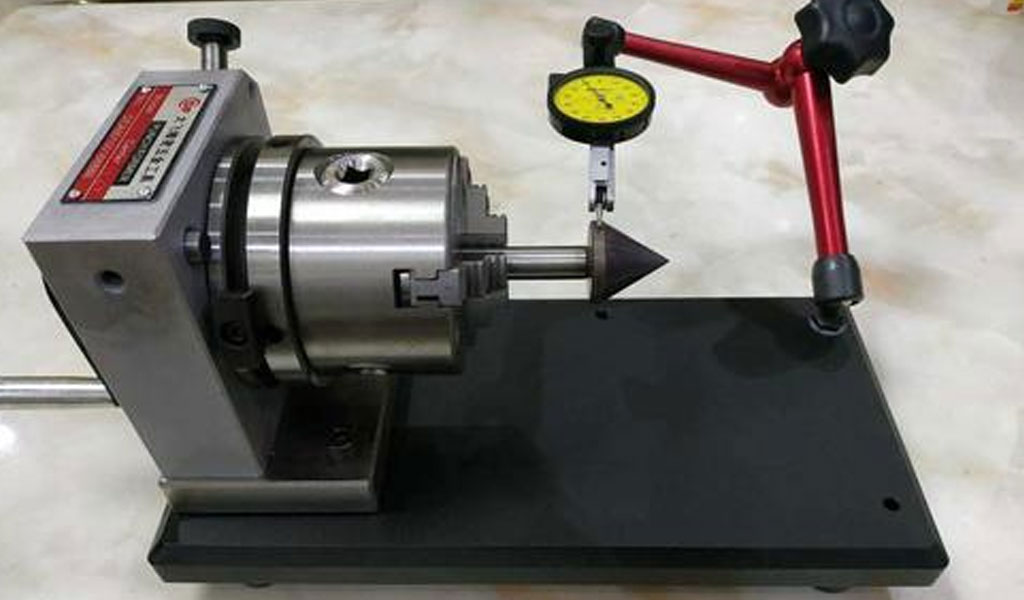
Positioning control is a fundamental aspect of precision manufacturing, ensuring that parts are accurately aligned to meet the required specifications. Among the key concepts within this domain are concentricity and coaxiality—terms that refer to the alignment of different features of a part relative to each other, particularly in terms of their axes. While concentricity and coaxiality are sometimes used interchangeably, they have distinct meanings in the context of engineering and manufacturing, especially in precision machining and metrology. Understanding the difference between these terms and how they are applied is critical for achieving high-precision parts in industries such as aerospace, automotive, medical devices, and others that require tight tolerances.
Concentricity
Concentricity refers to the relationship between the centers of two or more circular features on a part. More specifically, it is a geometric tolerance that controls how closely the center of one circle aligns with the center of another. When two features are concentric, they share a common centerline, meaning their axes lie along the same axis, but they may not necessarily be collinear. The concentricity tolerance ensures that one feature (such as a hole or a shaft) is aligned with another feature in terms of their centerpoints.
For instance, consider a cylindrical part with two holes, one inside the other. To meet concentricity requirements, the center of the smaller hole must be aligned with the center of the larger hole, ensuring that they share the same axis. This alignment is crucial when the part is assembled with other components, particularly when rotating parts are involved, to prevent vibrations, wear, or premature failure.
Concentricity can be difficult to measure accurately in practice due to the complexity of achieving perfect alignment in the manufacturing process. It typically requires the use of precision measurement tools such as CMMs (Coordinate Measuring Machines) or specialized gages. The measurement of concentricity is done by comparing the deviation of the actual center of a feature from its nominal center. Tolerances for concentricity are usually specified in terms of radial deviation, indicating the maximum allowable offset from the ideal center.
The importance of concentricity is particularly evident in applications where rotating parts are used, such as in shafts and bearings. If these parts are not concentric, misalignment can lead to uneven wear, increased friction, and ultimately, mechanical failure. The concept of concentricity is also critical in the design of seals and bearings, where a concentric relationship ensures that the parts move smoothly without excessive clearance or interference.
Coaxiality
Coaxiality is a term that refers to the alignment of two or more cylindrical or rotational features along a common axis. While concentricity deals with the center points of features, coaxiality specifically addresses the alignment of the axes of two or more cylindrical features, such as a shaft and a bearing. The difference between concentricity and coaxiality lies in the fact that coaxiality takes into account the entire axis of the feature, not just the center point.
In practical terms, coaxiality ensures that multiple cylindrical components or features, such as the bore of a shaft or the outer diameter of a housing, are aligned along the same axis. This is essential in preventing eccentricity, which could cause components to wobble or experience uneven wear during operation. Coaxiality is particularly important in high-speed rotating equipment like turbines, electric motors, and gearboxes, where even small misalignments can result in vibration, noise, and premature failure of the components.
In a typical coaxiality application, the tolerance is specified as a maximum allowable deviation between the axes of the features being measured. For example, when designing a shaft and its associated bearing housing, the two features must be coaxial to ensure that the shaft rotates smoothly within the housing without any wobble or binding. If the shaft is misaligned relative to the housing, it can cause uneven load distribution, leading to excessive wear on both the shaft and the bearing.
Measurement of coaxiality is typically done using specialized instruments such as dial indicators, CMMs, or optical systems. The key challenge in coaxiality measurement is to ensure that the axes are aligned over the entire length of the features, which requires precise alignment of the part in the measuring system.
Geometric Dimensioning and Tolerancing (GD&T)
Both concentricity and coaxiality are part of a broader system known as Geometric Dimensioning and Tolerancing (GD&T). GD&T is a standardized method for defining and communicating engineering tolerances in mechanical design. It provides a clear and unambiguous way to specify the allowable variation in the geometry of a part, ensuring that parts fit together as intended during assembly.
In GD&T, concentricity and coaxiality are defined by specific symbols and are subject to precise tolerance requirements. For example, concentricity is typically specified with a feature control frame that includes the concentricity symbol (a circle within a circle), followed by a tolerance value indicating the maximum allowable offset between centers. Coaxiality is also specified with a feature control frame, but it uses a different symbol (two concentric circles) to indicate the requirement for the alignment of axes.
One of the key advantages of using GD&T is that it allows for a more flexible and comprehensive approach to tolerancing. Rather than simply specifying linear dimensions and allowances for features, GD&T incorporates the relationship between different features, such as concentricity and coaxiality, which are essential for ensuring the functional performance of the part in its final assembly.
By defining tolerances for concentricity and coaxiality within the framework of GD&T, engineers can ensure that the part will function as intended, even if there are small variations in the manufacturing process. GD&T provides a clear roadmap for manufacturers, specifying the limits of permissible deviations and ensuring that the part will meet the required specifications.
Applications of Concentricity and Coaxiality
Concentricity and coaxiality are crucial in various industries, particularly in applications that involve rotating or moving parts. In the aerospace industry, for instance, concentricity and coaxiality are critical in the design and manufacturing of engine components, such as turbine blades, shafts, and bearings. Misalignment in these parts can result in catastrophic failures, which is why the tolerances for concentricity and coaxiality are often extremely tight.
In the automotive industry, concentricity and coaxiality play a significant role in the production of engines, transmissions, and suspension systems. Engine components such as crankshafts, camshafts, and pistons must be precisely aligned to ensure smooth operation, reduce vibration, and extend the lifespan of the engine. Similarly, in the production of gearboxes, the gears and shafts must be coaxial to prevent excessive wear and ensure proper meshing of the gears.
The medical device industry also requires strict concentricity and coaxiality tolerances, particularly in the production of implants and surgical tools. For example, orthopedic implants such as hip replacements and knee joints must have features that are precisely concentric to ensure proper fit and function. Any misalignment could result in joint instability or complications during surgery.
In the electronics industry, coaxial cables and connectors are designed to ensure that the central conductor and the outer shield are aligned along the same axis, preventing signal degradation and interference. The performance of high-frequency electronic systems is often dependent on the precise coaxiality of the components used.
Challenges in Achieving Concentricity and Coaxiality
Achieving high levels of concentricity and coaxiality can be challenging, particularly when dealing with complex geometries or high-precision components. The manufacturing process itself can introduce deviations from ideal alignment due to factors such as tooling wear, machine vibration, or thermal expansion. Even slight misalignments can have a significant impact on the performance of the final product, especially in high-precision applications.
One of the most significant challenges is ensuring that the part remains concentric or coaxial throughout the entire manufacturing process. During operations such as turning, milling, or grinding, small deviations in tool position or part setup can lead to misalignment. To counteract these challenges, manufacturers use advanced techniques such as precision fixturing, machine calibration, and real-time monitoring to maintain the required tolerances.
Another challenge is the measurement of concentricity and coaxiality, as both require highly accurate instruments and careful handling to ensure that the measurement is representative of the actual part geometry. In some cases, it may be necessary to measure the part multiple times using different methods to ensure that the measurements are accurate and consistent.
Conclusion
Concentricity and coaxiality are critical concepts in precision manufacturing, particularly in industries that require high levels of accuracy and reliability. While concentricity deals with the alignment of center points, coaxiality focuses on the alignment of axes, both of which are crucial for ensuring the proper function and longevity of rotating or moving components. The ability to control concentricity and coaxiality through geometric dimensioning and tolerancing (GD&T) allows engineers and manufacturers to produce high-quality parts that meet stringent requirements. Despite the challenges in achieving and measuring these tolerances, advancements in manufacturing technology and precision measurement techniques continue to improve the ability to produce parts with minimal deviation from ideal alignment, ensuring that they perform as intended in their final applications.