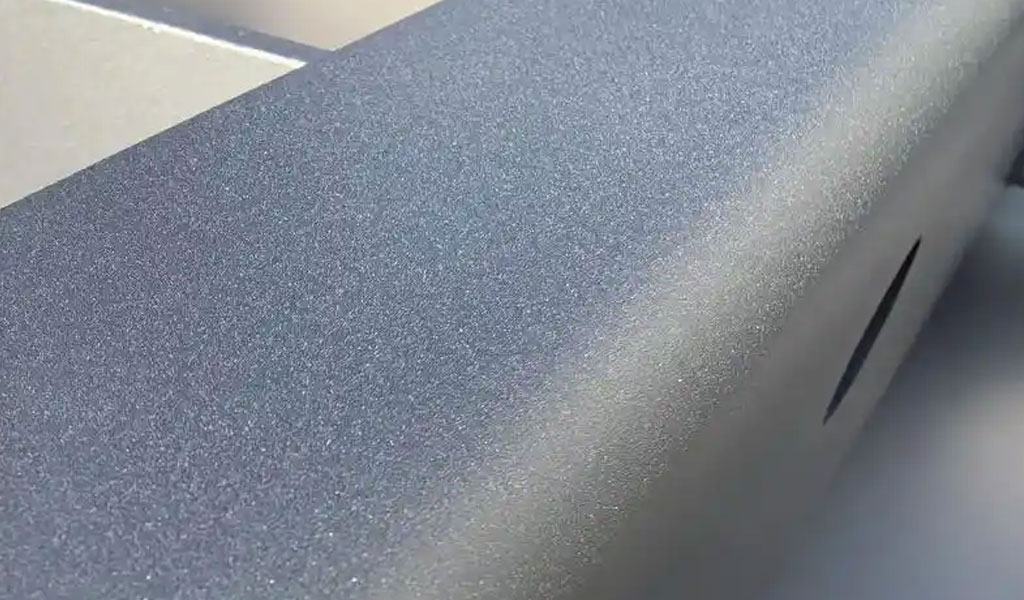
Bead blasting and sandblasting are two popular surface finishing techniques widely used in industrial and commercial applications for cleaning, deburring, and texturing metal, glass, plastics, and other materials. Although both processes share the fundamental principle of abrasive blasting, they differ significantly in the media used, the results they achieve, and the specific applications for which they are suited. Understanding these differences is crucial for selecting the most appropriate technique based on the desired outcome, material type, and intended use of the finished product.
Bead Blasting
Bead blasting is a type of abrasive blasting where small, spherical beads of abrasive material are propelled at high velocity onto the surface of a workpiece. The most common media used for bead blasting are glass beads, ceramic beads, or other rounded particles. These spherical beads produce a smooth, uniform surface finish, making bead blasting particularly suitable for applications where a fine, matte, or satin finish is required.
The primary advantage of bead blasting over other abrasive techniques is the gentle action it applies to the surface. Since the beads are rounded and not jagged, they tend to produce less aggressive abrasion, which reduces the risk of damaging or distorting the workpiece. Bead blasting is often used for cleaning, polishing, or texturing delicate parts, such as aerospace components, medical devices, and automotive parts.
Bead blasting also offers a high degree of control over the finish quality, as the size and hardness of the beads can be adjusted to achieve the desired texture. The smaller the bead size, the smoother the finish, while larger beads will create a coarser texture. The soft and non-destructive nature of bead blasting makes it ideal for finishing surfaces without causing significant material removal or surface deformation.
In addition to its surface finishing capabilities, bead blasting is also used for cleaning purposes. For instance, it can be employed to remove rust, scale, or other contaminants from metal parts without causing the damage that might result from harsher abrasive processes. This makes bead blasting a suitable option for parts that require a high degree of precision and minimal material loss.
Sandblasting
Sandblasting, also known as abrasive blasting, is a more aggressive surface treatment technique that uses sand or other angular, abrasive materials to clean, smooth, or roughen surfaces. The abrasive material, typically silica sand, is propelled at high pressure onto the surface of the workpiece using compressed air or a mechanical system.
Unlike bead blasting, sandblasting uses angular abrasives, which have sharp edges that can cause significant material removal and surface damage. This makes sandblasting more suitable for applications where aggressive cleaning or surface preparation is required, such as removing heavy rust, paint, or scale from industrial machinery, structural steel, and concrete. Sandblasting is also commonly used in the preparation of surfaces for coating or painting, as it can create a rough profile that enhances the adhesion of subsequent layers.
One of the key characteristics of sandblasting is its ability to quickly remove material, making it ideal for large-scale cleaning or surface preparation projects. However, because of the aggressive nature of the process, sandblasting can also cause surface roughening, which may not be suitable for delicate parts or those requiring a fine finish. Additionally, the use of silica sand in sandblasting has raised health concerns, as the fine silica dust can lead to serious lung diseases if proper safety measures are not taken.
Over the years, many industries have shifted away from using silica sand due to its hazardous nature, opting instead for alternative abrasives, such as garnet, aluminum oxide, or steel shot. These materials can offer similar abrasive properties while reducing the health risks associated with inhaling silica dust. Despite these concerns, sandblasting remains a popular and effective method for heavy-duty cleaning and surface preparation in industries such as construction, automotive, and shipbuilding.
Comparing Bead Blasting and Sandblasting
While both bead blasting and sandblasting are forms of abrasive blasting, their differences are significant enough to influence their choice for various applications. The most notable differences are found in the type of abrasive media used, the finish quality, and the level of aggressiveness.
- Abrasive Media: The media used in bead blasting are typically rounded particles such as glass or ceramic beads, which produce a smoother finish and reduce the risk of damaging the material. In contrast, sandblasting uses angular abrasives, like silica sand or aluminum oxide, which are more aggressive and capable of removing larger amounts of material.
- Surface Finish: Bead blasting tends to result in a smooth, uniform, matte, or satin finish, making it ideal for applications where a polished or semi-polished look is required. Sandblasting, on the other hand, produces a more textured or rough surface, which is beneficial for cleaning heavily soiled parts or preparing surfaces for coating or bonding.
- Material Removal: Sandblasting is more effective at removing material from the surface, making it a better choice for tasks such as rust removal, cleaning large surfaces, or preparing surfaces for paint or coatings. Bead blasting, while capable of cleaning and finishing surfaces, is more suited for delicate operations where minimal material removal is desired.
- Application Suitability: Bead blasting is commonly used for cleaning and finishing delicate parts in industries such as aerospace, medical, and automotive, where precision and smooth finishes are critical. Sandblasting is more suited for heavy-duty applications, including the cleaning of industrial machinery, structural components, and concrete surfaces.
- Health and Safety Concerns: The use of silica sand in sandblasting can pose serious health risks, as inhaling fine silica dust can cause respiratory diseases. While alternatives to silica sand exist, the dust produced by sandblasting remains a concern. Bead blasting, on the other hand, typically uses non-toxic materials like glass beads, which do not produce hazardous dust to the same extent, making it a safer option for workers.
Advantages and Disadvantages of Bead Blasting
Bead blasting offers several benefits for precision surface finishing:
- Gentle on Surfaces: Bead blasting is less abrasive than sandblasting, which reduces the risk of distorting or damaging delicate materials.
- Smooth Finish: It provides a smoother, more consistent finish, which is ideal for parts that require a high level of aesthetic quality.
- Reduced Surface Contamination: The spherical nature of the beads causes less contamination on the workpiece, making it more suitable for medical and aerospace components where cleanliness is critical.
However, bead blasting also has some limitations:
- Slower Material Removal: Bead blasting is less aggressive, which can make it slower for cleaning or surface preparation tasks that require heavy material removal.
- Cost: The equipment and media for bead blasting can be more expensive than sandblasting, particularly for specialized applications.
Advantages and Disadvantages of Sandblasting
Sandblasting is a versatile and efficient technique, especially for heavy-duty cleaning and surface preparation:
- Fast Material Removal: Sandblasting is highly effective at removing rust, paint, scale, and other contaminants, making it ideal for industrial applications.
- Rough Surface Profiles: It creates a rough texture, which is useful for enhancing the adhesion of coatings, paints, or adhesives.
- Cost-Effective: Sandblasting equipment and abrasives are generally less expensive than bead blasting, making it a more economical choice for large-scale projects.
However, sandblasting also comes with its drawbacks:
- Surface Damage: The aggressive nature of sandblasting can lead to surface damage or distortion, especially on delicate parts.
- Health Risks: The use of silica sand and the dust produced during sandblasting can pose serious health risks to workers without proper ventilation and protective equipment.
Conclusion
Both bead blasting and sandblasting are essential techniques in the realm of surface finishing, with each method offering unique advantages depending on the specific requirements of the application. Bead blasting is ideal for delicate, high-precision work, producing smooth, uniform finishes on parts that require minimal material removal. Sandblasting, in contrast, is more suitable for heavy-duty cleaning and surface preparation, where aggressive material removal and rough surface profiles are needed.
Choosing between bead blasting and sandblasting ultimately depends on factors such as the type of material being treated, the desired surface finish, the scale of the project, and the health and safety considerations for workers. By understanding the strengths and limitations of both techniques, manufacturers and industrial operators can select the right method for their needs, ensuring optimal results and efficiency in their surface finishing processes.