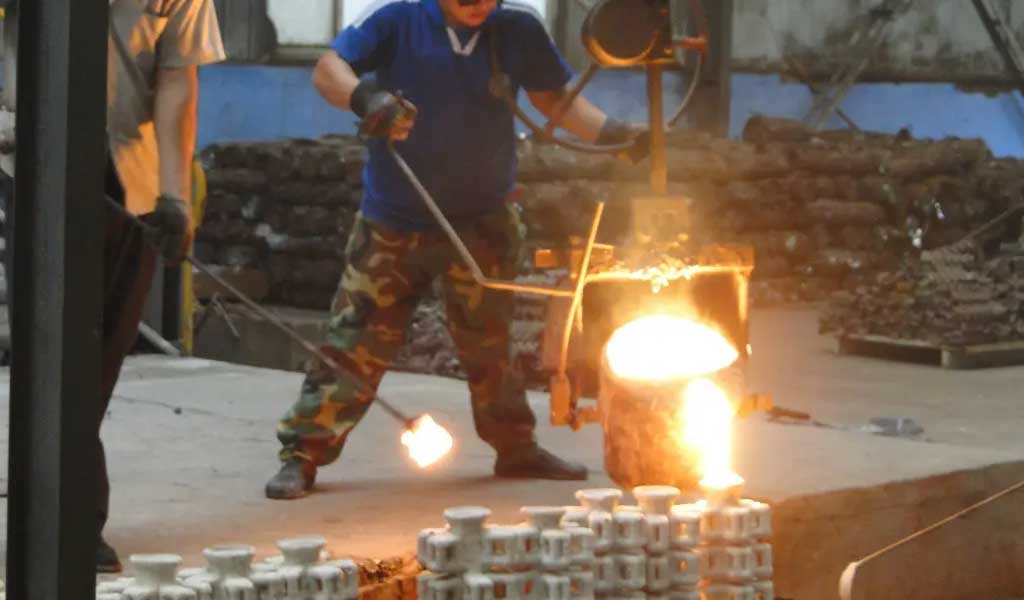
Coated sand molds are also called sand casting molds. First, use wood to make a casting (usually the material used is wood, but also metal molds), bury the wood mold in the sand, and then take out the wood mold, so that the sand It is formed into a cavity, the molten steel is poured out of the cavity, and after cooling, it is the required mold.
Non-metallic precision casting molds contain bauxite and high-temperature cement, which have the advantages of simple and convenient production, low cost, can be reused, wide range of use, and short production cycle. It can greatly save the materials for molding, save nearly 50% of labor, and can ensure the quality of castings and avoid environmental pollution.
The following explains the detailed comparison between the coated sand mold and the metal precision casting mold:
- The surface quality of the precision casting mold is high and the size is standard; the surface quality of the sand casting mold is poor, and the size is not as accurate as that of the precision casting, but the cost is lower than that of the precision casting. Low; the cost of the mold is higher than that of the sand-turning mold.
- Coated sand molds and non-metallic precision casting molds contain bauxite and high-temperature cement, and the weight ratio is: bauxite 69-86%; high-temperature cement 14-31%. Precision casting mold: first make the wax part (that is, the final shape of the mold), then hang the slurry on the wax mold, stick the sand to form a solid shell on the surface of the wax part, and then heat it to put Drain the wax, pour molten steel or aluminum water into the empty shell, smash the shell after cooling, and you can get the desired mold