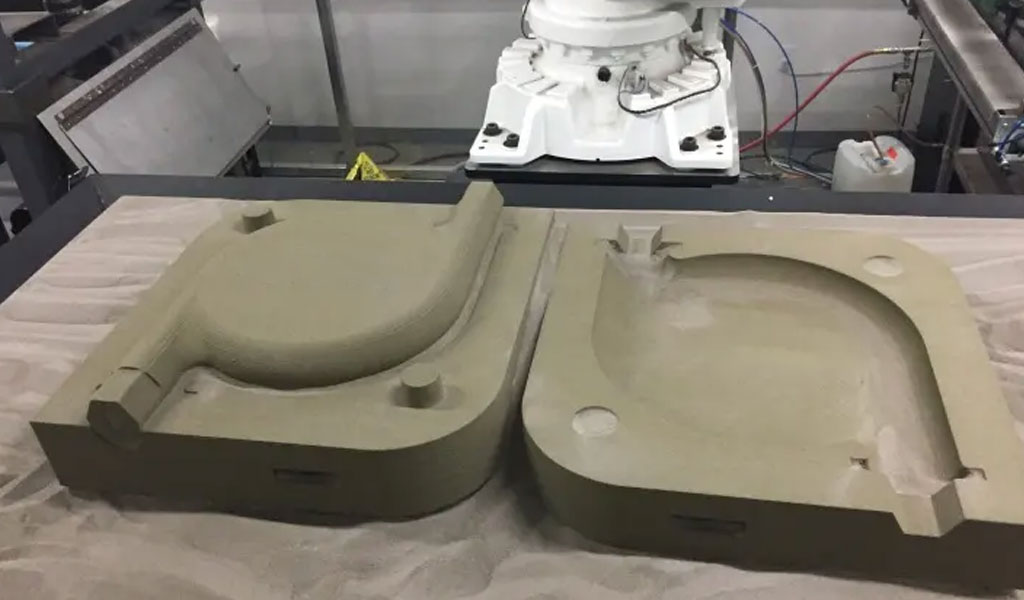
Additive manufacturing technology realizes the process of directly forming solid parts from 3D model data, which has the characteristics of short cycle, high precision and complex parts. The combination of additive manufacturing technology and casting can improve the production efficiency, reduce the cost, and expand the application field and development direction of casting technology. The technological process and forming principle of additive manufacturing are introduced, and the specific process and practical application of additive manufacturing technology in investment casting and sand casting are described respectively.
Key words:additive manufacturing; investment casting; sand casting; application
Casting is an important part in the field of material forming. Compared with other forming technologies, its production cost is relatively low and its process flexibility is large, and it can produce castings with complex structures and large sizes.With the rapid development of the modern product manufacturing industry, the product replacement interval is shortened, and the needs of users are gradually becoming more personalized and diversified. The problems existing in the traditional casting process are gradually emerging. And the change of size has an impact on the design and production of the mold, and it is difficult to meet the market demand [2]. Additive manufacturing technology, also known as rapid prototyping technology or 3D printing technology, has quickly attracted worldwide attention for its high efficiency, high quality, high flexibility and low cost since its inception.
Additive manufacturing technology breaks the shackles of traditional preparation processes, integrates computer three-dimensional design, laser technology, new processes, and new materials, and directly prepares various structures of metal or Non-metal parts have the advantages of no mold, short cycle, low production cost in small batches, and reduced manufacturing complexity. Additive manufacturing technology and traditional casting technology are combined to complement each other’s advantages, improve casting flexibility, shorten production cycle, and improve production efficiency It is of great significance to the development and reform of the modern foundry industry to ensure product quality and precision, ensure product performance, and achieve single-piece small batch production.This paper will introduce the characteristics and process flow of additive manufacturing technology, and on this basis, discuss the application of additive manufacturing technology in the foundry industry, especially the process and application of rapid investment casting and rapid sand casting.
Laser Additive Manufacturing Technology
The rapid popularization of solid CAD software and the rapid development of technologies such as lasers, new materials, and new processes have laid the foundation for the development and application of additive manufacturing processes, which not only effectively guarantees a wide range of material sources and higher material utilization for additive manufacturing. It is widely used in aerospace, shipbuilding, automobile, construction, medical equipment and other fields.
Additive manufacturing is based on the principle of discrete-stacking, which converts 3D data into 2D sections, and then stacks the sections layer by layer into 3D solid parts. First, the three-dimensional solid data is sliced and layered by the slicing software, and the layered profile section data of the specified height is generated, and then the data is imported into the software control system of the molding machine. A layer of powder “prints” a section to form a sheet of a certain thickness, and then a new layer of powder is applied to print a new layer of section, and so on repeatedly to obtain a complete part. At present, additive manufacturing technology has included many forms, such as stereolithography (SLA), selective laser melting (SLM), selective laser sintering (SLS), fused deposition (FDM), three-dimensional inkjet printing (3DP) and so on.
The Application Of Laser Additive Manufacturing In Investment Casting
Investment manufacturing technology has high precision, convenient operation, and good repeatability, and is an important part of the part preparation process. However, precision casting requires the use of molds, and is affected by the structure and size of the castings. The stainless steel casting takes weeks or even months. , increasing the application cost of castings. The introduction of additive manufacturing technology can omit the step of mold manufacturing, and can directly obtain precision wax molds with excellent coating and hanging properties. Combined with traditional casting processes, parts can be easily and quickly prepared, achieving high precision, high quality, and low casting costs. Cost, short-cycle production targets.
1.Rapid Investment Casting
The combination of additive manufacturing technology and investment casting process forms the rapid investment casting technology. Slurry, hanging sand treatment, then roasting and dewaxing to obtain the shell, and finally pouring and demoulding to obtain castings
Rapid Investment Casting Wax Pattern
- Data processing Use 3D CAD software to design three-dimensional graphics, and use related repair software (such as Magics RP) to automatically repair or manually repair defects such as bad edges and holes in the model; In order to improve the utilization rate of raw materials, the model needs to be hollowed out. In the process, the influence of structural strength and other factors is comprehensively considered. The hollow wall thickness of the wax model is controlled to 10 mm, and the minimum wall thickness is 5 mm; In one sintering molding, it is necessary to divide and sinter the model into blocks; finally, the model is sliced to obtain the profile section data of the specified thickness. The slicing process directly affects the dimensional stability, surface finish and production efficiency of the wax mold. Therefore, the slicing process is formulated. During the process, it is necessary not only to meet the requirements of the design documents, but also to determine the process parameters of the slicing under the premise of taking into account the quality and efficiency. The generally selected layer thickness parameters are 0.1~0.3mm, and the scanning spacing is 0.2~0.5mm.
- Printing Import the processed data into the printing device, and prepare the powder material that is evenly spread on the workbench. The laser beam is irradiated according to the specified path, the powder is melted and solidified, and a section is printed to form a sheet of a certain thickness. After printing one layer, lay a new layer of powder, and then print a new layer of cross-section, and so on repeatedly to obtain the required wax mold. The specific operation principle of the equipment is shown in Figure 3.
- Wax dipping Wax dipping is a post-processing process for additive manufacturing of wax molds. The main purpose is to improve the surface quality of wax molds and the adhesion to coatings, improve the surface quality of castings, and prevent the chemical reaction between wax molds and certain coatings. . The principle of this process is to immerse the sintered wax mold in liquid wax of a certain temperature, keep it for a certain time, so that the wax material can fully immerse into the tiny gap of the wax mold, and then use coarse to fine sandpaper for careful grinding. , so as to obtain a wax model with excellent surface quality.
Shell coating, demolding and pouring
- The inorganic binder for shell coating is mixed with silica powder of a certain fineness and additives into a brushing slurry of a certain viscosity, and the wax mold is immersed in the slurry to hang the paste. Sand the surface and dry in the shade. Repeat the above process for 8 to 12 times. Except for the first layer, sanding is applied layer by layer. After the shell is finished, it should be dried in the shade for 24 hours. The types of molds that are usually made are silica sol molds and water glass molds.
- Demoulding and demoulding are carried out after the shell making process. Demoulding used to be the main influencing factor restricting the wide application of additive manufacturing technology in the investment casting industry. However, with the development of new materials, this problem has been basically has been solved. The newly developed mixed material (decomposition temperature is only 260 ℃) is selected, supplemented by a certain number of ventilation holes and slag collectors to prevent the expansion shell from damaging the mold shell, and then the wax mold can be completely removed after high temperature roasting (800~950 ℃). , and after the additive manufacturing wax mold is fired, the ash powder residue is much less than 0.05%.
- Pouring and post-processing According to the relevant requirements of different types of alloys and parts, choose different casting methods, such as gravity casting, vacuum suction casting, die casting in pressure tanks, etc. After pouring, it is cooled and finally post-treated to obtain the final casting.
2.Rapid Sand Casting
Rapid sand casting is a new type of casting technology formed by the combination of additive manufacturing technology and traditional sand casting. The prepared castings meet the relevant properties of the parts. For traditional and complex parts casting, the sand core needs to be divided into several or even dozens of small sand cores, and then the same number of molds must be designed and manufactured, resulting in time-consuming and laborious sand core manufacturing, and poor overall accuracy of the sand core after splicing. Rapid sand casting avoids the process of repeated design and manufacture of molds, and its process is greatly shortened than that of traditional sand casting, and sand cores of any complex shape can be formed at one time. At the same time, rapid sand casting has high precision and high forming speed. Accuracy reaches ±0.2 mm [9,10]. Through optimized design of metal castings, casting performance can be greatly improved, thereby potentially transforming the sand casting industry’s potential to produce high-quality castings.
The preparation process of sand core additive manufacturing castings is shown in Figure 7. The three-dimensional model that needs to be cast is designed by computer, including the design of multiple ideas such as gating and riser system, anti-deformation, subsidies, and scale, and then using casting CAE The software simulates filling and solidification, and predicts possible defects such as air entrainment, sand flushing, cold insulation, stress concentration, and excessive deformation, so as to further optimize the results and form the best process plan.
After obtaining the best process, the corresponding data is used for laser sintering of the sand core and outer mold on the printing equipment. After the sand mold is cleaned, it needs to be baked and cured. After the sand mold is formed, the strength can only reach 0.75 MPa, which is not enough for sand casting, so secondary curing is required. During the molding process, only the laser-scanned positions between the sands have the strength of the connection, while the unscanned positions have basically no strength, and the strength of the sand core after molding is not enough for sand casting, so secondary curing is required. If there is no suspended structure in the structure of the sand mold, it can be directly placed in the oven together with the pick-up plate, the temperature is 180 °C, and the time is 1-5 h. The larger the sand mold, the longer the time. If the sand mold has a suspended structure, place the sand mold in a curing box, fill it with glass beads with a diameter of 1~2 mm, and put it in an oven. , the more glass beads are buried, the longer the time. For the core with large volume and complex internal structure, the phenomenon of incomplete curing is prone to occur. The glass beads can be removed and then placed in an oven to be cured again. The temperature is 180 °C and the time is 0.5~3.0 h.
After the sand core is obtained, the core is formed to form a mold, and then the molten metal that meets the requirements is poured into the mold, and the casting is obtained after cooling and solidification. Taking Yijia 3D preparation of cylinder block and cylinder head as an example, the cylinder block adopts HT250 for induction furnace melting gravity casting, the casting temperature is 1 400 ℃ to 1 430 ℃, the casting time is 20 s. The gas from the sand core can be discharged in time. The cylinder head is poured with ZL110, and the resistance furnace is melted and gravity poured, and the pouring temperature is 730 ℃. Finally, the post-processed casting blanks are tested for internal and external quality and key dimensions, so as to obtain castings whose quality fully meets the requirements.
The Applications Of Rapid Sand Casting
Compared with traditional casting technology, the application of additive manufacturing technology to sand casting can obtain sand casting with high dimensional accuracy, complex structure, good casting quality and short production cycle, and reduce the casting cost, and the obtained castings can be obtained in practice. widely used. At present, the application of rapid sand casting technology has gradually matured, and its application range has become wider and wider.
Taking the cast iron cylinder block as an example, the casting process is first designed, then the casting simulation is carried out, and the model is divided into CAD. After the sand mold and sand core are prepared by SLS additive manufacturing, it is poured into a qualified cast iron blank. The process is shown in Figure 8. shown. It only takes 25 days from design to lost foam casting the two-piece cylinder block casting blank, which greatly shortens the manufacturing cycle and reduces the production cost, and the cast cylinder block meets the technical requirements of the product. Although the pouring temperature is high, there is no looseness and veining. When there is a shortage of filling, the probability of breaking the core is less than 5%. Cylinder head sand core assembly, the trial production cycle of cast aluminum cylinder head is shorter, and it only takes 12 days to successfully obtain 2 pieces of cast aluminum cylinder head blanks. Hydraulic valve inner core structure The structure is relatively complex, the traditional process requires multiple sand cores, but the application of SLS additive manufacturing technology, the inner core is sintered as a whole, the accuracy is greatly improved, the core assembly process is also simplified, and the production efficiency is improved.
The combination of additive manufacturing technology and casting process not only improves the utilization rate of materials in the casting process, reduces the processing cost caused by tooling investment, manufacturing and repair, shortens the development cycle, and accelerates production efficiency, but also provides a new technology for additive manufacturing. Opened up a new direction of development. The advantages of the two complement each other, and the development of rapid casting technology has further increased the potential of the foundry industry to produce high-quality castings, making castings prepared by rapid casting widely used, providing a basic guarantee for the development of aerospace and automotive parts, as well as for large-scale complex, The development and production of high-demand components has opened up a new way, the economic benefit has been significantly improved, and it also has far-reaching social benefits.
Key words:additive manufacturing; investment casting; sand casting; application