What Is Lost Foam Casting
Lost Foam Casting (LFC; or Expendable Pattern Casting, EPS) is a new technology with nearly no allowance and precise forming. One of the new casting technologies representing the 21st century.
Lost Foam Casting is made of foamed plastic into a solid pattern that is exactly the same as the structure and size of the part, dipped in refractory adhesive coating, dried and then dried with sand, vibrated and compacted, and then poured into molten metal to make the pattern heated. The precision casting method of metal parts with the same shape and shape can be obtained.
Compared with other casting processes, it has the following process features and advantages
- The surface roughness of the casting is low and the dimensional accuracy is high. The dimensional accuracy and surface roughness of castings can reach CTS~CT7 R.=6.3~12.5 µm respectively, which is close to the level of investment casting; the machining allowance is at most 1.5~2mm, which can greatly reduce the cost of machining, which is similar to the traditional sand casting method. ratio, which can reduce the machining time by 40% to 50%; and the casting has no flash burrs, and also reduces the dimensional error caused by the combination of core blocks
- The casting structure design is flexible. The foam plastic is used as the pattern, no need to draw the mold, neither the parting surface nor the core, and the pattern has no mold drafting slope; the components that were originally processed and assembled by multiple parts can be produced by first slicing after the lost foam casting process. The pattern and post-bonding method form an integral foam mold, and the parts are integrally cast 11 11; the core can be omitted, and the hole structure can be directly cast, which greatly saves the time and cost of processing and assembly, and reduces the investment in processing equipment.
- It adopts loose sand for compact modeling, no binder, simplified casting production process and high labor productivity. The lost foam casting process adopts dry sand for compact molding, and the sand does not need binder and moisture, which reduces the adverse effect of sand treatment on the quality of castings, and greatly simplifies the sand treatment process. Almost all the molding sand can be reused, which saves costs; and the traditional whole process of stick sand, compaction, mold taking, box closing and sand treatment is omitted; the pattern can be assembled arbitrarily, and one box can be poured into multiple castings. Therefore, the production efficiency is greatly improved, which is conducive to mass production.
- It is easy to achieve cleaner production. Polystyrene (EPS) is harmless to the environment at low temperature, emits less organic matter during pouring, produces organic emissions in a short time, is concentrated in locations, and is easy to collect. The utilization rate is above 95%. Eliminates noise, co gas and silica dust hazards of lost foam casting processes compared to traditional casting methods Significant reduction, significantly improved environment, easy to achieve mechanization, automation and cleaner production.
Lost Foam Castings & Custom Lost Foam Casting Parts Manufacturer
If you are seeking a supplier of Lost Foam Casting services and custom lost foam casting parts, here is the right place for you. In order to meet the mass production requirements of some customers and reduce costs, we work with our industry-leading in-house factory to assist your project. The extensive and comprehensive network enables us to expand our capabilities and serve more clients across the world, especially those who require quality metal Lost Foam Casting Parts. To lower the price of your lost foam mold manufacturing, our lost foam casting service can offer large prototypes in short time, then we use CNC techniques and machines to modify the appearance and achieve other specifications, which greatly shortens the lead time. However, the precision is only about 0.05mm, and the part complexity should be reviewed before manufacturing to check the feasibility. Other than the casting process, a selection of other services can be applied based on your quote. The stable and long-term relationships between our partners and us allow us to deliver the best quality at the most competitive prices. Before the final order going on its way to customers, multiple quality inspections will be implemented at different production stages of the Lost Foam Casting products. Welcome to send your inquiry or custom designs of Lost Foam Casting parts to be made, we’ll send you a free quote within 24 hours in working days and work out a schedule for recording the progress. Steel and iron Lost Foam Castings are most commonly produced at our factory.
Automatic lost foam production line Lost Foam Debugging Equipment Lost Foam Factory Lost Foam Mould Manufacturing Lost Foam Production Technician Machined Lost Foam
The Advantage Of Lost Foam Casting
The lost foam casting process uses a foamed plastic pattern to form a compact shape.
When pouring, the foamed plastic pattern is heated and vaporized and disappears, cooled and solidified, and finally a casting is obtained. Compared with traditional casting, the castings produced by this process have low surface roughness, high dimensional accuracy, nearly no allowance, accurate forming, flexible casting structure design, no need for moulding, no parting surface and core, and complex castings can be cast as a whole. Lost foam casting has the advantages of high dimensional accuracy of castings, smooth surface and less pollution. With the improvement of lost foam technology and the development of related materials, especially in recent years, with the strengthening of national environmental protection and governance, dry sand molding is adopted. The application range of the lost foam casting process has been continuously expanded and has been developed by leaps and bounds.
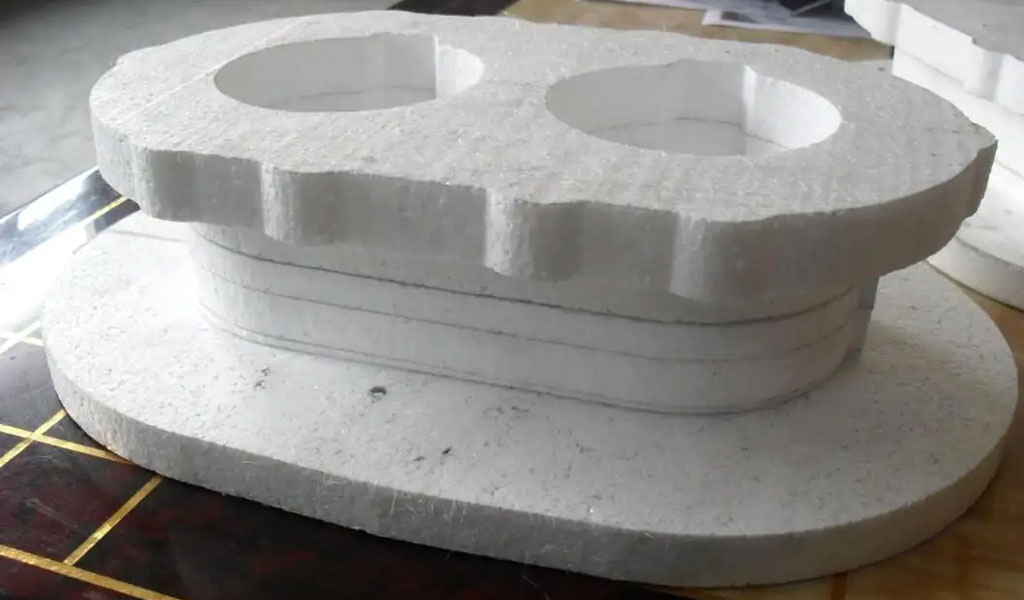
Because the lost foam casting process uses EPS white mold (foam mold), there are pyrolysis products at the front of the molten metal flow, and the reaction with the molten metal affects the filling of the molten metal. higher. In actual production, casting defects such as slag inclusion, pores, sand sticking, and carburization are common in this process. Therefore, when adopting the lost foam casting process, all or part of the EPS white mold should be removed as far as possible before pouring to eliminate the above-mentioned casting process defects. Based on this idea, the use of coatings or shells to isolate sand, moisture and C is beneficial to the casting. In the forming environment, the process test was carried out.
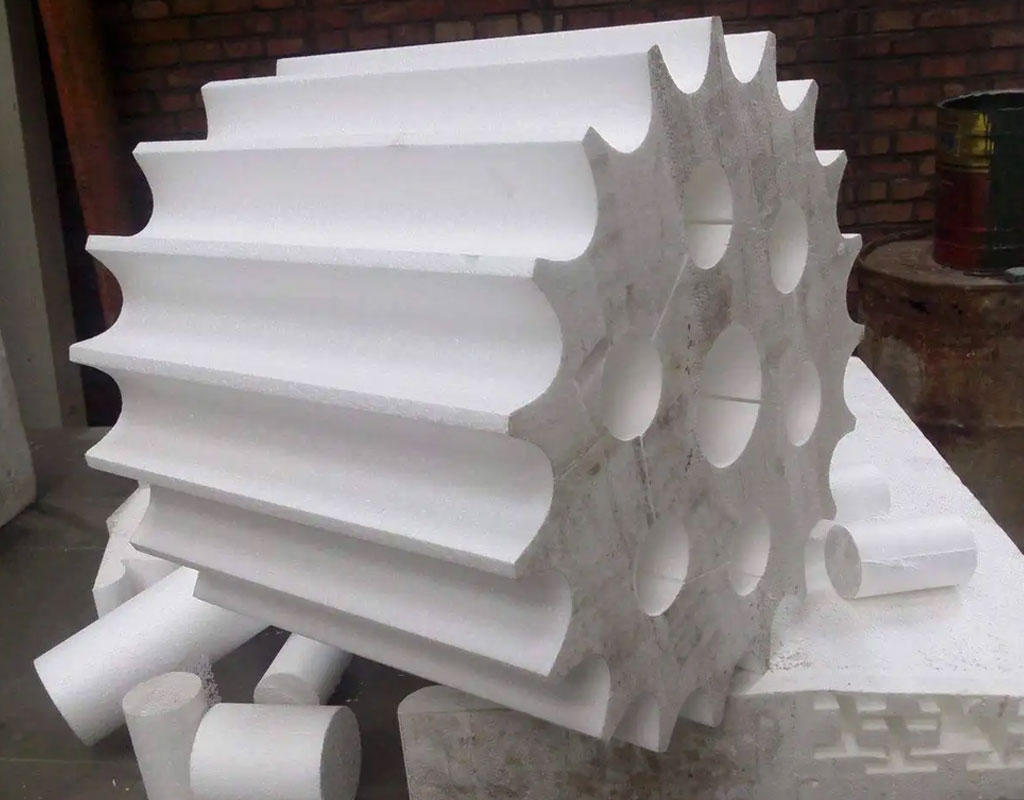
Lost Foam Material For Molds
The process of the lost foam mold is an accurate forming process, which is suitable for various materials such as steel, iron, aluminum, copper, etc., and has a better effect on the lost foam casting with complex structure. In fact, the main raw materials used in lost foam casting are dry sand, casting coatings and model materials. Of course, there are many materials, these are just the most important ones. Dry sand is one of the main raw materials used in lost foam casting. Dry sand should be selected with relatively large particles, refractory and high temperature dry sand. At present, most manufacturers use natural quartz sand to remove moisture and iron slag. And there are certain requirements for the temperature.
Foundry paint is also one of the important raw materials, it has a high refractory composition, and model casting is also a very critical step, requiring fine workmanship and size. Failed. Therefore, the selection of raw materials used in lost foam casting is very high. Only if the requirements are high, the products will be good. The casting principle of the lost foam mold is to use dry sand to replicate the original prototype. The casting requires high dimensional accuracy, no flash, burr, uniformity, and high surface finish. The internal structure of the casting is stable, the process of the lost foam mold makes full use of the concept of environmental protection, the foam-like material is harmless to the environment, and the recycling rate of used sand is over 95%. . The castings cast by the lost foam mold can greatly reduce the labor intensity of workers and reduce the harm to the environment.
The Process Characteristics And Defects Of Lost Foam
When the process technicians consider the casting process, they have a more three-dimensional sense and are more intuitive, which will be more conducive to the optimal design of the casting process plan. At the same time, the casting and feeding system of this process is set up flexibly, and there will be more process trial production schemes, which is conducive to the innovation and improvement of the casting process design level. The EPS white mold provides sufficient free space for the design of the casting structure. For example, for the complex design of the core under the parting of a casting in the conventional casting process, multiple EPS foam plastic modules can be designed to be bonded as a whole white mold; The product structure assembled from parts can also be designed and cast as a whole after bonding multiple EPS foam modules. The disappearing mold has the following characteristics:
Copolymer foam is used as the model material. Because the copolymer is decomposed by zipper, the degree of one-time gasification is high, the proportion of liquid phase is small, and the small molecular gas is easy to overflow from the coating.The casting has high dimensional accuracy and smooth surface. Compared with the traditional molding process, the lost foam casting does not need to open the box to take the mold, does not need to place the sand core, and has no parting surface, so the casting has no flash, burr, and no core combination. Dimensional deviation, the dimensional accuracy of castings can reach CT6~CT9 grades, and the dimensional tolerances of castings are also very small
The lost foam casting process that uses dry sand to fill the molding does not contain chemical binders in the sand, especially in recent years, the use of ceramsite sand (Baozhu sand) is more effective. At low temperature, foam plastic does not cause gas pollution to the environment, and the organic matter emitted during pouring is not only less but also concentrated and discharged in a short time. By adopting the RCO method (adsorption catalytic concentration combustion purification method) centralized treatment, the advantages of cleanliness and environmental protection are obvious, and the equipment measures are also better. Conducive to the improvement of environmental protection.
Lost foam negative pressure casting is more conducive to the filling and feeding of liquid metal, and improves the structure density of the castingThe lost foam casting forming process can improve the casting filling and solidification feeding ability. Under the action of vacuum adsorption and ceramsite sand (baozhu sand) cavity chilling, the internal structure of the casting is dense, which effectively solves the problems of shrinkage and shrinkage. Can improve the mechanical properties of castings (better combined with vibration casting)
The lost foam casting process simplifies the casting process, the equipment is easy to realize mechanization and automation, and the investment is small, which can significantly reduce the number of workers, improve the workshop environment, and reduce investment and production costs; the quality of castings can be improved, the surface is smooth, and the workload after cleaning is greatly reduced. , reduce the dust and noise in the workshop, and have obvious advantages in cleaning and environmental protection.