Investment casting, also known as lost-wax casting, is a precision casting technique used to produce intricate and accurate metal parts. A crucial component of this process is the core, which creates internal cavities and complex geometries within the final cast product. Traditionally, investment casting cores have been made using a variety of materials and methods, including wax, ceramic, and other materials. However, with the advent of 3D printing technology, there have been significant advancements in the design, production, and application of investment casting cores. This article explores the process of building investment casting cores using 3D printing technology, detailing the materials, methods, and benefits associated with this innovative approach.
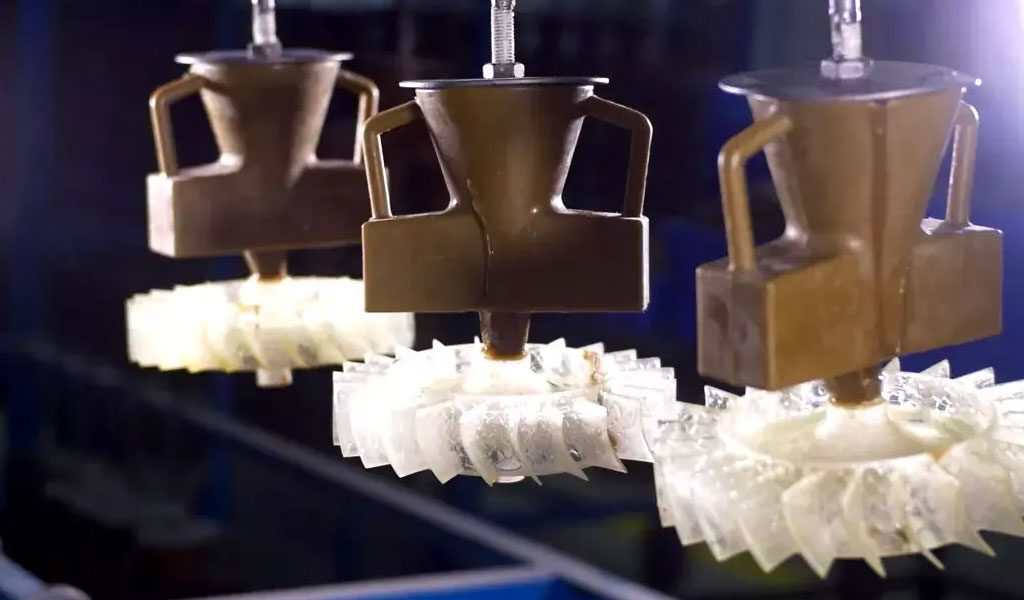
What Is Investment Casting
Investment casting is a manufacturing process that dates back thousands of years, historically used to produce intricate jewelry and metal tools. The modern investment casting process involves creating a wax model, or pattern, of the desired part. This pattern is then coated with a ceramic material to create a mold. Once the ceramic material hardens, the wax is melted and drained away, leaving a hollow mold that can be filled with molten metal. The result is a precise and detailed metal part that replicates the original wax pattern.
In investment casting, cores are used to create internal features or cavities within the cast part that are not possible to achieve with just the outer mold. These cores are typically made from materials that can withstand the high temperatures of molten metal and are easily removable after casting. Traditional core materials include ceramic, sand, and wax. The production of these cores involves various techniques, such as injection molding, hand shaping, and machining.
What Is 3D Printing Technology
3D printing, also known as additive manufacturing, is a process of creating three-dimensional objects by adding material layer by layer based on digital models. This technology has revolutionized various industries, including aerospace, automotive, medical, and manufacturing, due to its ability to produce complex geometries, reduce material waste, and shorten production times. There are several types of 3D printing technologies, including stereolithography (SLA), fused deposition modeling (FDM), selective laser sintering (SLS), and direct metal laser sintering (DMLS).
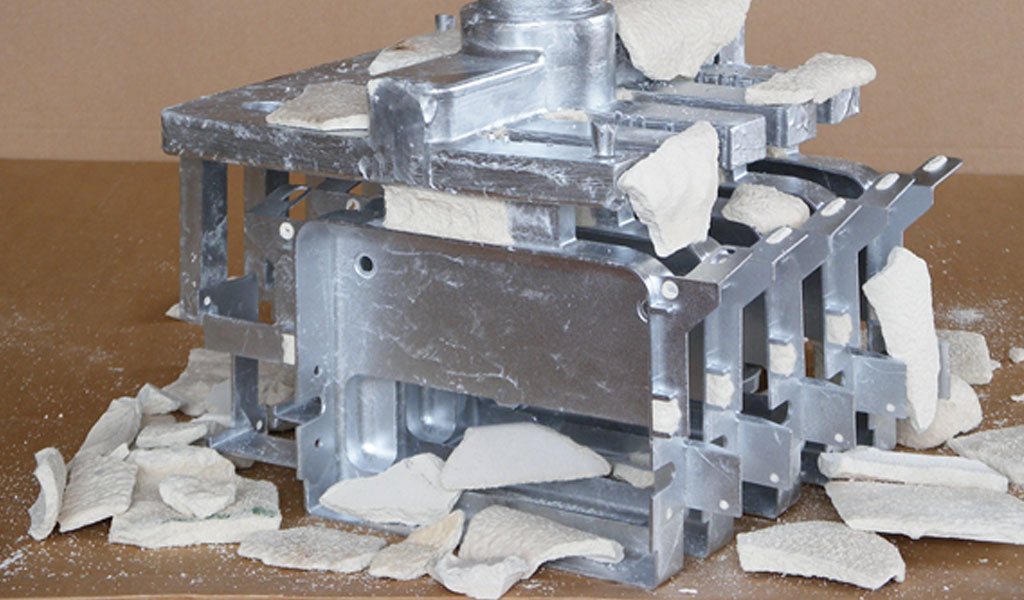
Advantages of 3D Printing in Investment Casting
The integration of 3D printing technology in the production of investment casting cores offers several advantages:
- Design Flexibility: 3D printing allows for the creation of complex geometries that are difficult or impossible to achieve with traditional manufacturing methods.
- Reduced Lead Time: The production of cores using 3D printing can significantly reduce the time required to create molds and patterns, accelerating the overall casting process.
- Cost Efficiency: While the initial investment in 3D printing equipment can be high, the technology can reduce costs in the long run by minimizing material waste and labor costs.
- Customization: 3D printing enables the production of customized cores tailored to specific applications, enhancing the performance and functionality of the final cast parts.
- Quality and Precision: 3D printing offers high precision and repeatability, ensuring the consistency and accuracy of the cores produced.
Materials for 3D Printed Investment Casting Cores
The choice of material for 3D printed cores depends on several factors, including the type of metal being cast, the complexity of the core design, and the desired properties of the final cast part. Common materials used for 3D printed cores include:
- Ceramic Materials: Ceramics are widely used in investment casting due to their high temperature resistance and stability. Ceramic cores can be printed using technologies such as SLA and SLS, which provide high precision and detail.
- Wax: Wax is a traditional material for investment casting patterns and can also be 3D printed using FDM or SLA technologies. Wax cores are typically used for low-temperature metal casting.
- Sand: Sand cores are used for larger castings and can be 3D printed using binder jetting technology. Sand provides good thermal stability and can be easily removed after casting.
- Resins: Various resins, including UV-curable resins, can be used to produce 3D printed cores. These resins offer good detail resolution and can be used for complex geometries.
3D Printing Technologies for Investment Casting Cores
Several 3D printing technologies are suitable for producing investment casting cores, each with its advantages and limitations. The choice of technology depends on the specific requirements of the casting process, including the material, geometry, and size of the core.
Stereolithography (SLA)
SLA is a 3D printing technology that uses a UV laser to cure liquid resin into solid layers. This technology is known for its high precision and ability to produce detailed and smooth surfaces, making it suitable for creating intricate investment casting cores. SLA can be used with various resins, including ceramic-filled resins, to produce cores that can withstand high temperatures.
Fused Deposition Modeling (FDM)
FDM is one of the most widely used 3D printing technologies, where a thermoplastic filament is extruded layer by layer to build an object. While FDM 3d printing is typically used for producing patterns rather than cores, it can be used to create wax cores for low-temperature metal casting. FDM offers cost-effective and accessible solutions for producing investment casting patterns and cores.
Selective Laser Sintering (SLS)
SLS is a 3D printing technology that uses a laser to sinter powdered material, binding it together to create a solid structure. SLS 3d printing is well-suited for producing ceramic and sand cores due to its ability to handle high-temperature materials and create complex geometries. SLS provides good mechanical strength and thermal stability, making it ideal for investment casting applications.
Direct Metal Laser Sintering (DMLS)
DMLS is an advanced 3D printing technology that uses a laser to sinter metal powder, creating fully dense and functional metal parts. While DMLS is not typically used for producing cores, it can be used to create metal patterns and molds for investment casting. DMLS offers high precision and strength, making it suitable for producing intricate and durable components.
Binder Jetting
Binder jetting is a 3D printing technology that involves depositing a liquid binding agent onto a powder bed, layer by layer, to create a solid object. This technology is commonly used for producing sand cores and molds due to its ability to handle large volumes and complex geometries. Binder jetting offers fast production times and good scalability, making it suitable for large-scale investment casting operations.
Design Considerations for 3D Printed Investment Casting Cores
When designing investment casting cores for 3D printing, several factors must be considered to ensure the success of the casting process. These considerations include the geometry of the core, material selection, and the specific requirements of the casting process.
Geometry and Complexity
3D printing allows for the creation of highly complex and intricate geometries that are difficult to achieve with traditional manufacturing methods. When designing cores, it is important to consider the following:
- Thin Walls and Fine Details: 3D printing can produce thin walls and fine details that are essential for creating precise internal features in cast parts. However, the thickness of the walls should be optimized to ensure structural integrity during casting.
- Undercuts and Hollow Sections: 3D printing can easily create undercuts and hollow sections, which are challenging with traditional methods. These features can enhance the performance and functionality of the final cast part.
- Surface Finish: The surface finish of the core can impact the quality of the final cast part. Smooth surfaces can reduce the need for post-processing and improve the overall appearance of the cast part.
Material Selection
The choice of material for 3D printed cores depends on the specific requirements of the casting process, including the type of metal being cast and the desired properties of the final part. Key considerations include:
- Thermal Stability: The core material must be able to withstand the high temperatures of molten metal without degrading or deforming.
- Removability: The core material should be easily removable after casting, either by melting, breaking, or dissolving, without damaging the final cast part.
- Compatibility: The core material must be compatible with the mold material and the metal being cast to prevent reactions or defects.
Process Parameters
The success of 3D printed cores in investment casting also depends on the process parameters used during printing. Key parameters include:
- Layer Thickness: Thinner layers provide higher resolution and better surface finish, but may increase printing time. Optimizing layer thickness is important for balancing quality and efficiency.
- Print Speed: Print speed affects the overall production time and the quality of the printed core. Slower speeds may provide better detail resolution, while faster speeds can improve productivity.
- Support Structures: Support structures are often required to ensure the stability of the core during printing. These supports must be carefully designed to be easily removable without damaging the core.
Post-Processing of 3D Printed Cores
After 3D printing, the cores may require post-processing to ensure they meet the required specifications and are ready for use in investment casting. Common post-processing steps include:
- Cleaning: Removing any residual powder, support structures, or binding agents from the printed core.
- Sintering: For ceramic and sand cores, sintering may be required to enhance mechanical strength and thermal stability.
- Surface Finishing: Smoothing the surface of the core to achieve the desired finish and reduce potential defects in the final cast part.
- Inspection: Verifying the dimensions, geometry, and material properties of the core to ensure it meets the required specifications.
Applications of 3D Printed Investment Casting Cores
The use of 3D printed cores in investment casting has been successfully applied in various industries, including aerospace, automotive, medical, and manufacturing. Some notable applications include:
Aerospace
In the aerospace industry, 3D printed cores are used to produce complex and lightweight components, such as turbine blades, fuel nozzles, and structural parts. The ability to create intricate internal cooling channels and other features enhances the performance and efficiency of aerospace components.
Automotive
The automotive industry benefits from 3D printed cores for producing high-performance engine components, transmission parts, and exhaust systems. The precision and customization offered by 3D printing enable the production of optimized and lightweight parts that improve vehicle performance and fuel efficiency.
Medical
In the medical field, 3D printed cores are used to create customized implants, prosthetics, and surgical instruments. The ability to produce patient-specific geometries ensures a better fit and functionality, enhancing patient outcomes.
Manufacturing
In general manufacturing, 3D printed cores are used for producing intricate and precise components for various applications, including machinery, electronics, and consumer products. The flexibility and efficiency of 3D printing support rapid prototyping and small-batch production.
Future Trends and Developments
The integration of 3D printing technology in investment casting is an evolving field with ongoing research and development. Future trends and developments include:
Advanced Materials
The development of new materials for 3D printing cores, including high-performance ceramics, metal alloys, and composite materials, will expand the range of applications and improve the properties of the final cast parts.
Hybrid Manufacturing
Combining 3D printing with traditional manufacturing methods, such as CNC machining and injection molding, will enhance the capabilities and efficiency of investment casting. Hybrid manufacturing approaches can leverage the strengths of each technology to produce high-quality and cost-effective components.
Automation and Integration
The integration of 3D printing with automated production systems and digital manufacturing platforms will streamline the investment casting process. Automation and digital integration will improve productivity, reduce lead times, and enable real-time monitoring and control of the casting process.
Sustainability
The adoption of sustainable practices in 3D printing and investment casting, including the use of recyclable materials, energy-efficient processes, and waste reduction strategies, will support environmental and economic sustainability in the manufacturing industry.
China Best 3D Printing Investment Casting Provider – BE-CU Casting
The use of 3D printing technology for producing investment casting cores represents a significant advancement in the field of precision casting. The flexibility, precision, and efficiency of 3D printing enable the creation of complex and customized cores that enhance the performance and functionality of the final cast parts.
As technology continues to evolve, the integration of 3D printing in investment casting will drive further innovation and development, supporting a wide range of applications across various industries. The ongoing research and advancements in materials, hybrid manufacturing, automation, and sustainability will shape the future of investment casting and unlock new possibilities for manufacturing complex and high-performance components.
If you are looking for a 3d Print Investment Casting provider in town and want your work to be done by the best, then you must contact BE-CU.COM. They can cater to all your 3d Print Investment Casting needs. Their team of professionals is highly equipped with all the needed knowledge and can help you in this. They have years-long experience in this field and a huge customer base that loves their work. BE-CU can help you in making any design you want, no matter how complex it is. Get in touch with their customer care today.
If you are still confused about what services they offer then here’s the list!
-
304 Stainless Steel Precision Casting Agricultural Machinery Parts
-
304-303 Stainless Steel Lost Wax Casting Bracelet Or Buckle
-
Investment Casting Stainless Steel Oil Press Chamber Rod
-
304 Stainless Steel Sand Casting Components
-
Automotive Shock Absorber Bracket By Casting Iron
-
Custom Brass Fixtures By Sand Casting
-
Gravity Casting A3 Iron Hole Punch Rough
-
Lost Wax Casting Badminton Racket Pulling Machine Accessories
They provide many 3d printing china services and have huge customer bases who love their services. Apart from the consultation, they provide services like:
- On-Demand Manufacturing of Specific Designs
- Appearance Models for Your Products
- Functional Prototyping so that you have a clear Idea
- Low-Volume Production for limited needs
- Rapid Prototyping for faster Production
Their consultation facility can give you a clearer look into all these services, and you can select the one that superlative fits your requirements.