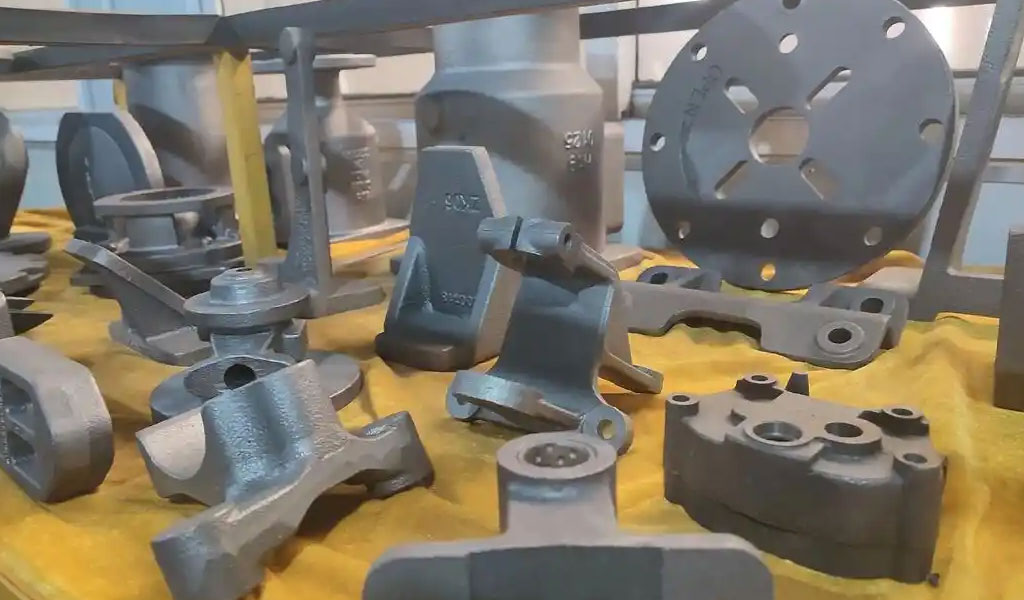
Investment casting, also known as lost-wax casting, is a precise metal-forming process that is commonly used for producing intricate and complex parts. The process involves creating a detailed wax pattern of the desired part, which is then coated with a ceramic shell. After the shell hardens, the wax is melted and drained away, leaving a mold that is ready to be filled with molten metal. The mold undergoes a heating process, and the molten metal is poured into the cavity, where it solidifies into the desired shape.
A crucial aspect of the investment casting process is the shrink factor, which refers to the reduction in volume of a material as it transitions from a liquid to a solid state. This shrinkage must be carefully accounted for during design and mold-making to ensure that the final cast part has the intended dimensions.
In the case of 17-4PH stainless steel, a precipitation-hardening martensitic alloy, it is essential to understand the specific shrinkage characteristics of this material in the investment casting process. Accurate control of the shrink factor ensures that cast parts meet the stringent dimensional tolerances required in industries like aerospace, defense, and medical device manufacturing, where 17-4PH is commonly used due to its excellent mechanical properties and corrosion resistance.
17-4PH Stainless Steel Composition and Properties
17-4PH is a versatile stainless steel alloy containing approximately 17% chromium, 4% nickel, and smaller amounts of copper, niobium, and titanium. This alloy is notable for its high strength, good corrosion resistance, and ease of heat treatment. It is most commonly used in applications where high strength is needed at both room and elevated temperatures.
The alloy undergoes a two-step heat treatment process, involving solution annealing and aging, which gives it its high mechanical strength and hardness. These properties make 17-4PH ideal for demanding applications, including parts used in aerospace, chemical processing, and medical equipment.
The material’s shrinkage behavior in investment casting is influenced by several factors, including the composition of the alloy, the mold material, the casting temperature, and the cooling rate.
Shrinkage in Investment Casting
Shrinkage during solidification occurs because metals contract as they cool from their molten state to room temperature. This shrinkage is a critical factor in casting design and is typically accounted for in the casting process by increasing the size of the pattern relative to the desired final dimensions. For precision and performance, the correct shrink factor must be applied.
The shrinkage factor is typically expressed as a percentage and can vary depending on the alloy used, the casting method, and the final heat treatment of the cast part. For 17-4PH stainless steel, this shrink factor is primarily influenced by the alloy’s solidification characteristics, including its solidus and liquidus temperatures, which determine the temperature ranges at which the metal transitions from a liquid to a solid.
Factors Affecting Shrink Factor for 17-4PH
- Alloy Composition: The presence of elements like chromium, nickel, copper, and titanium in 17-4PH stainless steel influences its shrinkage behavior. These elements can affect the solidification process, altering the rate at which the metal cools and solidifies.
- Casting Temperature: The temperature at which the 17-4PH alloy is poured into the mold also plays a critical role in the shrinkage rate. A higher pouring temperature typically results in a greater shrinkage due to increased fluidity and a longer time for the metal to cool.
- Mold Material: The type of material used for the mold also influences the cooling rate and shrinkage. Molds made from different materials (e.g., silica, alumina, zircon) have different thermal conductivities, which affect the heat dissipation rate and, consequently, the shrinkage factor.
- Cooling Rate: The rate at which the molten metal cools as it solidifies inside the mold also affects the final shrinkage. Faster cooling tends to result in higher shrinkage due to the rapid contraction of the metal as it cools quickly.
- Heat Treatment: After the initial casting process, 17-4PH parts typically undergo heat treatment processes such as solution annealing and aging, which can further affect the shrinkage of the alloy and alter the final dimensions of the part.
Shrinkage in 17-4PH Stainless Steel Investment Casting
Based on empirical data from casting studies and metallurgical tests, the shrink factor for 17-4PH stainless steel is typically in the range of 1.5% to 2.0% during solidification. This means that the pattern or mold must be made slightly larger than the desired final part dimensions to account for the reduction in size during cooling and solidification. This shrink factor is a general guideline and may vary based on the factors mentioned above.
The following table provides a comparison of typical shrinkage factors for 17-4PH stainless steel in investment casting at different stages of the process:
Stage of Casting | Shrink Factor | Notes |
---|---|---|
Solidification (Initial) | 1.5% to 2.0% | Initial shrinkage during the transition from liquid to solid. |
Cooling to Room Temperature | 1.0% to 1.5% | Shrinkage due to cooling and contraction after solidification. |
Post-Heat Treatment | 0.5% to 1.0% | Shrinkage may occur during solution annealing and aging. |
Final Shrinkage | 2.0% to 3.0% | Total shrinkage from the mold pattern size to final dimensions. |
As seen in the table, the total shrinkage factor from the mold to the final part dimensions can range from 2.0% to 3.0%, depending on the casting and post-processing conditions. This variation is due to the combination of solidification shrinkage, cooling shrinkage, and the minor adjustments that may occur during heat treatment.
Shrink Factor Design Considerations
To ensure that the final dimensions of 17-4PH investment castings meet the required specifications, it is crucial to account for the shrink factor during the design and mold-making stages. In many cases, patterns are intentionally made larger to compensate for shrinkage. The pattern size is typically determined by adding the estimated shrinkage percentage to the desired final dimensions.
For instance, if a cast part needs to be 100 mm in the final form, and the shrinkage factor is estimated at 2%, the pattern would need to be made approximately 102 mm to account for the shrinkage during the casting process.
The following formula is commonly used to calculate the pattern size based on the shrinkage factor:
Pattern Size=Final Size/(1−Shrinkage Factor)
Where:
- Final Size is the desired final dimensions of the part.
- Shrinkage Factor is the estimated shrinkage (expressed as a decimal).
For example, for a part with a final size of 100 mm and a shrinkage factor of 2%, the pattern size would be calculated as:
Pattern Size=100/(1−0.02)=102.04 mm
This formula ensures that the casting compensates for shrinkage, leading to a part that meets the intended final dimensions after solidification, cooling, and heat treatment.
Conclusion
The shrink factor for 17-4PH stainless steel in investment casting is an essential consideration for ensuring the accuracy of cast parts, particularly in industries where dimensional precision is critical. With a typical shrinkage range of 1.5% to 2.0% during solidification, and additional minor shrinkage occurring during cooling and heat treatment, manufacturers must carefully account for these factors when designing patterns and molds.
By understanding and applying the appropriate shrink factor, manufacturers can achieve high-quality, dimensionally accurate castings that meet the demanding specifications of industries such as aerospace, defense, and medical devices. The application of precise shrinkage calculations is integral to the success of the investment casting process for 17-4PH stainless steel, ensuring the production of reliable, high-performance components.