In the realm of modern manufacturing, the demand for precision, efficiency, and versatility has led to the development and refinement of various techniques. Among these, CNC (Computer Numerical Control) spinning and investment casting stand out as highly effective methods for producing complex metal parts. While each technique has its strengths and limitations, their complementarity offers significant advantages in manufacturing. This article explores the principles, applications, advantages, and limitations of CNC spinning and investment casting, and elucidates how their integration can enhance production processes.
CNC Spinning
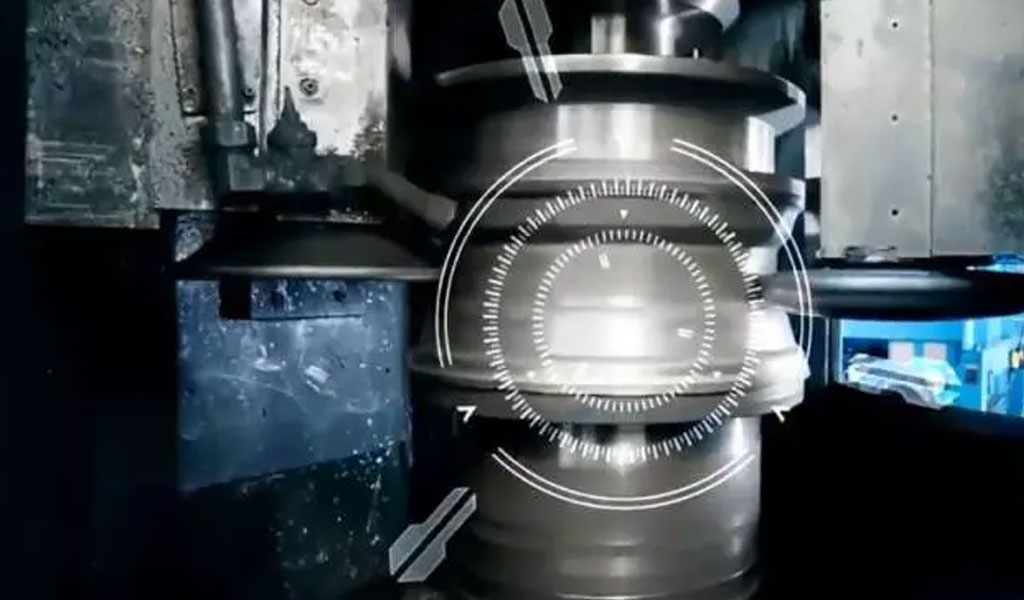
CNC spinning, also known as rotational forming or spin forming, is a metalworking process where a flat metal disc or sheet is deformed into a desired shape by rotating it at high speeds while a tool applies pressure. This technique is predominantly used for producing axisymmetric components, such as cones, cylinders, and hemispheres. The process is characterized by its high precision, ability to work with various metals, and relatively low cost for short to medium production runs.
Process Description
In CNC metal spinning, a metal blank is clamped onto a spinning lathe, which rotates the blank around its central axis. As the blank spins, a forming tool presses against the metal, gradually shaping it into the desired form. CNC technology enables the precise control of both the spinning speed and the forming tool’s movement, which ensures high accuracy and repeatability. The process can be performed either cold or hot, depending on the material and the required properties of the finished product.
Applications
CNC spinning is widely used in the aerospace, automotive, and consumer goods industries. It is particularly suited for producing parts like aerospace engine housings, automotive wheel rims, and decorative metal products. The ability to create complex shapes with minimal tooling makes it an attractive option for prototype development and small to medium production runs.
Advantages
- Precision: CNC spinning allows for high precision in the creation of complex shapes, with minimal variation between parts.
- Material Efficiency: The process generates minimal waste compared to other metalworking techniques, as the majority of the original material is utilized in the final product.
- Versatility: CNC spinning can be applied to a wide range of metals, including aluminum, steel, and titanium, making it suitable for various applications.
Limitations
- Shape Limitations: The process is best suited for axisymmetric shapes and may not be ideal for non-axisymmetric or highly intricate designs.
- Tool Wear: Continuous use of spinning tools can lead to wear and tear, necessitating regular maintenance or replacement.
Investment Casting
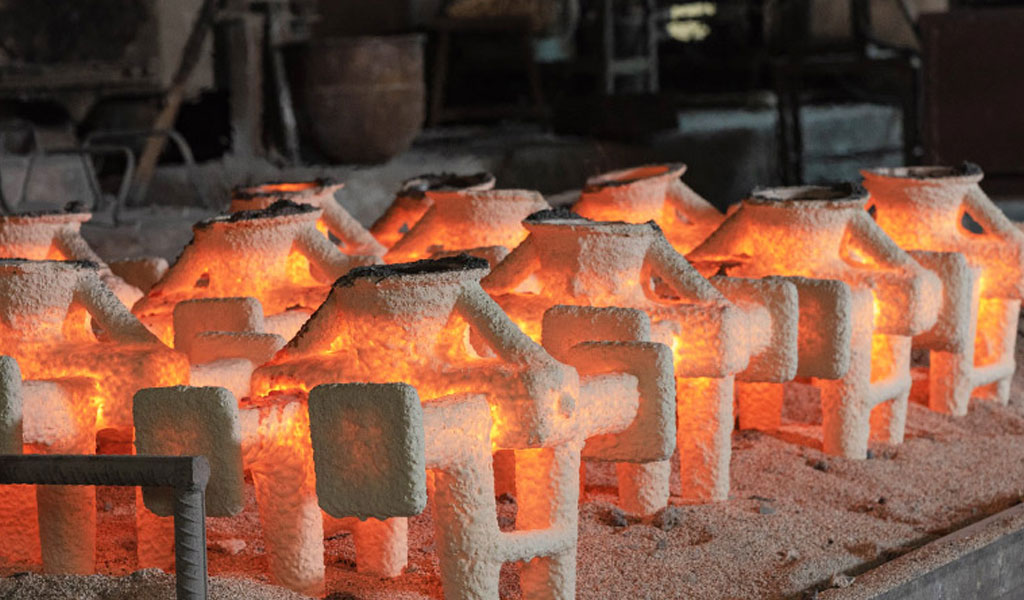
Investment casting, also known as lost-wax casting, is a versatile and precise method of producing complex metal parts. It involves creating a wax model of the desired part, coating it with a ceramic material to form a mold, and then melting out the wax to leave a cavity into which molten metal is poured. This process is valued for its ability to produce parts with intricate details and high dimensional accuracy.
Process Description
The investment casting process begins with the creation of a wax model or pattern of the component. The wax pattern is then repeatedly dipped into a ceramic slurry and allowed to dry, forming a ceramic shell around the wax model. Once the shell is hardened, it is heated to melt and remove the wax, leaving behind a hollow ceramic mold. Molten metal is then poured into the mold, filling the cavity and taking the shape of the original wax pattern. After the metal has solidified, the ceramic shell is broken away to reveal the finished part.
Applications
Investment casting is extensively used in industries requiring high precision and complex geometries, such as aerospace, automotive, and medical device manufacturing. It is particularly useful for producing components like turbine blades, engine parts, and surgical instruments. The process is well-suited for materials such as stainless steel, nickel-based alloys, and aluminum.
Advantages
- Complex Geometries: Investment casting allows for the production of intricate and complex shapes that would be challenging or impossible to achieve with other methods.
- High Precision: The process provides excellent dimensional accuracy and surface finish, reducing the need for post-casting machining.
- Material Versatility: Investment casting can accommodate a wide range of metals and alloys, making it suitable for various applications.
Limitations
- Cost: The initial costs for creating molds and patterns can be high, making investment casting less economical for low-volume production.
- Cycle Time: The process can be time-consuming, particularly when creating complex molds and allowing for the complete removal of wax.
Complementarity of CNC Spinning and Investment Casting
Integration of Techniques
CNC spinning and investment casting, while distinct in their methodologies, can be highly complementary when integrated into a single manufacturing workflow. Each technique addresses different aspects of the production process, and their combined use can leverage the strengths of both.
Scenario of Integration
In certain manufacturing scenarios, CNC spinning can be employed to produce initial prototypes or low-volume parts where rapid iteration and adjustment are crucial. Once a design is finalized, investment casting can be used to produce high-volume parts with intricate details and high precision. This integration allows manufacturers to benefit from the cost-effectiveness and material efficiency of CNC spinning while also taking advantage of the fine details and complex shapes achievable through investment casting.
Advantages of Integration
- Cost Efficiency: Combining CNC spinning for initial runs with investment casting for mass production can optimize production costs, especially when transitioning from prototyping to full-scale manufacturing.
- Design Flexibility: The ability to prototype and test designs using CNC spinning before committing to investment casting ensures that complex geometries and fine details are accurately represented in the final product.
- Enhanced Production Capabilities: The integration of both techniques allows manufacturers to produce a wider range of parts, catering to various industry needs and applications.
Challenges and Considerations
While the integration of CNC spinning and investment casting offers numerous benefits, it also presents certain challenges. Coordinating the transition between the two techniques requires careful planning to ensure that design specifications are maintained and that the quality of the final product meets the required standards. Additionally, the different materials and processes involved may necessitate adjustments in production workflows and quality control measures.
Conclusion
The complementarity of CNC spinning and investment casting underscores the importance of leveraging diverse manufacturing techniques to achieve optimal results. By understanding the strengths and limitations of each method, manufacturers can effectively integrate CNC spinning and investment casting into their production processes, thereby enhancing precision, efficiency, and versatility. This approach not only facilitates the production of high-quality components but also drives innovation and advancement in the manufacturing industry.
The continued evolution of both CNC spinning and investment casting techniques, along with their integration, promises to further expand the possibilities for producing complex and high-precision parts across various industries.