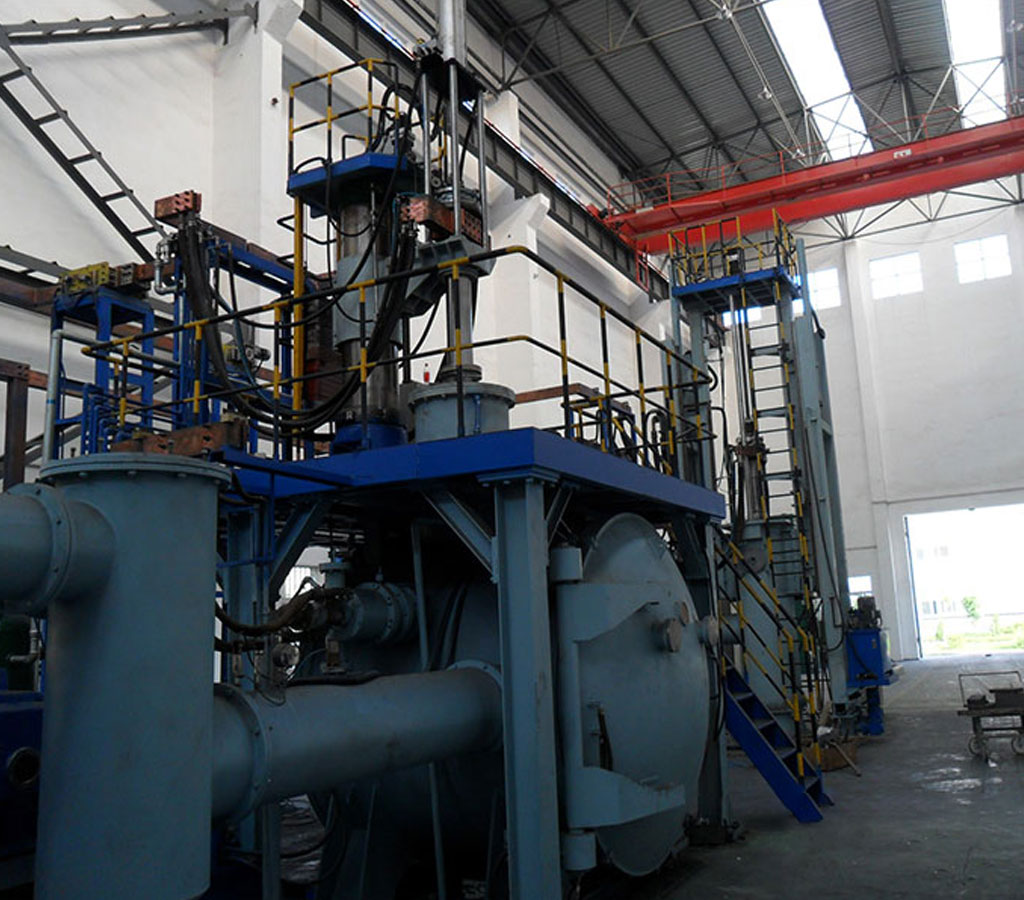
Titanium Casting
Titanium is very active in the molten state. For a long time, it has not been able to find suitable melting and casting methods and molding materials, resulting in cast titanium lagging behind deformed titanium alloys by more than 20 years. From 1956 to 1962, American Bell (Beal) and others developed the vacuum consumable arc condensing shell melting and casting technology, which made titanium castings officially enter into industrial production. In the 1970s, it began to be used in the aerospace field. Since the 1970s, titanium alloy large-scale thin-walled precision casting technology has been developed and applied. Under the premise that its material performance is close to or equal to aviation titanium forgings, the cost is reduced by about 50%, so the titanium casting technology has developed rapidly. It is expected that in the near future, it will achieve the same important position as wrought titanium alloy
If you are willing to work with us or want to know more details, welcome to contact us via email.
Graphite type is the main molding process for the production of civil titanium castings. It is divided into processing graphite type and graphite tamping type. The processed graphite mold is made of high-quality artificial graphite blocks by hand or machine. According to the complexity of the mold, a combination of multiple active blocks can be used. This mold can be used multiple times. Graphite tamping type is made by grinding and mixing artificial graphite sand and carbonaceous organic binder into a mixture, and then molding it by hand or molding machine in a wooden mold or metal mold sand box. The prepared graphite sand mold is baked, dried and solidified at a low temperature, and then roasted at a high temperature under the cover of dry loose graphite powder or under the protection of a non-oxidizing atmosphere. After making the mold combination, it can be installed in the furnace for casting. To produce aviation castings with strict quality requirements, both processed and tamped types need to be vacuum degassed before casting.
Investment casting is the main process for producing titanium alloy castings for aviation with high precision, complex shape, smooth surface and dense interior. The investment casting method of titanium is basically the same as the steel precision casting process, but there are differences in the shell material and some processes.
There are three processes used to produce titanium precision castings today:
- Graphite shell process.
- Metal surface layer ceramic shell process.
- Oxide ceramic shell process.
The first one is cheap and can be used in the production of small and medium castings, and the latter two can be used in the production of large thin-walled precision castings.
Titanium casting is the process of smelting and pouring titanium materials into castings in a vacuum or protective atmosphere. It is one of the preparation processes of titanium materials.Casting titanium alloys and casting quality Most deformed titanium alloys can be used for casting, the most widely used is Ti-6A1-4V alloy. It has good casting performance and stable microstructure. Compared with the deformed alloy of the same composition, the strength of the cast titanium alloy is basically the same, but its plasticity and fatigue properties are about 40% to 50% lower, and the fracture toughness is slightly better.
Titanium material castings are generally treated with stabilization annealing. The solution treatment and hydrogenation treatment in the study can refine the grains, improve the structure, and improve the fatigue properties of the alloy to the level of forgings. Hot isostatic pressing is a common treatment method for high-quality titanium material castings. After high temperature and high pressure treatment, the size of the castings will not change, but the internal structure will become denser, and the stability of mechanical properties will be greatly improved. The quality of castings shall be inspected according to the national standard GB6614, the national military standard GJB2896 or the aviation standard HB5448. The technical characteristics of titanium alloy castings are listed in the table