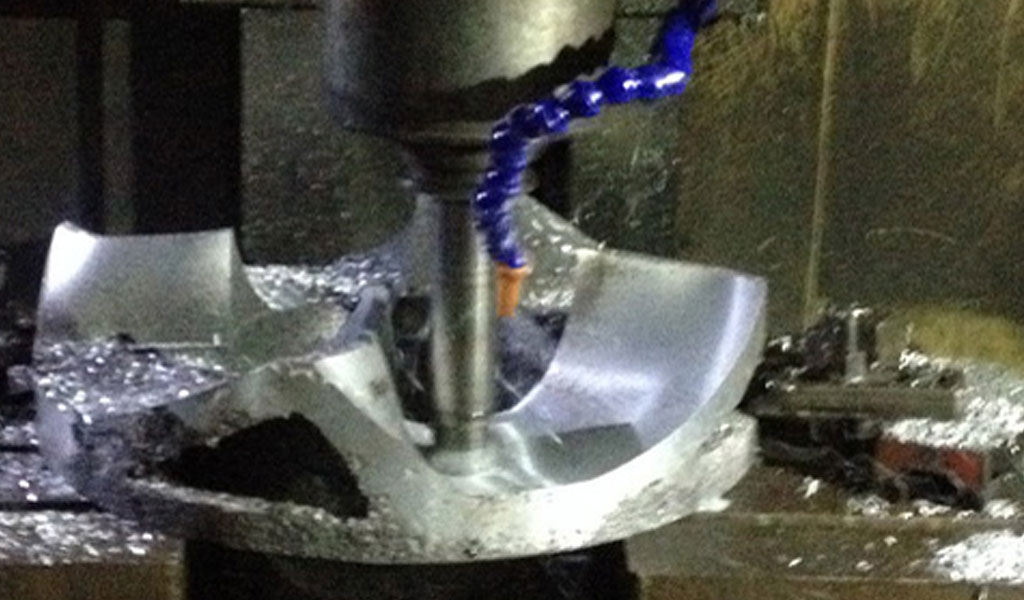
Blade moulds are usually referred to as female moulds, which are used to produce paste-laminated blades. It needs to be made before making the negative mold
A male mold for making a female mold. Blade main mold (ie upper and lower profile mold, also commonly known as blade shell mold) male mold
The manufacturing method and mold structure of the negative mold are very complicated, and it is one of the key technologies of blade manufacturing.
Positive Mold Making
The manufacturing method and mold structure of the front and rear beams of the blade, the upper and lower spar male molds and the mold structure are relatively simple, and will not be repeated here, and only the production of the blade shell male mold will be introduced below. Usually, there are two production methods for the male mold. One is to buy the finished blade for grinding and trimming to make it smooth and meet the requirements of the leaf surface curve; Template control method production. The blade shell male mold is the mold tire that constitutes the upper and lower profile surfaces of the blade. The structure needs to have a certain strength and rigidity, and the surface has a certain hardness, but the machining accuracy of the geometric surface is mainly high. The foreign advanced male mold manufacturing process is to process the profile by large-scale CNC machining equipment.
Because the blade is very long, it needs to be processed in sections and then assembled into one. First, rough machining on the easy-to-process rigid foam body, process it to a certain size, spray a hard shell with a certain thickness on the surface of the foam body, then process the hard shell to the size, and then polish it to reach the size required for reproducing the negative mold Precision and surface finish. This kind of processing equipment is still rare in China, and it is difficult to adopt this method. Another method of making male molds is to use a large number of CNC-machined precise cutting templates to control the manual repair of the profile, which can also meet the accuracy requirements.
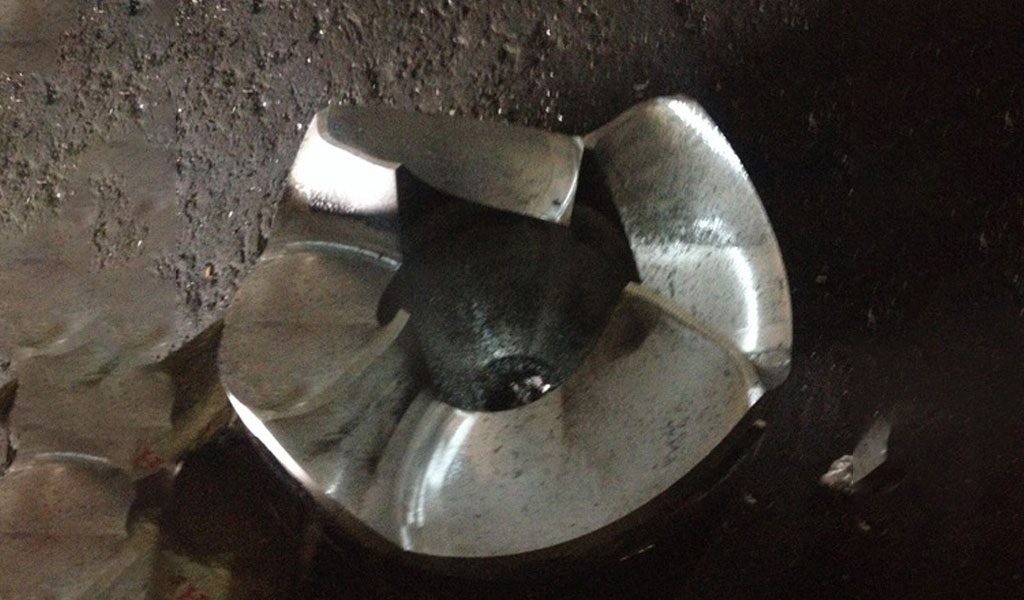
Blade mold (female mold) manufacturing
The main mold refers to the mold (female mold) that produces the blade shell. The overall form of the leaf shell mold is: “glass fiber reinforced plastic shell + steel structure frame”, and the upper and lower profiles have a split structure. The “glass reinforced plastic shell” forms the geometric surface required for the blade, with certain strength and rigidity, and the surface adopts a mold gel coat layer. A heating system is placed in the shell to ensure the temperature required for blade forming. The “steel frame” provides the main strength and stiffness for the mold and provides the mounting base for the mold’s positioning system and clamping/ejection system. The method of closing and opening the mold adopts the method that the lower mold is fixed and fastened to the ground, and the upper mold is moved by the crane to connect or open the lower mold. , or separate from the lower die and blade. A jacking system should be used for initial separation before lifting. In general, the production process of the main mold is as follows: paste the upper and lower mold shells (on the mold tire, that is, the male mold), weld the upper and lower mold steel frames, paste the upper and lower mold steel frames with the upper and lower mold shells, and spray polyurethane. Insulation materials, upper and lower molds are removed, lower molds are leveled, upper and lower mold positioning devices are installed, turning mechanisms are installed, and upper and lower mold surfaces are polished and inspected. The wiring and fixing of the heating tape should also be considered when pasting the shell.
Front and rear spar, upper and lower wing spar mould making
The production of the front and rear beams and the upper and lower spar molds is simpler than the production of the main mold. It is only necessary to paste the mold on the male mold (mold tire), weld the supporting steel frame, and paste the steel frame and the mold into one. Leveling, grinding and inspection of the model surface, do not require lifting mechanism, positioning device, turning mechanism and heating system.