What Is Die Casting
Die casting is a special casting method with little cutting and no cutting, which has developed rapidly in modern metal processing technology. It has the characteristics of high production efficiency, excellent economic indicators, high dimensional accuracy of castings and good interchangeability. The chemical industry has been widely used and developed rapidly. Die casting is the predominant forming method for light metals such as aluminium, magnesium and zinc, and is suitable for the production of large and complex thin-walled shell parts. Die-casting parts have become an important part of products in the fields of automobiles, sports equipment, electronics and aerospace, among which the automotive industry is the main field of die-casting technology applications, accounting for more than 70%.
With the rapid development of automobiles, motorcycles, internal combustion engines, electronic communications, instrumentation, household appliances, hardware and other industries, the functions and application fields of die-casting parts continue to expand, thus promoting the continuous development of die-casting technology and improving the quality of die-casting parts.
China Top Die Casting Parts OEM Supplier & Manufacturer
If you are looking for dependable aluminum die casting supplier with High pressure die casting service who offers you competitive price, good service and quality for aluminium (aluminum), zinc, or magnesium die casting, then we are surely a partner you are looking for to fulfill all your die casting needs.
For over 30 years, the BE-CU foundry has been providing custom die casting services for a variety of industries and project types. Our in-house mold-making, heat treatment, and precision casting services bring experience and quality to every project.Capable of both mass production and prototyping, BE-CU foundry has provided many high-precision prototypes and end-use parts to our clients. CNC machining is available to combine with die casting and produce parts with finer surface details (surface finishing available, too). As mentioned before, we work shoulder-to-shoulder with you up front, in the design and development phase, to make sure the most innovative and creative solutions can be implemented that match your needs and expectations. Our expert team will review all of part design issue, mold manufacturing issue, or any potential problem and bring all of issue together and report to you, to make sure our die casting performance is fulfilling your expectations and we could have the best status of die casting products at the first mold trial.
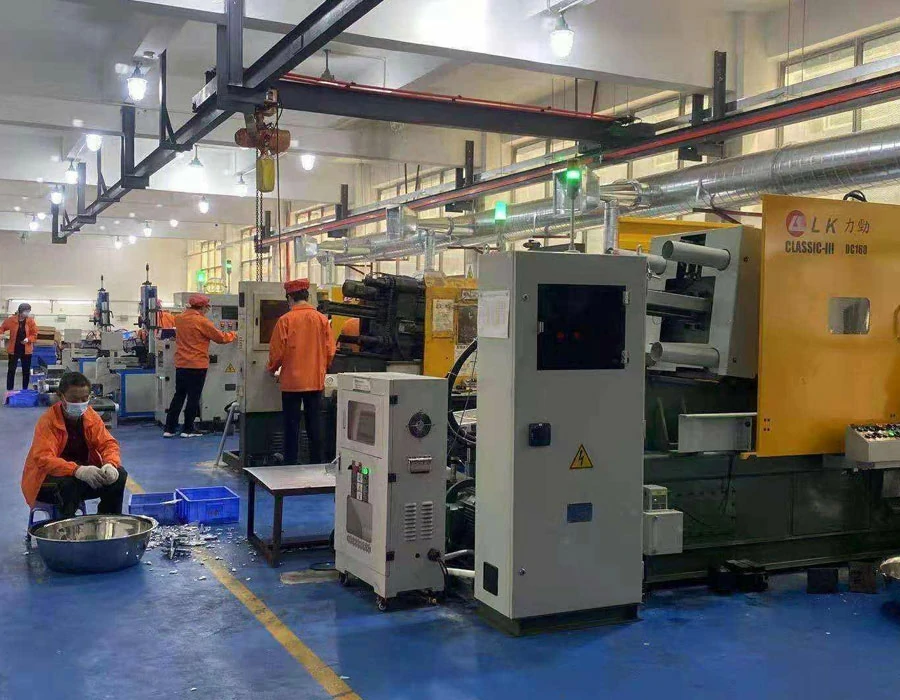
After first die casting mold samples, we will analysis your products issue base on your requirement, measure all of dimensions according to 2D drawing and improve the die castings issue or part design issue to meet your requirement, during this time we will trial the die casting mold and send you the new casting samples from time to time until you 100% satisfied.
During the time from mold manufacturing until you approval the final die casting parts, we will stay with you as a team player, to work with you on every step, to make sure that you will be happy with our die casting company and our die castings.Our improved algorithm decreases die casting quotation times by up to 90%. Most quotes are delivered within 24 hrs. and usually in much less time, depending on project details.Your customer support partner will contact you directly about your die casting quote to ensure you’ve received and understand all aspects of your quotation and to answer any questions you may have about your options.
Metal Die Casting Equipment Gallery
BE-CU metal die casting company can produce components in Aluminium die casting, Magnesium die casting & Zinc die casting up to 300 tons in Aluminium( Magnesium ) & 100 tons in Zinc per month depending upon the size of the component. We have die casting machines ranging from 30 tons to 3000 tons,Facilities for die casting of rotors for FHP Motors, machining, anodizing & Powder Coating of rotors, riveting of stacks, CNC machining of end-shields also exist.
200 T Hot Chamber Die Casting Machine 3000T LIBI DIE CASTING MACHINE lijing 280T die casting machine SANJI Overhaul 550t Die Casting Machine YIZUMI DM 400t Die Casting Machine YIZUMI DM 1650t Die Casting Machine
High Pressure Die Casting Material
At present, the commonly used die-casting alloys in the industry are aluminum alloys and magnesium alloys. Among them, aluminum alloys for die casting mainly include Al-Si (Al-Si-Cu, Al-Si-Mg) and Al-Mg series, among which Al-Si alloys are the most widely used. However, the current industrial die-casting aluminum alloys are mainly developed for the characteristics of the die-casting process, and less consideration is given to the mechanical properties, post-heat treatment and welding process requirements. Therefore, although the strength of the current die-casting parts can reach 300 MPa, the plasticity is poor, the elongation after fracture is low, and the subsequent heat treatment and welding process requirements cannot be met, which greatly limits the application scope of die-casting aluminum alloy parts. Magnesium alloys for die casting mainly include AZ series (Mg-Al-Zn), AM series (Mg-Al-Mn) and AE series (Mg-Al-RE) and other series, such as AZ91D, AM60B and AE42 and other die-casting magnesium alloys It has been widely used in automobile, electronics and other fields. Similar to die-casting aluminum alloys, the development of die-casting magnesium alloys is also based on the characteristics of the die-casting process. However, due to the relatively low absolute mechanical properties, poor corrosion resistance and high temperature performance of commonly used die-casting magnesium alloys, it is difficult to apply die-casting magnesium alloys in a wide range [
The Types of Metal Die Casting
Molds are usually machined from stronger alloys, a process somewhat similar to injection molding. Most die castings are free of iron, such as zinc, copper, aluminum, magnesium, lead, tin, and lead-tin alloys and their alloys. Depending on the type of die casting, a cold chamber die casting machine or a hot chamber die casting machine is required.
Whether hot chamber die casting or Cold Chamber Die Casting, Die castings are characterized by a very good surface finish (by casting standards) and dimensional consistency.
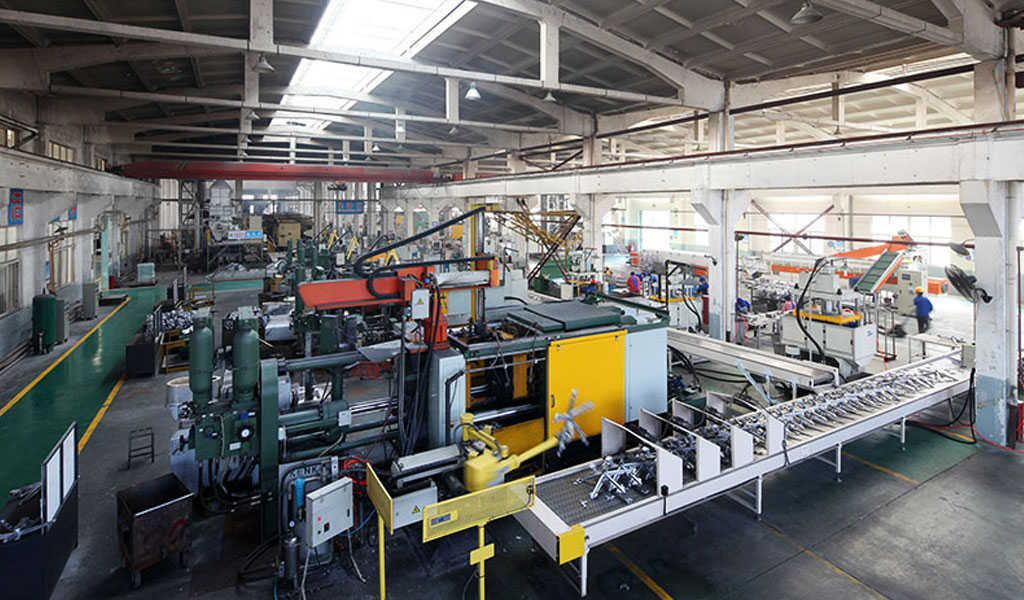
Molds are usually machined from stronger alloys, a process somewhat similar to injection molding. Most die castings are free of iron, such as zinc, copper, aluminum, magnesium, lead, tin, and lead-tin alloys and their alloys. Depending on the type of die casting, a cold chamber die casting machine or a hot chamber die casting machine is required.
Hot chamber die casting refers to a die-casting method in which the injection chamber and the injection punch are immersed in molten metal. The injection chamber is connected to the gate of the die-casting mold through a gooseneck. It is suitable for die-casting zinc, lead and other low melting point non-ferrous alloy parts, and can be widely used in automobile, motorcycle accessories, instrumentation, daily hardware, household appliances and other industrial sectors.
Cold chamber die casting refers to a vertical chamber cold chamber methods in which the injection chamber and the injection punch are not immersed in the molten metal, but a quantitative amount of molten metal is poured into the injection chamber and then injected. The injection method is placed vertically;The procedure of one working cycle of horizontal cold chamber die casting is simpler than that of vertical cold chamber die casting.
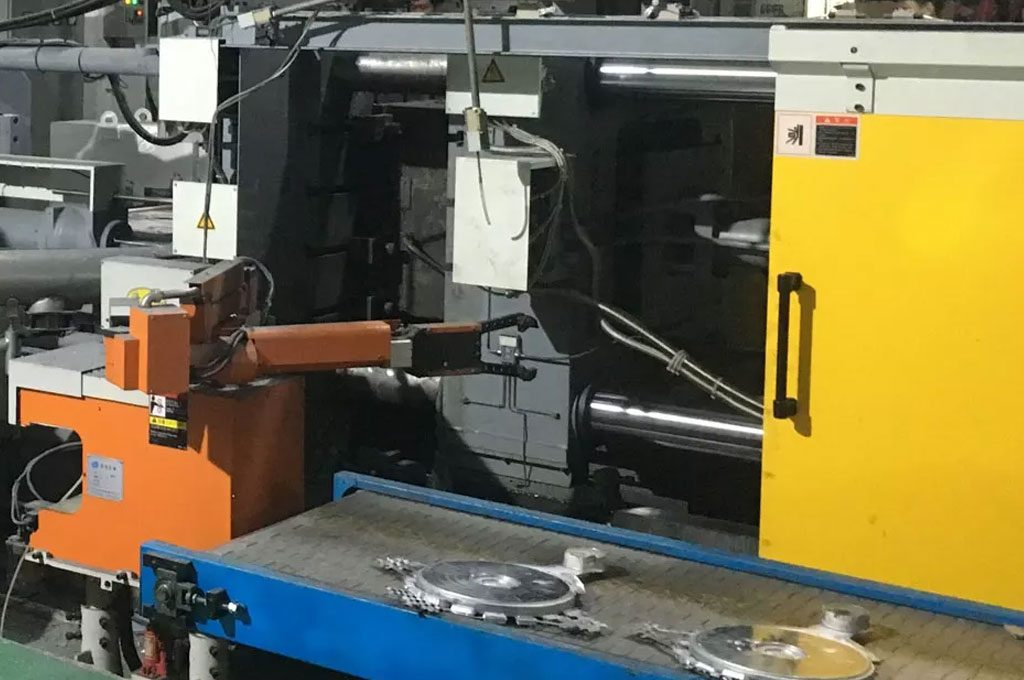
Advantages of Die Casting
The essence of die casting is a forming process in which liquid or semi-solid metal is filled into the die-casting mold cavity at a very high speed under the action of high pressure, and is formed and cooled and solidified under the action of pressure to obtain a casting. It can be seen that high-pressure and high-speed filling of the die-casting mold cavity are the two major characteristics of the die-casting process—its commonly used injection pressure ranges from thousands to tens of thousands of KPa, and even reaches 2×105KPa at the highest; at the same time, its filling The speed is about 10~50m/s, sometimes even more than 100m/s, so the filling time is very short, generally in the range of 0.01~0.2s. Compared with other liquid forming methods, the die casting process has the following three advantages:
Disadvantages of Die Casting
Things often have two sides. Although the die-casting process has so many advantages, it also inevitably has many problems to be solved. These problems, the limitations of the die casting process, can be summarized in the following four aspects:
- Die castings often have pores: this is because during die casting, the molten metal fills the cavity at a high speed, and the gas in the cavity will inevitably be involved in the molten metal before it can be discharged, resulting in pore defects and reducing die casting. Piece quality. In addition, the gas expansion in the pores at high temperature will cause the surface of the die casting to bubble, which will seriously affect the appearance of the die casting and reduce its overall mechanical properties. Therefore, die castings generally cannot be heat treated and welded, nor should they work at high temperatures.
- Not suitable for small batch production: the main reason is that the cost of the die casting machine and the die casting mold is relatively expensive, and the production efficiency of the die casting machine is very high, so although the die casting process can bring a lower unit cost to mass production, it is not suitable for small batches. It is not economical to produce.
- Die-casting size is limited: The size of die-casting mold is limited by the clamping force of the die-casting machine and its mold size, so the die-casting process is only suitable for the production of small and medium-sized castings, but not for large-scale castings. Similarly, for die-casting parts with complex concave, the die-casting production is also difficult due to the limitations of die-casting molds and principles.
- The types of die-casting alloys are limited: the die-casting molds are limited by the operating temperature, and the melting point of some alloys (such as ferrous metals) is too high, resulting in too low lifespan of the matching die-casting molds and high costs, making it difficult to apply in actual production. At present, the alloys used for die casting production are mainly non-ferrous metals such as zinc alloy, aluminum alloy, magnesium alloy and copper alloy.
Looking at the above four limitations, ② and ④ are limited by economic costs, and ③ limited by existing equipment conditions, so far, the technological progress has been slow. Only ① is produced in the die-casting process, and the generation of pores can be reduced or even completely avoided through certain technical improvements.
In fact, it is the existence of the porosity problem that constantly promotes the improvement of the die-casting process to meet people’s increasing requirements for the quality of die-casting parts, and at the same time expands the application range of the die-casting process.
High Pressure Die Casting Process
In the die casting process, the molten metal fills the cavity at a high speed (generally up to 10-100 m/s) under the action of a punch, and crystallizes and solidifies under high pressure (common pressure is 15-100 MPa) to form a casting. High pressure and high speed are the main characteristics of die casting. According to the changes of punch speed and pressure in different stages, taking cold chamber die casting as an example, die casting is generally divided into soup feeding, injection (two stages of slow injection and fast injection), pressure-holding solidification, mold opening and sampling, etc. process. In the process of feeding the soup, the high-temperature molten metal contacts with the air and is oxidized, and the generated oxides will enter the cavity with the injection process, resulting in oxidation inclusions.
In the process of low-speed injection, when the low-speed speed is too high, the molten metal at the front end of the punch is easy to flip forward and get involved in the air, forming air holes. During the high-speed filling process, the molten metal enters the cavity in the form of turbulent flow. The air in it is too late to be discharged and is involved in the molten metal, which eventually leads to the appearance of pores in the casting.
Since most of the die castings are complex thin-walled parts, in order to meet the filling integrity, the inner gate is usually designed to be very small. The effect of high-speed filling is achieved, but during the solidification process, the smaller inner gate is easier to solidify earlier than the casting, thus blocking the liquid phase feeding channel between the pressure chamber and the cavity, making the subsequent high-pressure feeding;The action time of the stage is short, and the effect is not ideal.
Die making and assembly
Injection
Cooling
Ejection
Trimming
On the other hand, pre-crystallized structures (ESCs), as a typical structure in die castings, are the coarse dendritic grains formed by the pre-crystallized particles formed by the solidification of molten metal in the pressure chamber as the melt fills the cavity. In the area where ESCs gather, due to the unsatisfactory feeding effect, shrinkage defects are very likely to occur. Therefore, pores and shrinkage cavities constitute the main defects of die-casting products – hole defects. Hole defects cause the mechanical properties of die castings to decline and become unstable, reduce the air tightness of die castings, and limit the welding and heat treatment applications of die castings. Hole defects close to the surface can also cause die castings to be scrapped after machining, greatly limiting the range of die casting applications.Although die castings are now widely used in the fields of automobiles, communication electronics and aerospace, due to their low absolute strength, poor high temperature mechanical properties, and difficulty in subsequent heat treatment, welding and other processes. Therefore, die castings are mainly used to produce shell parts that do not require high mechanical properties at room temperature, while other forming processes with relatively low production efficiency and relatively poor economic indicators are still used for structural parts with high requirements on mechanical properties. or other materials with lower specific strength. With the rapid development of my country’s automobile industry, on the one hand, the demand for automobile die castings is increasing; high demands. Relevant literature points out that every 10% reduction in vehicle body weight can reduce energy consumption by 5% to 7%. Therefore, the development of high-performance, high-density die-casting forming technology to expand the application range of die-casting parts is the main development trend of the die-casting industry in the future.