Inconel, a family of austenitic nickel-chromium-based superalloys, is known for its exceptional resistance to oxidation, corrosion, and extreme temperatures. This unique combination of properties makes Inconel an ideal choice for high-stress applications in industries such as aerospace, automotive, chemical processing, and power generation. Two primary methods for manufacturing Inconel components are investment casting and CNC machining. Each technique has its advantages and limitations, which significantly impact the selection process for specific applications.
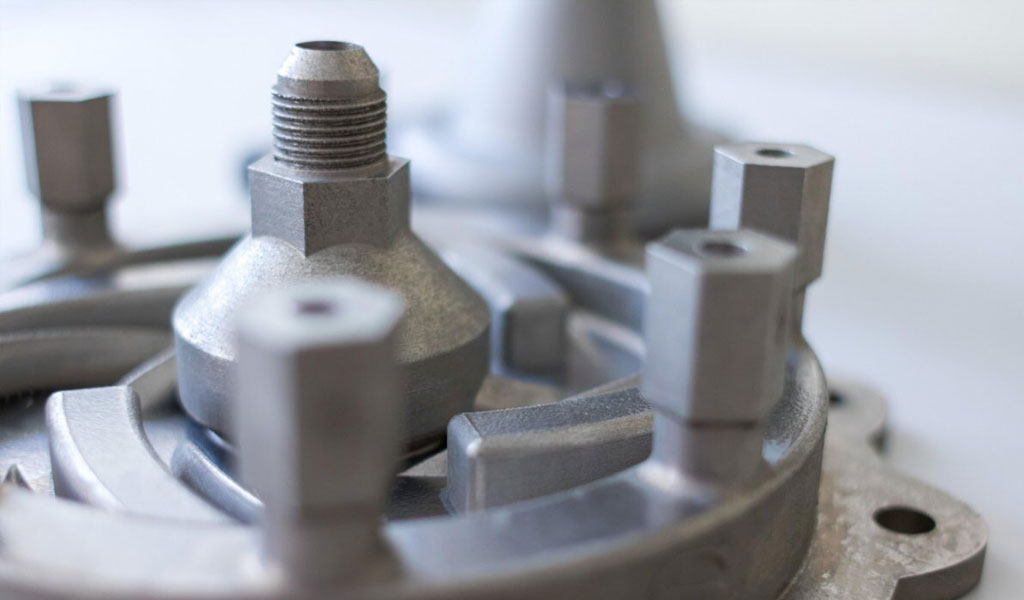
Inconel Alloys Overview
Inconel alloys, developed by the International Nickel Company, encompass a range of compositions tailored to meet various performance criteria. Some of the most widely used Inconel alloys include Inconel 600, 625, 718, and 750.
These alloys are characterized by their ability to maintain mechanical strength and stability over a wide temperature range, high resistance to oxidation and corrosion, and good weldability and fabricability.
- Inconel 600: Known for its excellent resistance to oxidation and corrosion at high temperatures, Inconel 600 is commonly used in furnace components, chemical and food processing equipment, and nuclear reactors.
- Inconel 625: With superior fatigue and thermal-fatigue strength, oxidation resistance, and weldability, Inconel 625 is ideal for aerospace, marine, and chemical processing applications.
- Inconel 718: This alloy offers exceptional tensile, fatigue, creep, and rupture strength, making it suitable for high-temperature aerospace applications, such as turbine engines and rocket motors.
- Inconel 750: Featuring high strength and excellent resistance to oxidation and corrosion, Inconel 750 is used in gas turbines, rocket engines, and various high-temperature applications.
Investment Casting Inconel
Investment casting, also known as lost-wax casting, is a precision casting process that involves creating a wax model, coating it with a ceramic shell, and then melting the wax away to create a mold.
Molten metal is then poured into the mold to produce the final component. This process is highly regarded for its ability to produce intricate and complex shapes with excellent surface finish and dimensional accuracy.
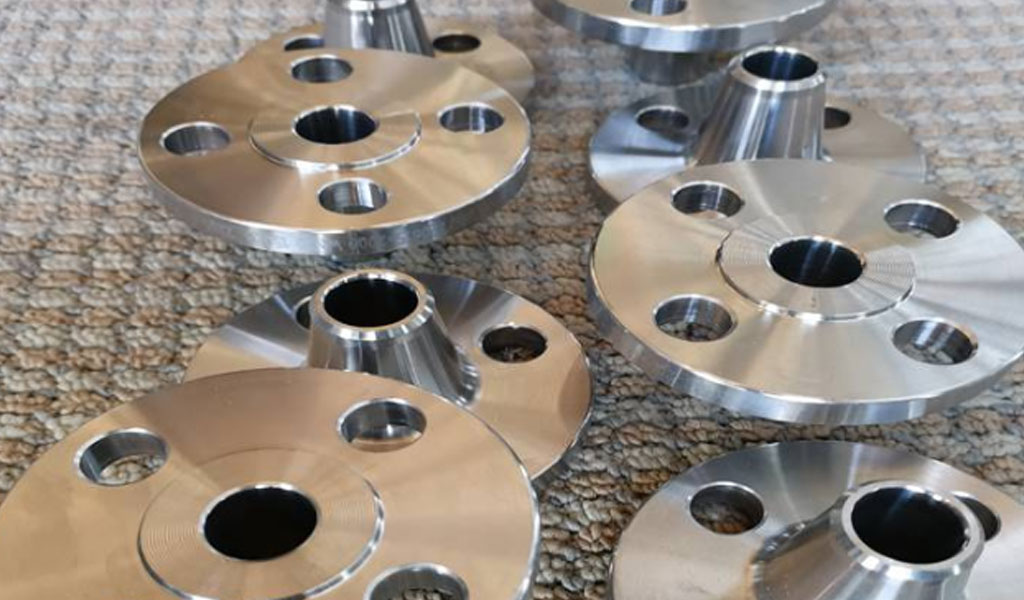
Process
- Pattern Creation: A wax pattern is created using injection molding or 3D printing techniques. This pattern replicates the final component’s geometry and dimensions.
- Assembly: Multiple wax patterns can be assembled onto a wax tree to allow for the simultaneous casting of several components.
- Shell Building: The wax pattern or tree is repeatedly dipped into a ceramic slurry, coated with fine sand, and dried to create a ceramic shell. This process is repeated until the shell reaches the desired thickness and strength.
- Dewaxing: The ceramic shell is heated in an autoclave or furnace to melt and remove the wax, leaving behind a hollow ceramic mold.
- Casting: The mold is preheated, and molten Inconel is poured into the mold to fill the cavity left by the wax pattern.
- Cooling and Shell Removal: After the metal has solidified, the ceramic shell is broken away to reveal the cast component.
- Finishing: The cast component undergoes various finishing processes, such as trimming, grinding, and machining, to achieve the desired final dimensions and surface quality.
Advantages
- Complex Geometry: Investment casting can produce highly complex and intricate shapes that would be difficult or impossible to achieve with other manufacturing methods.
- Excellent Surface Finish: The use of fine ceramic materials in the shell building process results in a smooth surface finish on the cast components.
- Dimensional Accuracy: Investment casting offers high dimensional accuracy, reducing the need for extensive post-casting machining.
- Material Efficiency: This process allows for the efficient use of material, with minimal waste and the potential for recycling excess material.
Limitations
- Cost: Investment casting can be more expensive than other casting methods, particularly for small production runs, due to the cost of creating wax patterns and ceramic shells.
- Lead Time: The process can be time-consuming, with multiple steps required to create the final component, leading to longer lead times compared to other manufacturing methods.
- Size Limitations: The size of components that can be produced using investment casting is limited by the size of the ceramic shell and the handling equipment.
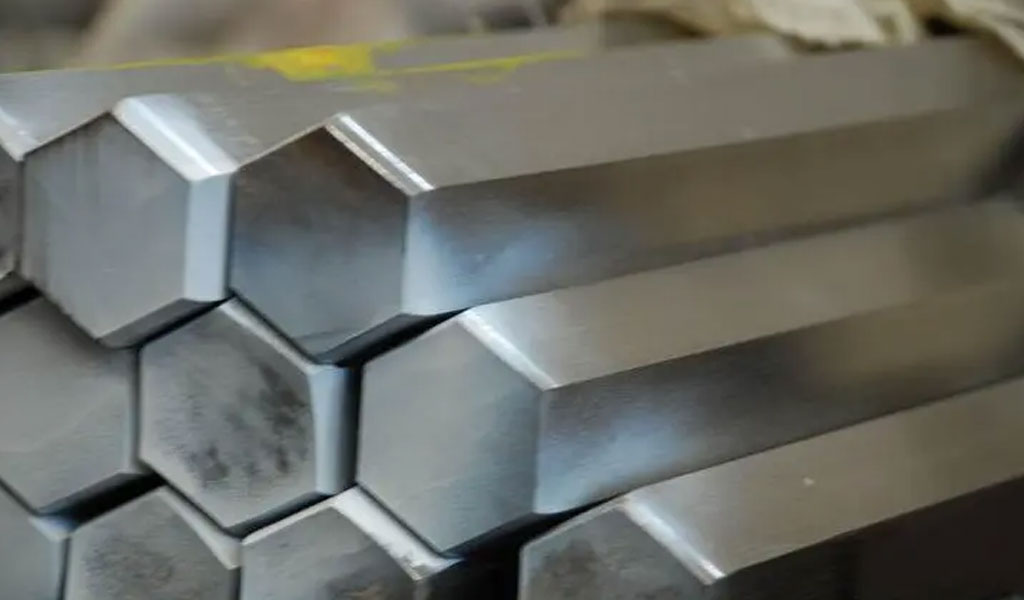
CNC Machining Inconel
Computer Numerical Control (CNC) machining is a subtractive manufacturing process that involves using computer-controlled machine tools to remove material from a solid workpiece to create the desired final shape.
Inconel CNC machining is highly versatile and capable of producing complex components with high precision and repeatability.
Process
- Design and Programming: The component’s design is created using Computer-Aided Design (CAD) software, and the machining process is programmed using Computer-Aided Manufacturing (CAM) software.
- Setup: The workpiece, typically a solid block or billet of Inconel, is secured in the CNC machine, and the appropriate cutting tools are selected and installed.
- Machining: The CNC machine follows the programmed instructions to remove material from the workpiece, using various cutting tools such as end mills, drills, and lathes.
- Inspection: The machined component is inspected to ensure it meets the required dimensional and surface finish specifications.
- Finishing: Additional finishing processes, such as grinding, polishing, and coating, may be performed to achieve the final desired properties.
Advantages
- Precision and Accuracy: CNC machining offers high precision and accuracy, making it suitable for components with tight tolerances and complex geometries.
- Repeatability: The use of computer control ensures consistent quality and repeatability across multiple production runs.
- Versatility: CNC machines can be used to produce a wide variety of components from different materials, including Inconel alloys.
- Short Lead Times: CNC machining can produce components relatively quickly, particularly for small to medium production runs.
Limitations
- Material Waste: CNC machining is a subtractive process, resulting in significant material waste, particularly for complex components with high material removal rates.
- Tool Wear: The hardness and toughness of Inconel alloys can cause rapid tool wear, increasing tooling costs and potentially affecting machining efficiency.
- Cost: CNC machining can be expensive, particularly for complex components requiring multiple setups and specialized cutting tools.
Comparison of Inconel Investment Casting and CNC Machining
Complexity and Geometry
- Investment Casting: This process excels at producing components with complex geometries, including thin walls, intricate internal features, and undercuts. The ability to create detailed wax patterns allows for the production of components that would be difficult or impossible to machine.
- CNC Machining: While CNC machining is capable of producing complex shapes, it may be limited by tool access and the need for multiple setups. However, it offers greater flexibility in creating precise features and tight tolerances.
Surface Finish and Tolerances
- Investment Casting: Investment casting typically produces components with a good surface finish, although some post-casting finishing may be required to achieve the desired final surface quality. The dimensional tolerances achievable with investment casting are generally acceptable for most applications but may not be as tight as those achievable with CNC machining.
- CNC Machining: CNC machining offers excellent surface finish and the ability to achieve very tight tolerances, making it suitable for applications requiring high precision and fine surface quality.
Material Efficiency
- Investment Casting: This process is relatively material-efficient, with minimal waste generated during the casting process. Excess material can often be recycled and reused.
- CNC Machining: CNC machining generates significant material waste, particularly for components with high material removal rates. However, the waste material can often be recycled, mitigating some of the material loss.
Production Volume
- Investment Casting: Investment casting is well-suited for medium to high-volume production runs, particularly for complex components that would be costly to machine. The cost of creating wax patterns and ceramic shells can be spread across a larger number of components, reducing the per-unit cost.
- CNC Machining: CNC machining is ideal for small to medium production runs, particularly for components requiring high precision and tight tolerances. The setup and tooling costs can be significant, but they are offset by the flexibility and speed of the machining process for lower volumes.
Lead Time
- Investment Casting: The investment casting process can be time-consuming, with multiple steps required to create the final component. This can result in longer lead times compared to other manufacturing methods.
- CNC Machining: CNC machining typically offers shorter lead times, particularly for small to medium production runs. The ability to quickly program and set up CNC machines allows for rapid production of components.
Cost
- Investment Casting: The cost of investment casting can be higher than other casting methods, particularly for small production runs. However, the ability to produce complex components with minimal post-casting machining can offset some of the initial costs.
- CNC Machining: CNC machining can be expensive, particularly for complex components requiring multiple setups and specialized cutting tools. However, the precision and flexibility of the process can justify the cost for certain applications.
Applications
Aerospace
In the aerospace industry, Inconel components are subjected to extreme temperatures and high stresses. Both investment casting and CNC machining are commonly used to produce Inconel components for aerospace applications, depending on the specific requirements of the part.
- Investment Casting: Investment casting is often used for turbine blades, vanes, and other complex components that require high strength and resistance to oxidation and corrosion at elevated temperatures.
- CNC Machining: CNC machining is typically used for components requiring high precision and tight tolerances, such as fuel system components, fasteners, and structural parts.
Automotive
In the automotive industry, Inconel is used in high-performance and high-temperature applications, such as exhaust systems, turbocharger components, and engine parts.
- Investment Casting: Investment casting is well-suited for producing complex exhaust manifolds, turbocharger housings, and other components with intricate geometries and high-temperature requirements.
- CNC Machining: CNC machining is often used for precision components, such as fuel injectors, sensors, and fasteners, where tight tolerances and high surface quality are critical.
Chemical Processing
In the chemical processing industry, Inconel components are used in environments with corrosive chemicals and high temperatures.
- Investment Casting: Investment casting is commonly used to produce complex valves, pumps, and heat exchanger components that require high corrosion resistance and strength.
- CNC Machining: CNC machining is typically used for precision components, such as fittings, connectors, and instrumentation parts, where tight tolerances and high surface quality are essential.
Power Generation
In the power generation industry, Inconel components are used in gas turbines, nuclear reactors, and other high-temperature applications.
- Investment Casting: Investment casting is often used for turbine blades, vanes, and other complex components that require high strength and resistance to oxidation and corrosion at elevated temperatures.
- CNC Machining: CNC machining is typically used for precision components, such as fasteners, instrumentation parts, and structural components, where tight tolerances and high surface quality are critical.
Conclusion
Both investment casting and CNC machining offer unique advantages and limitations for the production of Inconel components. The choice between these two manufacturing methods depends on the specific requirements of the application, including complexity, surface finish, tolerances, material efficiency, production volume, lead time, and cost.
Investment casting is ideal for producing complex geometries with excellent surface finish and dimensional accuracy, making it suitable for medium to high-volume production runs of intricate components. CNC machining, on the other hand, offers high precision, repeatability, and flexibility, making it suitable for small to medium production runs of components requiring tight tolerances and fine surface quality.
Ultimately, the selection of the appropriate manufacturing method for Inconel components should be based on a thorough evaluation of the specific requirements and constraints of the application. By understanding the strengths and limitations of both investment casting and CNC machining, manufacturers can make informed decisions to optimize the performance, quality, and cost-effectiveness of their Inconel components.