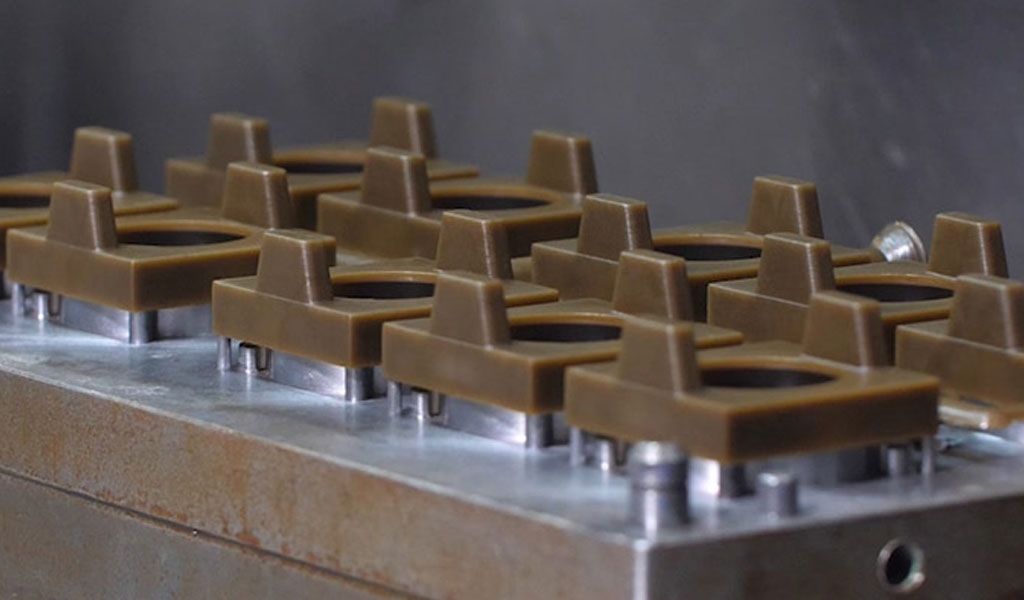
Lost wax casting, also known as investment casting, is a manufacturing process that has been used for centuries to produce complex and precise components. The process involves creating a wax model of the desired part, encasing it in a ceramic mold, and then melting the wax away to create a cavity into which molten metal is poured. While the technique offers exceptional accuracy and versatility, understanding the cost and price structure of lost wax casting is crucial for industries and individuals seeking to utilize this process. This article explores the various factors influencing the cost and pricing of lost wax casting, providing a comprehensive analysis of the underlying elements.
Material Costs
One of the primary contributors to the cost of lost wax casting is the material used. The materials required in the process include wax for model creation, ceramic materials for the mold, and the metal or alloy used for the final product. Each of these components affects the overall cost:
- Wax
The type and quality of wax used in the process can vary widely, with costs ranging based on the complexity of the part being replicated. Specialized waxes designed for precise molding and easy removal can be more expensive than standard alternatives. - Ceramic Mold Materials
The ceramic shell used to encase the wax model must be heat-resistant and durable enough to withstand the casting process. High-quality ceramic materials increase the mold’s ability to handle intricate designs but also raise production costs. - Metals and Alloys
The selection of metal significantly impacts the cost of lost wax casting. Common metals like aluminum, bronze, and steel are more economical, while exotic alloys such as titanium, Hastelloy, or Inconel are considerably more expensive due to their properties and the additional complexities in handling them during casting.
Labor Costs
Labor is a significant cost factor in lost wax casting due to the intensive, multi-step nature of the process. Each stage requires skilled workers or specialized automation to ensure precision and quality. Labor costs may include:
- Wax Model Production: The creation of a precise wax replica is a meticulous process, often requiring skilled artisans or advanced machinery for intricate parts.
- Mold Preparation: Applying multiple layers of ceramic material to the wax model involves manual or semi-automated processes. Each layer must dry and cure before the next is applied, extending the production timeline.
- Casting and Finishing: Pouring molten metal into the mold and subsequently removing the ceramic shell demand expertise to avoid defects. Post-casting finishing tasks such as grinding, polishing, or machining further add to labor expenses.
Equipment and Tooling Costs
The equipment and tooling required for lost wax casting can be significant investments for manufacturers. These costs are typically distributed across the number of parts produced, with smaller production runs incurring higher per-unit costs. Key equipment expenses include:
- Wax Injection Machines
Advanced machines for creating wax models ensure precision and consistency, but their initial cost and maintenance can add up. - Kilns and Furnaces
High-temperature kilns are essential for curing ceramic molds, while furnaces are required to melt and pour metal. Energy consumption and maintenance of these machines contribute to overall costs. - Inspection and Quality Control Tools
Equipment such as X-ray machines or coordinate measuring machines (CMM) used for non-destructive testing and dimensional inspection are vital for ensuring quality, adding to operational expenses.
Production Volume
The volume of parts produced in a casting project significantly impacts the overall cost. Lost wax casting is generally more cost-effective for medium to high production runs because the initial setup and tooling expenses can be spread over a larger number of units. However, small-batch or prototype production often incurs higher per-unit costs due to the same fixed setup expenses being amortized over fewer parts.
Design Complexity
The complexity of the part being cast is another critical factor. Intricate designs with fine details or undercuts require advanced wax model creation and more precise mold preparation. Complex parts may also need additional finishing operations, such as machining or polishing, which increase the overall cost.
Tolerance and Surface Finish Requirements
High tolerance levels and specific surface finish requirements demand greater precision during the casting process and post-processing. Achieving tighter tolerances may involve additional machining, while smooth or polished surfaces may necessitate more extensive finishing work, both of which increase costs.
Environmental and Regulatory Compliance
Lost wax casting facilities must adhere to environmental regulations concerning emissions, waste disposal, and worker safety. Compliance measures, such as air filtration systems or the safe disposal of spent ceramic materials, contribute to operating costs. Additionally, certifications like ISO 9001 or AS9100 for quality management systems can increase the cost of production but are often necessary for serving specific industries such as aerospace or medical.
Overhead Costs
Indirect costs, including facility maintenance, utilities, and administrative expenses, are allocated across the parts produced. Facilities in regions with higher energy or labor costs may experience increased overhead, affecting the final price of the cast parts.
Pricing Strategies in Lost Wax Casting
Pricing strategies for lost wax casting parts often consider both cost factors and market dynamics. Manufacturers may employ one or more of the following pricing models:
- Cost-Plus Pricing
In this model, the manufacturer calculates the total production cost and adds a markup percentage to ensure profitability. This approach is straightforward but may not account for competitive market conditions. - Market-Based Pricing
Prices are set based on industry standards and competitor pricing. This method requires thorough market analysis to balance competitiveness and profitability. - Value-Based Pricing
In cases where the lost wax casting provides unique value, such as exceptional precision or use of high-performance alloys, manufacturers may price parts higher, reflecting the added benefits to the customer. - Volume Discounts
Manufacturers often offer reduced per-unit prices for larger orders, leveraging economies of scale to attract bulk buyers.
Case Studies and Industry Applications
Lost wax casting is utilized across various industries, including aerospace, automotive, medical, and art. Each application imposes unique cost considerations:
- Aerospace Industry
Aerospace components often require high-performance alloys and strict tolerance levels, leading to higher costs. However, the ability to produce lightweight and complex parts justifies the expense. - Medical Industry
Implants and surgical tools made through lost wax casting must meet stringent biocompatibility standards, adding to material and quality control costs. - Automotive Industry
Lost wax casting is used for producing intricate engine components and high-performance parts. While cost is a factor, the method’s precision and durability benefits outweigh alternatives in certain cases. - Art and Jewelry
The process allows artists to create detailed sculptures and jewelry pieces. Smaller production volumes and the use of precious metals like gold or silver increase costs in this application.
Conclusion
Lost wax casting remains a preferred manufacturing method for creating complex and precise parts. Understanding the cost and price dynamics of the process is essential for making informed decisions in production planning and procurement. By considering material costs, labor, equipment, design complexity, and other factors, industries can optimize their use of lost wax casting to achieve a balance of quality and cost-effectiveness.