve their resistance to corrosion. These coatings form a barrier between the alloy and the environment, preventing the ingress of moisture or corrosive agents.
5. Residual Stresses and Microstructural Effects
The CNC machining process can introduce residual stresses into magnesium alloy die castings, particularly in areas that experience plastic deformation during cutting. These residual stresses can create conditions that promote stress corrosion cracking (SCC), as they provide localized regions of tensile stress that exacerbate the effects of corrosive environments. Furthermore, the machining process may alter the microstructure of the magnesium alloy, particularly in the heat-affected zone, leading to areas of increased susceptibility to corrosion.
To mitigate the risk of SCC and other corrosion-related issues, it is essential to employ techniques such as stress-relief annealing or vibratory stress relief. These processes can help to reduce residual stresses and restore the material’s integrity, reducing the likelihood of corrosion problems.
Prevention and Mitigation Strategies
Several strategies can be employed to reduce the corrosion susceptibility of CNC machined magnesium alloy die castings. These strategies include material selection, process optimization, and post-machining treatments.
- Material Selection: Choosing the appropriate magnesium alloy for the application is critical in minimizing corrosion problems. Alloys with higher levels of aluminum or rare earth metals tend to exhibit better corrosion resistance. Additionally, selecting alloys with refined microstructures and uniform compositions can reduce the likelihood of localized corrosion.
- Optimizing Machining Parameters: CNC machining parameters, such as cutting speed, feed rate, and depth of cut, should be optimized to minimize heat generation and reduce the risk of surface defects. Using cutting tools with low reactivity and ensuring proper tool maintenance can also help to prevent corrosion.
- Using Corrosion-Resistant Coolants and Lubricants: As mentioned earlier, using non-corrosive coolants and lubricants is essential for reducing the risk of corrosion during machining. Water-based coolants should be avoided in favor of oil-based or dry machining techniques.
- Post-Machining Surface Treatments: Anodizing, passivation, and coating applications are effective methods for improving the corrosion resistance of machined magnesium alloy die castings. These treatments help to create a protective barrier on the surface, preventing corrosion from occurring.
- Stress Relief and Heat Treatment: To minimize the risk of stress corrosion cracking, post-machining stress relief techniques such as annealing or vibratory stress relief should be employed. These processes help to alleviate residual stresses and improve the overall mechanical properties of the magnesium alloy.
Conclusion
Corrosion problems in CNC machining of magnesium alloy die castings are a significant challenge that can impact the performance and longevity of components. Understanding the corrosion mechanisms, including galvanic corrosion, pitting corrosion, stress corrosion cracking, and uniform corrosion, is crucial for mitigating these issues. By optimizing machining parameters, selecting appropriate materials, and applying post-machining treatments, it is possible to reduce the corrosion susceptibility of magnesium alloys and extend the service life of the components. As the demand for lightweight, high-performance materials continues to grow, addressing the corrosion challenges associated with CNC machining of magnesium alloys will remain a key focus for manufacturers seeking to enhance the durability and reliability of their products.