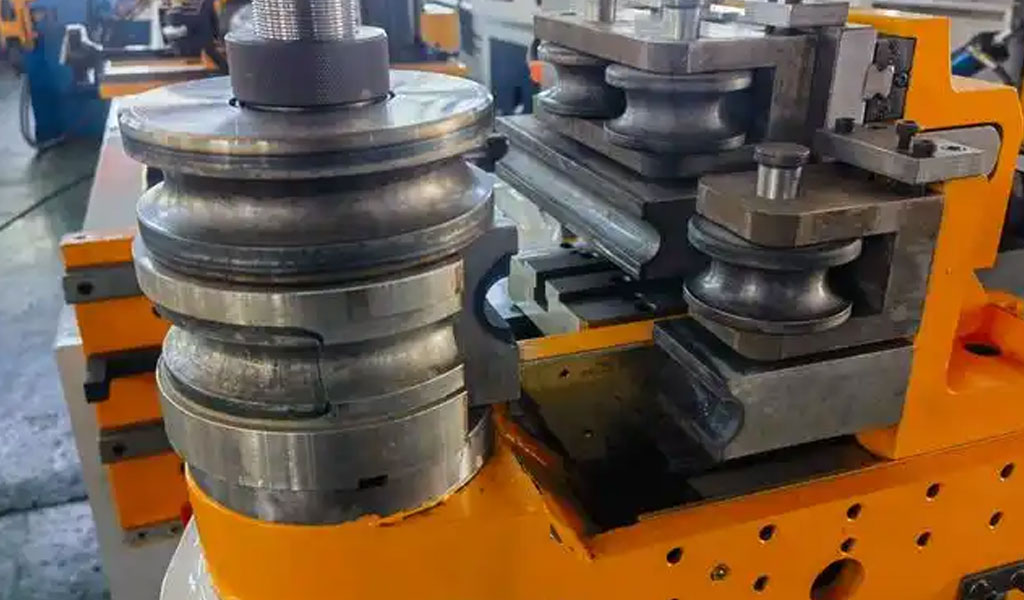
CNC (Computer Numerical Control) machining has revolutionized the manufacturing industry by offering precise control over machining operations. In the context of pipe bending, CNC technology plays a crucial role in ensuring that the bending process is highly accurate and efficient, particularly in industries such as aerospace, automotive, energy, and construction. A critical aspect of CNC machining for pipe bending is the proper conversion of various parameters to ensure the desired bend characteristics, such as angle, radius, and geometry, are met with precision. Parameter conversion in CNC pipe bending involves the translation of design parameters into machine-specific commands that control the motion of the bending tools.
Introduction to CNC Pipe Bending
Pipe bending is a manufacturing process used to create curved sections of pipe or tubing. The process can be performed manually, using hydraulic or mechanical benders, or through more advanced techniques such as CNC pipe bending. CNC pipe bending machines are equipped with a set of motors and controllers that receive input from a computer program, which allows for high levels of automation and precision.
In CNC pipe bending, the bending machine follows a set of instructions based on the parameters defined in a 3D design file, typically a CAD (Computer-Aided Design) or CAM (Computer-Aided Manufacturing) file. These instructions are then converted into machine-readable code, usually in the form of G-code or other specialized machine languages. The G-code contains commands for the machine’s movement along multiple axes, controlling various components such as the bending die, pressure die, clamping systems, and material feeders.
The Importance of Parameter Conversion
One of the most important tasks in CNC pipe bending is the conversion of design parameters into machine-readable commands. These parameters dictate the specific characteristics of the bend, including bend angle, bend radius, pipe diameter, material properties, and tooling specifications. An accurate conversion of these parameters ensures that the machine executes the bending operation correctly, resulting in parts that meet the required specifications.
The parameters involved in CNC pipe bending can be broadly categorized into several groups, including geometric parameters, material properties, machine settings, and tooling characteristics. Each group of parameters must be carefully considered and converted to ensure the bending process is both accurate and efficient.
Geometric Parameters in Pipe Bending
The geometric parameters are perhaps the most straightforward in CNC pipe bending. They refer to the dimensions and shapes of the bend and pipe. These parameters are usually specified in the design phase and include:
- Bend Angle: The bend angle is the degree to which the pipe is bent, typically measured in degrees (°). The CNC machine must accurately control the rotation of the bending die to achieve the desired angle.
- Bend Radius: The bend radius is the radius of the curve created during the bending process. It is often related to the pipe’s diameter and can be specified as a multiple of the pipe’s diameter (e.g., 1D, 2D, 3D). The radius is critical because it influences the pipe’s deformation, with tighter radii generally increasing the risk of buckling, wrinkling, or fracture.
- Straight Length: The straight length refers to the length of the pipe that remains straight before or after the bend. It is important for CNC machines to recognize the correct straight length to properly position the pipe within the machine.
- Centerline Radius: The centerline radius defines the radius from the centerline of the pipe, which is crucial in determining the exact bend geometry and ensuring that the bending die is correctly positioned in relation to the pipe.
- Bend Orientation: The orientation of the bend specifies whether the pipe bends in a horizontal or vertical direction, which affects the setup of the machine and the programming of the bending cycle.
Material Properties and Their Influence on Bending Parameters
The material properties of the pipe being bent are another critical aspect of parameter conversion in CNC pipe bending. Different materials have different mechanical properties that affect how they respond to bending forces. These properties include:
- Yield Strength: The yield strength of the material is the stress at which it begins to deform plastically. For CNC pipe bending, the yield strength directly impacts the maximum allowable bending angle and radius. Materials with higher yield strengths require more force to bend and are less prone to excessive deformation.
- Tensile Strength: Tensile strength is the maximum stress that the material can withstand while being stretched or pulled. Materials with high tensile strength are less likely to fail during the bending process but may require more power from the machine to achieve the desired bend.
- Ductility: Ductility is the ability of a material to undergo significant plastic deformation before rupture. More ductile materials, such as certain alloys and plastics, are easier to bend without cracking or breaking.
- Springback: Springback refers to the tendency of a material to return to its original shape after bending. This is a particularly important consideration in CNC pipe bending, as the machine must compensate for the material’s tendency to spring back after the bending process.
- Hardness: The hardness of a material also influences its ability to be bent. Harder materials are generally more resistant to deformation, making them more difficult to bend without inducing damage or defects.
These material properties must be taken into account when programming the CNC machine to ensure that the correct amount of force is applied during the bending process and that the material’s limitations are not exceeded. Parameter conversion must therefore include the translation of material data into machine-specific instructions that control the bending force, speed, and angle.
Machine Settings and Tooling Parameters
The settings of the CNC pipe bending machine, including the tool parameters, play a significant role in the final outcome of the bending operation. These parameters include:
- Bending Die Size and Shape: The bending die’s size and shape directly affect the bend radius and the pipe’s deformation. A die with a smaller radius will result in a tighter bend, while a larger die will produce a broader curve. CNC systems must convert the design’s bend radius into the appropriate die selection and positioning.
- Pressure Die and Clamp Positioning: Pressure dies help support the pipe during the bending process, preventing it from buckling or collapsing. The clamping system holds the pipe in place while it is being bent. Proper positioning of these dies is crucial for accurate bends, and CNC machines must precisely position these elements based on the design parameters.
- Feed Speed and Rotation Speed: The speed at which the pipe is fed into the bending machine, as well as the rotation speed of the bending die, must be optimized for the material and pipe size. Faster feed speeds can increase productivity, but may also increase the risk of poor bend quality or material failure.
- Springback Compensation: As mentioned earlier, springback is an important consideration in CNC pipe bending. Many CNC machines include springback compensation features that automatically adjust the machine’s movements based on the material’s springback properties. This ensures that the final bend matches the intended design, even after the material’s tendency to return to its original shape is accounted for.
CNC Programming and Parameter Conversion
In CNC pipe bending, the process of parameter conversion begins with the design data, which is often generated in CAD software. The design file is typically translated into a machine-readable format, such as G-code or another machine language. During this conversion, the geometric parameters (bend angle, radius, etc.) and material properties (yield strength, tensile strength, etc.) are incorporated into the machine’s program. The CNC program instructs the machine on how to move its various components (such as the bending die, clamping system, and pressure die) to achieve the desired result.
To perform parameter conversion, CNC systems use sophisticated algorithms and mathematical models that take into account factors such as material properties, machine constraints, and tooling requirements. The conversion process can involve both simple calculations and complex simulations, depending on the level of sophistication of the machine and the complexity of the design.
For instance, the machine must calculate the optimal amount of force to apply to the pipe to achieve the desired bend angle without exceeding the material’s yield strength. The machine also needs to take into account the springback effect by adjusting the bend angle to compensate for the material’s tendency to straighten after the force is removed.
In advanced CNC systems, the program can also incorporate real-time feedback from sensors and measuring devices, which continuously monitor the bending process and adjust the machine’s operations to ensure accuracy. These systems can automatically detect variations in material properties, pipe geometry, or machine performance and make corrections as needed during the bending cycle.
Challenges in Parameter Conversion for Pipe Bending
Despite the advanced capabilities of modern CNC machines, parameter conversion in pipe bending can still be challenging. Some of the key challenges include:
- Material Variability: Even within the same material type, there can be variations in material properties due to differences in manufacturing processes, heat treatment, or material age. This variability can affect the bending process, and accurate conversion requires careful consideration of the material’s specific characteristics.
- Complex Geometry: Bends that involve complex geometries, such as multi-plane bends or bends with tight radii, can be difficult to program accurately. In these cases, advanced algorithms and simulations are required to ensure that the bending process does not result in defects such as wrinkles, cracks, or kinks.
- Springback Variability: Springback can vary depending on the material, the bend angle, and the radius, making it difficult to predict precisely. While CNC machines can incorporate springback compensation, this is not always perfect, and adjustments may still be necessary.
- Tool Wear and Maintenance: Over time, the bending dies and other tools used in CNC pipe bending can wear out, affecting the quality of the bends. Regular maintenance and calibration are necessary to ensure that the machine performs optimally, and this can impact the accuracy of parameter conversion.
- Programming Complexity: For highly complex parts or assemblies, the programming process can be time-consuming and prone to error. In such cases, more sophisticated software tools and simulations are required to help ensure that the bending process is performed as intended.
Conclusion
Parameter conversion in CNC pipe bending is a critical aspect of the manufacturing process that ensures accurate, high-quality bends. By taking into account geometric parameters, material properties, machine settings, and tooling requirements, CNC machines can precisely control the bending process to produce parts that meet the desired specifications. While challenges such as material variability, complex geometries, and springback remain, advancements in CNC technology and programming techniques continue to improve the accuracy and efficiency of the process. As industries demand increasingly complex and precise pipe bending operations, the role of parameter conversion in CNC machining will continue to evolve, playing a pivotal role in the success of modern manufacturing.