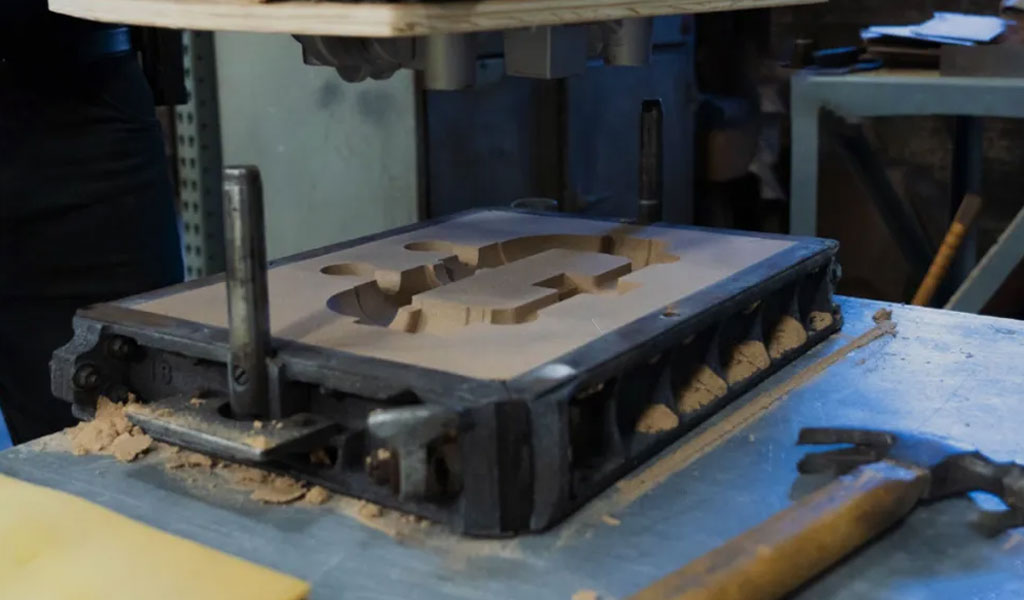
3D Printing sand printing technology has the characteristics of high quality and rapid prototyping, which solves the problems of slow mold opening cycle, high cost and low production efficiency of traditional sand casting, and can meet the requirements of rapid product delivery. This paper analyzes and explains the sand mold design principles, post-processing of digital mold and key factors in the printing process in the process of 3D Printing sand mold digital model design, and proposes solutions to the problems that are easy to occur.
At the same time, the application and prospects of 3D Printing sand mold printing technology Summarize.
Traditional sand casting requires the cooperation of mold manufacturers for production, which cannot meet the needs of rapid research and development of new products. 3DP printing technology uses three-dimensional model modeling, which can realize the four processes of traditional casting mold manufacturing, modeling, core making, and box closing by 3D printing and intelligent molding in one process, and manual and manual work will be replaced by intelligent machines. This technology can print sand molds of any shape, which has great advantages in product development and complex parts production. At the same time, 3DP sand mold printing has certain advantages in printing accuracy, printing speed and sand mold quality.
3D Printing Sand Printing Technology
3DP sand printing is a three-dimensional powder bonding technology. This technology uses droplet jetting technology to slice the sand model, and the computer precisely controls the jetting speed and jetting volume of the print head according to the outline of the sand model. On the mixed sand, after the sand is solidified, the printing table descends one level, and the printing head continues to spray resin, repeating back and forth, and the sand is piled up layer by layer to obtain the desired sand model.
3D Sand Model Design
1.Design Principles
For the casting process, the most important part of the production process is the casting sand. When designing the casting sand mold, it is mainly carried out from the following aspects:
- Parting surface. The selection of the parting surface has a great impact on the casting accuracy, production cost and productivity. Especially after 3DP sand printing, the sand needs to be cleaned. It is necessary to fully consider whether the modeling design can be successfully cleaned, so as to ensure the integrity and accuracy of the sand. . At the same time, the number of parting surfaces should be reduced as much as possible and the sand molding should be simplified.
- Positioning method. In order to ensure the position of the sand core model, improve the dimensional accuracy of the casting, and improve the work efficiency, it is very important to design a reasonable positioning method for the design of the sand mold model.
- Exhaust system. In order to ensure the quality of the castings, the sand mold structure should be ensured in the design process of the sand mold, which is conducive to the sufficient exhaust of the castings, so as to avoid the scrapping of the castings due to poor exhaust.
- Sand mold strength. 3DP sand mold is different from traditional manual molding. When designing sand mold, it is necessary to consider whether the strength of the sand mold can meet the casting production process. Generally speaking, the wall thickness of the casting and its surroundings should be ensured ≥35mm during sand molding; when multiple castings are modeled at the same time, the spacing between adjacent castings should be ≥10mm.
- Hoisting method. For the actual production process, the casting sand mold should be easy to handle, and the appropriate hoisting method can greatly improve the production efficiency. Small castings can be handled with a handle design, and large sand molds can be handled with a hoist.
2.Sand mold post-processing
After the sand mold model is designed, the model needs to be imported into the 3DP printing device for typesetting optimization, so as to meet the printing requirements of the sand mold.
3.Importing model types
After the sand model is designed, it is necessary to export the model to a file in “.stl” format. When converting the sand model, the model is divided into triangles, so the number of triangles directly affects the accuracy of the sand. . If the number of triangular faces is too small, the model will be deformed to a certain extent, but if the number is too large, the rate will be reduced. When exporting the sand mold model, the triangular tolerance and adjacent tolerance of the model should be less than or equal to 0.05, so as to ensure that the accuracy of the model meets the requirements of use. 2.2.
4.Model position adjustment
Since the 3DP sand printing is done layer by layer, it is necessary to ensure that the large plane faces downwards as much as possible when the model is typesetting, so as to reduce the influence of gravity during the model printing process. As shown in Figure 1, when there is an inclined plane or curved surface in the height direction of the sand mold model, the unreasonable placement of the model will cause the printed sand mold to have a step effect or even deformation under the action of gravity, which will affect the accuracy of the sand mold. lead to the scrapping of sand molds. When the design has to use the facet downward, the corresponding auxiliary model should be designed to prevent the deformation of the sand mold due to the influence of gravity. It will lead to an increase in the amount of calculation of the equipment and affect the operating efficiency of the equipment.
5.Model typography
After the model position adjustment is completed, the model needs to be three-dimensional typesetting, and a certain distance must be left between the models during typesetting. The distance between the two models is too close, which will cause the sand molds to stick together, which will lead to the scrapping of the model; if the distance between the models is too far, the space utilization rate of the equipment will be low, which will increase the printing and sand cleaning time and reduce the work efficiency. Generally speaking, the distance between the two sand molds is 10~30mm.
6.Sand printing
- Sample performance test. After the model is typeset, a certain number of test specimens need to be put in for testing and recording its performance. Because the performance of the sand mold will change every time it is printed, it is necessary to test the sample to test its bending resistance, shear resistance and gas generation, to ensure that the quality of the sand mold meets the needs of use, and to record its performance.
- Sand printing. After the performance test of the sample is qualified, the sand mold printing work can be carried out. During the printing process, pay attention to observe whether there is any abnormality, so as to modify and adjust the sand mold model later.
- Sand baking. In order to achieve the best performance of the printed sand mold, put the printed sand mold in an oven and bake it at 100℃ for 2~3 hours before taking it out for use. Too long or too short baking time will directly affect the quality of castings.
The Production Application And Prospect
At present, our factory has successfully applied the 3DP sand printing technology to the sand printing of castings and cold iron. Because of the excellent surface quality of the printed sand, it can greatly reduce the later sand dressing and casting grinding workload, and improve the production efficiency of castings. The cold iron sand mold printed by our factory is shown in Figure 2. Compared with traditional casting production, 3DP sand printing has the advantages of high precision, fast reading and no need for molds, and the size and structure of products can be adjusted at any time to meet the needs of rapid development and production. incomparable advantages.
At the same time, 3DP sand printing is completely unaffected by the shape of the part, and designers can formulate appropriate process plans according to product functional requirements; and completely subvert the traditional casting method, so as to achieve no draft, no process subsidies, and the opening of pouring risers. It can also be carried out in an optimal way without any limitation.
Provide extremely convenient conditions for the research and development of new products, reduce research and production costs, increase the added value of products, and improve product quality. At the same time, with the increasing application of 3DP sand printing in the foundry industry, how to localize 3DP printing equipment and further reduce printing costs will also be issues worthy of attention.