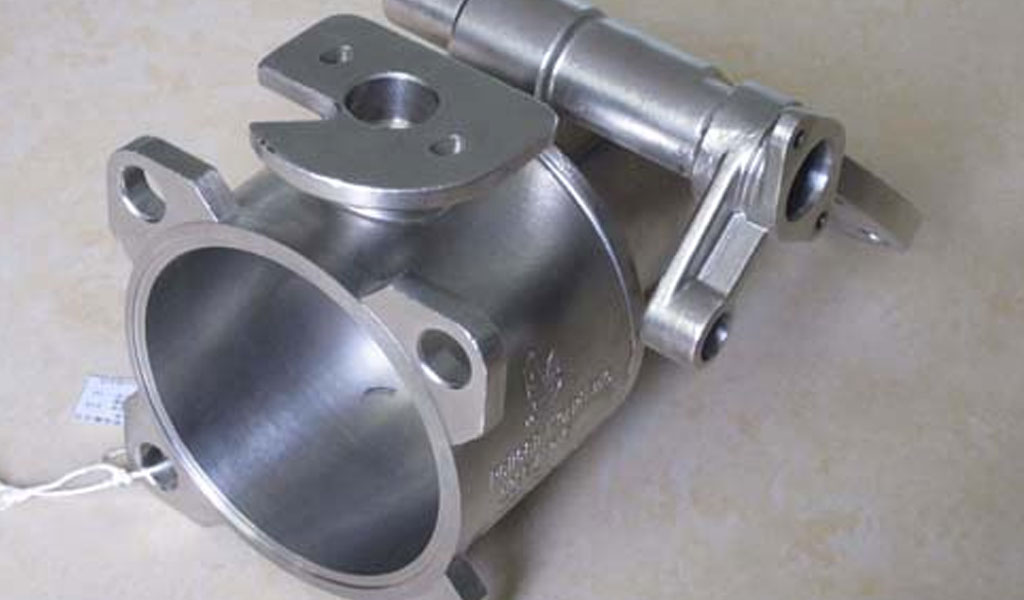
The production of the silver plate is completely dependent on the manual skills of the plate maker. Through sawing, filing, welding and cutting, the original plate with sharp edges and corners, clear lines and smooth surface is produced with 925 silver. It is a highly demanding process in the jewelry making process. It requires the surface, hollow parts and back of the silver plate to be smooth and free of traces. It requires that the structure of each part of the silver plate is reasonable, and the position and size of the gemstones are accurate and traceless. Parts are pre-processed. For the silver plate with complex structure, due to the large number of parts, it is very difficult to use the general welding method, and the production needs to be completed by the method of swinging the embryo. Once the silver plate is ready, the lost wax casting process can be entered.
Casting mold products generally do not apply pressure, do not require high strength of equipment and molds, have small restrictions on product size, and have low internal stress in products. Therefore, the production investment is less, and large-scale parts with excellent performance can be obtained, but the production cycle is long, and mechanical processing must be carried out after molding. On the basis of traditional casting, methods such as pouring, insert casting, pressure casting, spin casting and centrifugal casting are derived.
- Perfusion. The difference between this method and casting is that the product is released from the mold after casting, while the mold is an integral part of the product itself during pouring.
- Embedded casting. Various non-plastic parts are placed in the mold cavity and solidified with the injected liquid material to encapsulate them.
- Pressure casting. The necessary pressure is applied to the material during casting, which is conducive to injecting viscous materials into the mold and shortens the filling time. It is mainly used for epoxy resin casting.
- Spin casting. After the material is injected into the mold, the mold rotates around a single axis or multiple axes at a low speed, and the material is distributed on the inner wall of the mold cavity by gravity, and is shaped by heating and curing. For the manufacture of spherical, tubular and other hollow products.
- Centrifugal casting. A quantitative liquid material is injected into a mold that rotates at a high speed around a single axis and can be heated, and the material is distributed on the inner wall of the mold cavity by centrifugal force, and is solidified into a tubular or hollow cylindrical product by physical or chemical action (see Figure [centrifugation]. casting]). Monolithic cast nylon parts can also be formed by centrifugal casting.
The process flow of lost wax casting is: pressing plastic mold – opening plastic mold – wax injection (mold) – trimming wax mold (welding wax mold) – planting wax tree (weighing) – filling gypsum cylinder – gypsum vacuuming – gypsum natural solidification – Baking plaster – melting gold, casting – frying and washing plaster – rinsing, pickling, cleaning – cutting blanks – moulding. Each process is described below.
Material: The glue used for pressing the glue mold is a raw rubber sheet with viscose on both sides. The preservation of raw rubber sheets must pay attention to controlling the storage temperature. Generally, it is stored for one year under 20 °C, and the storage time at 0-5 °C can reach 2-3 years.
Equipment: (vulcanization) compression molding machine. The main components are composed of two inner heating plates with resistance wires and temperature sensing devices, thermostats, timers, etc. Also comes with a lift bar. For pressing and taking out. There are die frames that are used together, which can be divided into single-plate, double-plate, four-plate and other models according to the number of openings. The material for making the die frame is usually aluminum alloy, and the size is generally 48mm╳73mm, thickened size There are 64mm╳95mm.
Precautions for pressing plastic mold:
- The stamping frame and the raw film should be clean, and do not touch the surface of the raw film directly with hands.
- To ensure that there is no adhesion between the original plate and the rubber, the silver plate should be used first, and the copper plate should be plated with silver first.
- Determine the appropriate vulcanization temperature and time, which basically conform to a functional relationship, which is related to the thickness, length and width of the rubber mold and the complexity of the original. Usually, the temperature of the compression mold is set at about 150 degrees. If the thickness of the rubber mold is 3 layers (about 10mm), the general curing time is 20-25 minutes. If it is 4 layers (about 13mm), the curing time can be 30-35 minutes. . And so on. At the same time, the vulcanization temperature is also related to the complexity of the original. If the original is complex and small, the vulcanization temperature should be lowered and the vulcanization time should be extended.
- Make sure that there is no gap between the original plate and the raw film when pressing. The fine pores are filled with small colloidal particles.
- line preheating. When the vulcanization time is up, take out the plastic mold quickly, so that it can be cooled naturally enough that it is not hot, and you can use a sharp scalpel to open the plastic mold while it is still hot.