5-axis CNC (Computer Numerical Control) machining is a sophisticated and versatile manufacturing process that allows for the creation of complex parts with high precision. Unlike traditional 3-axis CNC machines, which operate along three linear axes (X, Y, and Z), 5-axis CNC machines incorporate two additional rotational axes. This increased range of motion enables the machining of intricate geometries and the production of parts that would be challenging or impossible to create with other methods.
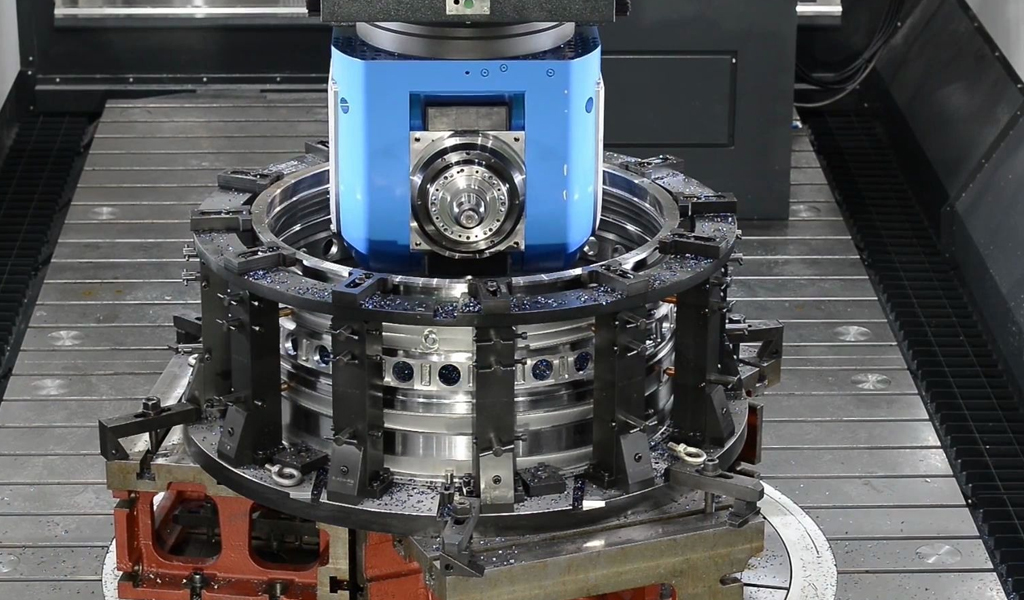
This increased range of motion enables the machining of intricate geometries and the production of parts that would be challenging or impossible to create with other methods.The adoption of 5-axis CNC machining has revolutionized various industries, including aerospace, automotive, and medical devices.
Its ability to produce high-precision components with complex shapes and tight tolerances makes it an essential tool for manufacturers looking to stay competitive in today’s market. However, the advanced capabilities of 5-axis CNC machining come with a range of costs that must be carefully considered.
This article provides an in-depth analysis of the costs associated with 5-axis CNC machining, exploring the various factors that influence these costs, comparing them to other types of CNC machining, and examining real-world case studies. By understanding the financial implications of 5-axis CNC machining, manufacturers can make informed decisions and optimize their production processes.
Types of Costs Involved
The costs associated with 5-axis CNC machining can be broadly categorized into initial setup costs, operational costs, and material costs. Each of these categories encompasses a variety of specific expenses that manufacturers must account for.
Initial Setup Costs
The initial setup costs for 5-axis CNC machining are significant and include the purchase price of the machines, installation, and calibration. The price of a 5-axis CNC machine varies depending on its size, capabilities, brand, and quality. High-end machines with advanced features and larger work envelopes can cost several hundred thousand dollars. Additionally, the installation process requires specialized technicians to ensure the machine is correctly calibrated and ready for production.
Beyond the machine itself, manufacturers must also invest in the necessary tooling, software, and infrastructure to support 5-axis CNC machining. This includes CAD/CAM software for designing and programming parts, as well as tooling such as end mills, drills, and cutting inserts. The costs of these additional components can add up quickly, making the initial setup phase a substantial investment.
Operational Costs
Once a 5-axis CNC machine is up and running, operational costs become the primary financial consideration. These costs include maintenance and repairs, energy consumption, and labor.
Regular maintenance is crucial for keeping a 5-axis CNC machine in optimal working condition. This includes routine inspections, lubrication, and the replacement of worn parts. While preventive maintenance can help avoid costly breakdowns, unexpected repairs are still a possibility and can result in significant downtime and expenses.
Energy consumption is another important operational cost. 5-axis CNC machines are typically more energy-intensive than their 3-axis counterparts due to their increased complexity and capabilities. Monitoring and optimizing energy usage can help reduce overall operational costs.
Labor costs are also a key factor. Operating a 5-axis CNC machine requires skilled machinists and programmers who are familiar with the technology and capable of producing high-quality parts. The cost of labor can vary depending on the region and the level of expertise required.
Material Costs
The materials used in 5-axis CNC machining play a significant role in determining the overall cost of production. Different materials have varying costs based on their properties and availability. Common materials used in 5-axis CNC machining include metals such as aluminum, steel, and titanium, as well as plastics and composites.
The choice of material depends on the specific requirements of the part being produced. For example, aerospace components often require lightweight and high-strength materials like titanium, which can be more expensive than other metals. Understanding the cost implications of different materials is essential for effective cost management in 5-axis CNC machining.
Factors Affecting Costs
Several factors influence the costs associated with 5-axis CNC machining. These factors include machine specifications, production volume, and the precision and complexity of the parts being produced.
Machine Specifications
The specifications of a 5-axis CNC machine, such as its size, capabilities, brand, and quality, have a direct impact on its cost.
Larger machines with greater work envelopes and higher precision capabilities are generally more expensive.
Additionally, machines from reputable brands with a history of reliability and performance may come with a higher price tag but offer long-term benefits in terms of durability and support.
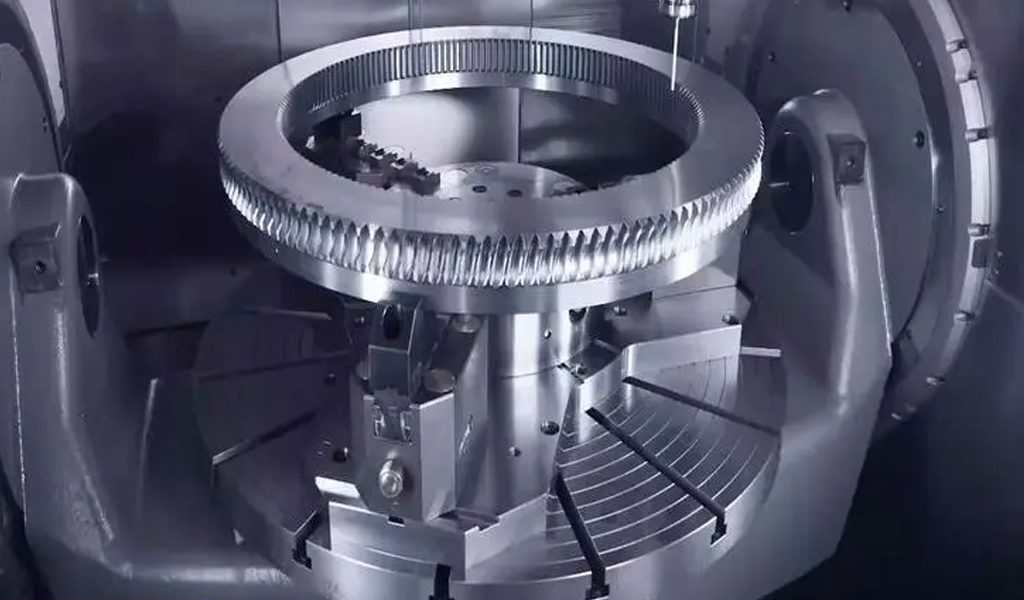
Production Volume
The volume of parts being produced also affects the cost of 5-axis CNC machining. High-volume production can benefit from economies of scale, where the cost per part decreases as the production quantity increases. On the other hand, low-volume or custom production runs may incur higher costs due to setup and programming time.
Precision and Complexity
The precision and complexity of the parts being produced are significant cost drivers in 5-axis CNC machining. Parts with tight tolerances and intricate geometries require more time and effort to program and machine. The need for specialized tooling and fixtures can further increase costs. Manufacturers must balance the desired precision and complexity with the associated costs to achieve optimal results.
Cost Comparison: 5-Axis vs. Other CNC Machines
Comparing the costs of 5-axis CNC machining with those of other CNC machines, such as 3-axis and 4-axis machines, provides valuable insights into the cost-benefit analysis of each option. While 5-axis machines offer superior capabilities and flexibility, they come with higher initial and operational costs.
5-Axis CNC Machining | 3-Axis CNC Machining | Traditional Machining | |
Setup time | Reduced setup time due to simultaneous machining from multiple angles. | Longer setup time is required for each machining operation. | Multiple setups are required for complex parts. |
Machining time | Shorter machining time due to faster cutting speeds and fewer operations. | Longer machining time due to slower cutting speeds and multiple operations. | Long machining times due to manual operations. |
Accuracy | Higher accuracy and precision due to multi-axis control. | Lower accuracy and precision, especially for complex geometries. | Lower accuracy and precision compared to CNC machining. |
Labor costs | Lower labor costs due to automation and fewer manual operations. | Higher labor costs due to manual setup and operation. | High labor costs due to extensive manual work. |
Scrap rate | Reduced scrap rate due to higher accuracy and fewer errors. | Higher scrap rate due to lower accuracy and multiple setups. | High scrap rate due to manual operations. |
Lead time | Shorter lead time due to faster production times. | Longer lead time due to longer machining and setup times. | Long lead times due to manual processes. |
Flexibility | Higher flexibility to produce complex parts with intricate features. | Lower flexibility for complex parts, limited to simpler geometries. | Limited flexibility for complex parts, requires custom tooling. |
Best suited for | Complex, high-precision parts, low-volume production of complex parts, and applications where reduced lead time is crucial. | Simple parts with basic geometries, high-volume production of simple parts. | Simple parts with basic geometries, low-volume production, or when cost is the primary concern. |
Comparison with 3-Axis and 4-Axis CNC Machines
3-axis CNC machines operate along three linear axes and are suitable for a wide range of applications. They are generally less expensive than 5-axis machines and require simpler programming. However, they are limited in their ability to produce complex parts with intricate geometries.
4-axis CNC machines add an additional rotational axis, allowing for greater flexibility and the ability to machine parts from multiple angles. While they offer improved capabilities over 3-axis machines, they still fall short of the versatility and precision of 5-axis machines.
Cost-Benefit Analysis
When considering whether to invest in a 5-axis CNC machine, manufacturers must conduct a cost-benefit analysis. This involves evaluating the specific needs of their production processes and weighing the advantages of 5-axis machining against the associated costs. In cases where high precision, complex geometries, and reduced setup times are critical, the benefits of 5-axis CNC machining may justify the higher investment.
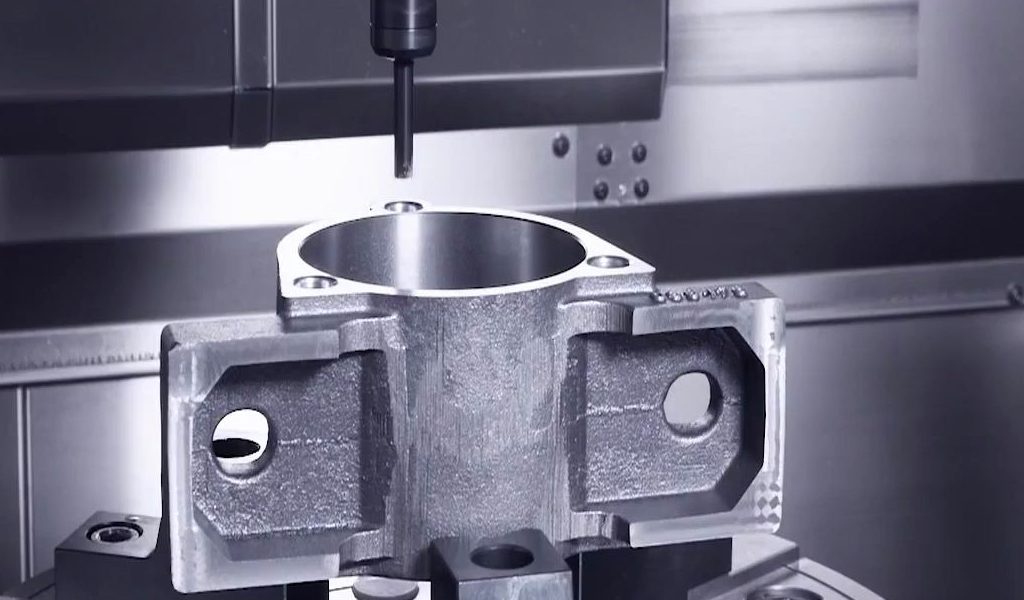
When to Choose 5-Axis Machining
The decision to choose 5-axis CNC machining over other options depends on several factors, including the complexity of the parts being produced, the required precision, and the production volume.
Industries such as aerospace and medical devices, where complex geometries and tight tolerances are common, often find 5-axis CNC machining to be the best choice. Conversely, simpler applications with less stringent requirements may benefit from the cost savings of 3-axis or 4-axis machines.
5 Axis CNC Machining Case Studies
Examining real-world case studies provides practical insights into the costs of 5-axis CNC machining across different industries. These case studies highlight the financial considerations and benefits of adopting this advanced manufacturing technology.
Aerospace Industry
The aerospace industry is one of the primary users of 5-axis CNC machining due to its need for high-precision components with complex geometries. Case studies from aerospace manufacturers can shed light on the cost implications of producing turbine blades, structural components, and other critical parts using 5-axis CNC machining. Factors such as material selection, production volume, and quality requirements play a significant role in determining the overall costs.
Automotive Industry
In the automotive industry, 5-axis CNC machining is used to produce various components, including engine parts, transmission components, and prototype models. Case studies from automotive manufacturers can provide insights into the cost dynamics of using 5-axis CNC machines for both high-volume production and custom prototyping. The impact of material costs, labor, and energy consumption on the overall cost structure can be explored.
Medical Devices Industry
The medical devices industry relies on 5-axis CNC machining to produce intricate and precise components for surgical instruments, implants, and diagnostic equipment. Case studies from medical device manufacturers can illustrate the costs associated with meeting stringent regulatory requirements and ensuring the highest levels of quality and precision. The role of advanced materials and the need for customization can also be examined.
Future Trends and Cost Projections
Technological advancements, automation, and the integration of artificial intelligence (AI) are expected to shape the future of 5-axis CNC machining. Understanding these trends and their potential impact on costs is crucial for manufacturers planning for the future.
Technological Advancements
Advances in machine design, software, and tooling are likely to improve the efficiency and capabilities of 5 axis CNC machining. Innovations such as additive manufacturing and hybrid machining, which combine subtractive and additive processes, may also influence cost structures. Staying abreast of these developments can help manufacturers optimize their production processes and manage costs effectively.
Impact of Automation and AI
Automation and AI are poised to play a significant role in reducing the costs associated with 5-axis CNC machining. Automated systems can streamline production, reduce labor costs, and minimize errors. AI-powered software can enhance programming efficiency and optimize machining strategies, further driving down costs. The adoption of these technologies requires an initial investment but can yield long-term cost savings.
Predicted Cost Trends
Predicting future cost trends involves considering factors such as market demand, technological advancements, and economic conditions. While the initial costs of 5-axis CNC machines may remain high, ongoing improvements in efficiency and productivity could lead to overall cost reductions. Manufacturers must stay informed about industry trends and continuously evaluate their cost management strategies to remain competitive.
Conclusion
The costs of 5-axis CNC machining encompass a wide range of factors, including initial setup costs, operational expenses, and material costs. Understanding these costs and the factors that influence them is essential for manufacturers looking to leverage the benefits of this advanced manufacturing technology. By carefully considering the specific needs of their production processes, conducting cost-benefit analyses, and staying informed about industry trends, manufacturers can optimize their use of 5-axis CNC machining and achieve a balance between cost and performance.
This comprehensive analysis of the costs associated with 5-axis CNC machining provides valuable insights for manufacturers across various industries. As technology continues to evolve, staying informed about the latest developments and cost management strategies will be key to maintaining a competitive edge in the market.