WHAT IS SAND CASTING
Sand casting is a common forming method that mainly uses sand as a raw material to prepare a casting mold and pours a metal melt into the cavity of the casting mold (common sand casting production process, as shown in Figure 1-5). This technology can realize the preparation and forming of large and complex parts. It has the characteristics of good fluidity, fast and rapid forming, low cost, and low sensitivity to size and weight. Therefore, in the production of large auto parts, sand casting is often used. forming method.
However, sand casting technology also has disadvantages such as complicated mold making and mold modification, many structural design restrictions, large modulus of complex castings, and harsh production environment.
There are many types of sands that can be used for sand casting process, including green sand, resin sand, pre-coated resin sand, water glass dry sand etc. Accordingly, the sand casting processes include floor molding, automatic molding and shell molding process.In the total metal casting output in the whole world, 60% to 70% of metal castings are sand castings. Their unit weight could from dozens of gram to dozens of tons, and their dimensions could be from dozens of millimeters to several meters. Moreover, according to the castings produced by other casting processes, sand castings are the cheapest and have very high production rate.However, nowadays, the other casting processes are also use the sand to make the mold. They have their own names, such as shell mold casting, furan resin coated sand casting (no bake type), lost foam casting and vacuum casting.Need mold making and sand casting supplies for large quantities of production parts? Looking for a more cost effective and time efficient way of manufacturing parts? Don’t miss our sand casting services! At BE-CU foundry, we provide high quality and affordable sand casting service for prototypes and production parts with quick turnaround times.
Top Sand Casting Manufacturer Company China – Mold Making Service Online
Invest-casting.com is one of the best sand casting suppliers and mold makers in China, offering sand castings solutions for every industry, including medical castings, electrical castings, automotive castings and more. In order to meet our clients’ large demand for casting parts, we cooperate with reliable partners to offer sand casting services, which can make up for your one-stop requirements for casting prototype and mass production. Our main services offering include shell mold casting, furan resin coated sand casting, lost foam casting, vacuum casting, as well as with CNC machining. With more than 30 years of experience, we are able to produce custom affordable green sand casting parts, sand casting mold and 3d printing sand casting parts according to customers’ specifications, drawings or samples.Materials worked with include ASTM steel alloys and chrome iron and carbon, martensitic alloy and nickel-based steels. Utilizes coreless furnaces with 500 to 10,000 pound size and 50,000 gross pounds per shift melting capacities, AOD with 6,000 pounds rate and heat treat furnaces with up to 2,175 degrees temperature. Provides grinding, welding and non-destructive testing services. We own advanced techniques, highly skilled staff that employ superior tooling and metal casting processes to ensure that the mold parts are of the cheapest price and highest quality. Whether you need rapid tooling, mass production mold making with tight tolerances, our team of experienced specialists can offer a cost-effective solution at each stage. Contact our expert team and get a price for your tooling/mold making service, we will quote you a sand casting mold and parts price in 24 hours!
-
304 Stainless Steel Sand Casting Components
-
Automotive Shock Absorber Bracket By Casting Iron
-
Gravity Casting A3 Iron Hole Punch Rough
-
A3 Cast Iron Pipe Fittings And Sand Casting Valve Body
-
Sand Cast Brass Fittings For Machinery
-
H59 Brass Sand Casting Ornaments
-
Aluminum Sand Casting 2D X Production Line Rack
-
Aluminum Sand Casting BBQ Bakeware
-
Clay Dry Aluminum Sand Casting Robot Hand Parts
In the sand casting process, the change of parameter conditions will obviously affect the flow and solidification process of the melt in the cavity, resulting in different changes in the microstructure and mechanical properties of the casting. Therefore, according to the characteristics of sand mold and casting material, designing reasonable sand casting process parameters is a necessary condition to ensure the quality of castings. In sand casting, the key process parameters that affect the casting quality include: resin additive content, preheating temperature, initial pouring temperature, pouring time and pouring system design, etc. By optimizing these process parameters, we can obtain good forming quality and performance. The best casting products.
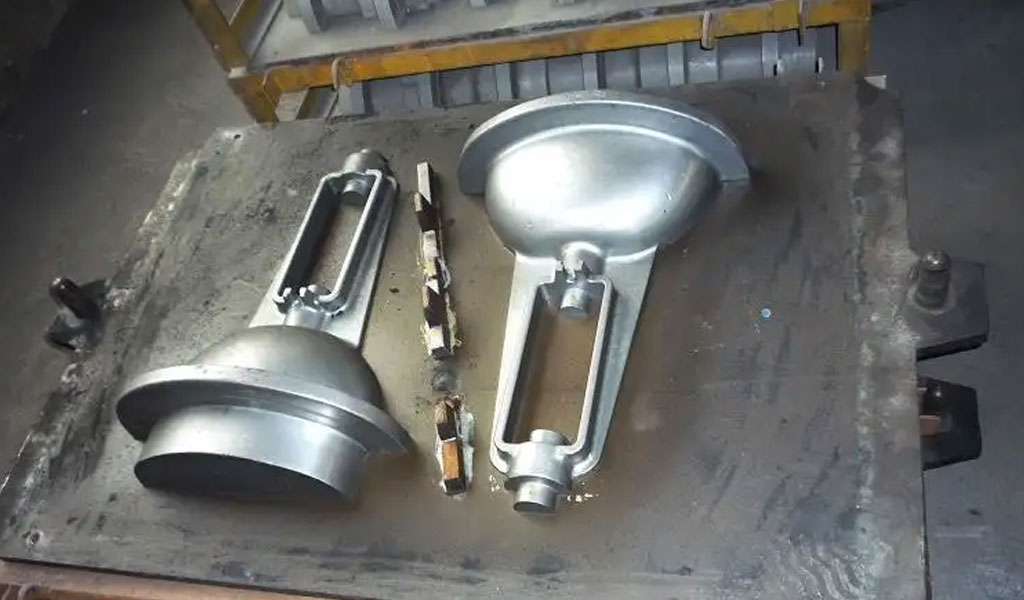
Resin additive content
Mold preheating temperature
Pouring initial temperature
Filling speed
Gating system design
3D Printing Sand Casting
At present, traditional manufacture technology is difficult to produce complex parts, while 3D printing sand casting, as a new casting method, is not sensitive to the complexity of parts. Therefore, combining the advantages of 3D printing with the advantages of traditional casting, it can realize the “integrated, short cycle, high precision and high value-added” manufacturing of casting products, and the advantages of fast production response, high efficiency, and low research cost. This technology can also meet the increasing needs of lightweight, green and intelligent equipments, and has broad application prospects in the fields of automotive, ship, aerospace and other industries.
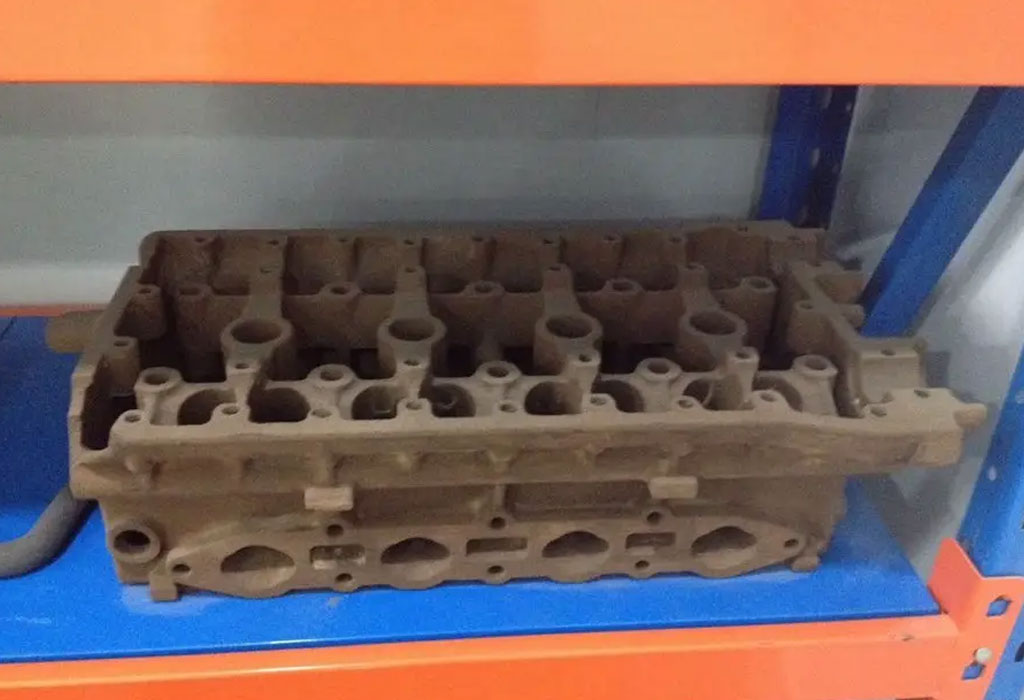
With the emergence of the concept of intelligent factory and intelligent production, traditional manufacturing industry has begun to seek new technological growth points in the environment of “manufacturing power”, and “3D printing technology”, known as the new generation of industrial revolution, has begun to promote this a process.
Based on the concepts of rapid prototyping and topology design, the technology is gradually applied to traditional industrial manufacturing fields, such as the production of complex components for automobiles, ships, rail transit and aerospace. In the process of moving from a manufacturing country to a manufacturing power, my country’s basic manufacturing industry has been continuously upgraded and transformed, and high-precision manufacturing has been further developed. The demand for some high-value-added parts and components is also growing rapidly, especially aerospace and automotive castings manufacturing. and other mechanical components with critical feature requirements. The material and design of these parts have changed a lot compared to the traditional concept, and the manufacturing process and method need to be changed [4,5]. It is common that multiple traditional functional parts are gradually integrated and integrated, thereby reducing the occurrence of fatigue fractures or potential accidents at the joints during use.
The industrial scale of the 3D printing (additive manufacturing) market will also be huge under this trend. In recent years, major manufacturing enterprises in my country have begun to introduce 3D printing equipment or production lines one after another, and try to use this technology for industrial upgrading. Because the current traditional manufacturing parts production technology is generally more sensitive to complex parts, the production of a complex part often requires multiple sets of molds, and then splicing, testing and other processes. Those complex parts with high timeliness requirements are extremely disadvantageous in actual production. 3D printing technology has the advantage of being less sensitive to the complexity of parts, thereby reducing the production cost of complex structural parts and improving the production efficiency. However, the current 3D printing metal parts technology cannot meet the application standards of parts in terms of forming size and efficiency, and there is still a certain distance from the actual production application.
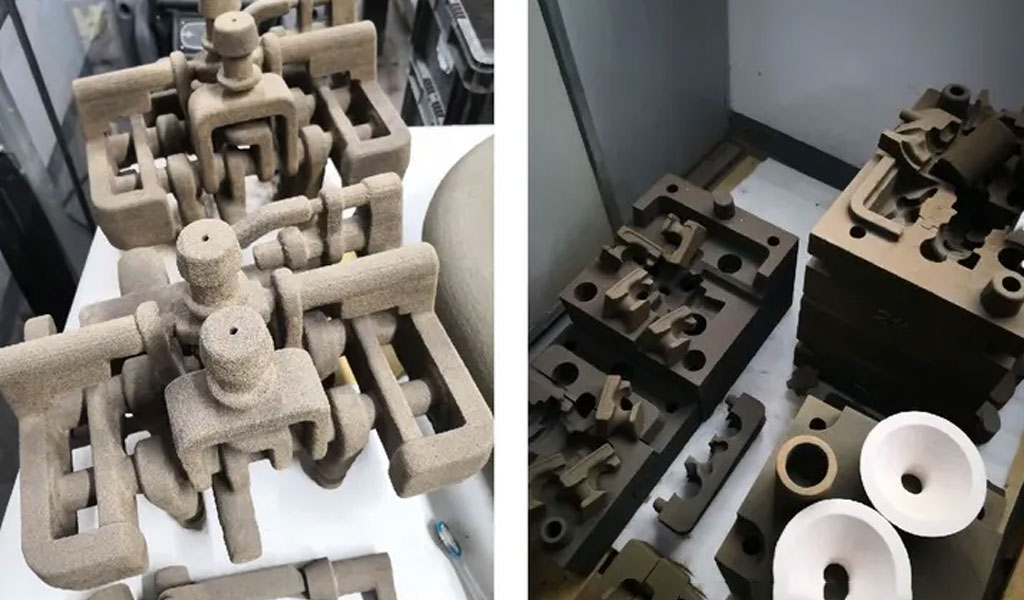
The Advantage Of 3D Printing Sand Casting
With the globalization of the economic market, the accelerated iterative upgrade of the product system, and the continuous increase in the demand for design and development, it has begun to profoundly affect the traditional foundry industry. It is required that the traditional industrial model must be transformed and upgraded as soon as possible, and new technological growth points must be found to meet the market demand. As one of the representative technologies of the new industrial revolution, 3D printing technology is gradually being applied to the traditional casting field.
This technology is not sensitive to the complexity of the product, and combined with the advantages of the traditional casting industry, it will burst out huge technological advantages.
- The application fields of 3D printing are mainly divided into two aspects: direct forming and indirect forming of parts. The direct forming method of parts mainly includes: powder bed melting technology, material jetting technology, directional energy deposition technology, etc.; the method of indirectly forming parts by printing a mold is mainly adhesive jetting technology. Because the cost value of metal powder is high and the utilization rate is low, casting 3D printing mainly adopts the method of indirect forming parts, that is, after using 3D printing equipment to print the mold, and then using the molten metal casting technology, Figure 1-5 Production process for 3D printing sand casting process.
- 3D printing sand casting abandons the traditional manufacturing processes such as wooden molds and metal molds, and directly realizes the integrated manufacturing and shaping of the required sand molds. This technology does not require manual intervention, greatly improves the production efficiency of sand molds for complex parts, improves the production environment, reduces the overall production cost and manufacturing risk, and realizes the controllable production of sand mold preparation parameters.
- When 3D printing technology and traditional manufacturing technology are combined into 3D printing sand mold rapid casting technology, it has many advantages. For example: use binder and sand to print, bond and cure layer by layer, without the need for complex and expensive molds, to achieve economical production of parts; ideal prototype manufacturing and parts optimization, molding multiple parts at one time, no external frame restrictions , with fast efficiency, etc.; the product takes only a few weeks from design delivery to solid molding, without complicated procedures such as mold opening and mold trial, which greatly optimizes the production efficiency and level of the product.
- Compared with traditional modeling techniques, 3D printing has fewer restrictions, and product personnel can obtain the most detailed geometric contours without thinking about structural difficulties such as demolding and chamfering. And unlike metal 3D printing, binder jet printing does not require extra brackets, the unused sand can be recycled after printing, and the printed sand can also be used for other purposes through technical processing, so as to truly achieve green sand castings, zero waste discharge