What Is Casting Molds
The metal casting molds refers to the mold used to form the casting in the casting forming process. Casting molds are supporting the casting process, mainly including gravity casting molds, high-pressure casting molds (die-casting molds), low-pressure casting molds, and extrusion casting molds. Casting mold is one of the most important technological equipment in casting production, which has a great influence on the quality of castings. The improvement of casting mold technology will be of great significance to improve the quality of castings, develop new types of castings, and improve the level of near-net processing. The advancement of casting mold technology will provide more precise, complex and high-quality castings for national pillar industries such as automobiles, electric power, ships, rail transit, aerospace, etc., and promote the improvement of the overall level of my country’s manufacturing industry.
Casting mold refers to that in order to obtain the structural shape of the part, other easy-to-form materials are used to make the structural shape of the part in advance, and then the mold is placed in the sand mold, so a cavity with the same size as the part structure is formed in the sand mold. Then pour a fluid liquid into the cavity, and after the liquid cools and solidifies, a part with exactly the same shape and structure as the mold can be formed. The casting mold is an important part of the casting process.
China Top Metal Casting Molds manufacturers
Need casting mold making supplies for mass production parts? China Be-Cu foundry is known as the best mold maker in China. With mold making facilities in house and resources from our partners, we are able to provide sand cast molds for both aluminum,iron,steel and more, investment cast molds for all type of precision stainless steel,brass or aluminum parts, and pressure die casting molds for aluminum, magnesium and zinc. We offer low-cost local production molds and high-quality exported molds for all your project needs.
Whatever you need prototype molds for the short-run production, or mass production molds for millions times, Be-Cu foundry can handle them for you smoothly.
Offers superior accuracy and smooth surface finish, making it an excellent solution for the production of intricate castings
How To Make A Cast Mold
The Process Of Investment Casting Mold Making
BE-CU investment casting mold factory uses wax to make a 1:1 desired object shape, and then wraps it with other substances (such as gypsum, molding sand, etc.), and then melts the wax by heating to form a “model” Cavity”, use this cavity to pour the desired shape object, this “cavity” is called “lost wax mold”
- First, I want to make a metal mold according to the requirements of the parts organization
- Second, use the casting machine to pass the medium temperature wax into the mold cavity (if the part is large, you can use the low temperature wax and pour it by hand)
- Third, wrap the wax mold with high temperature resistant material (usually quartz sand)
- Fourth, pour the liquid metal onto the wax mold wrapped by the high temperature resistant material. Since the melting point of the wax is low, the wax will flow out along the preset channel.
- Fifth, when the metal solidifies, remove the wrapped high temperature resistant material to obtain the required casting.
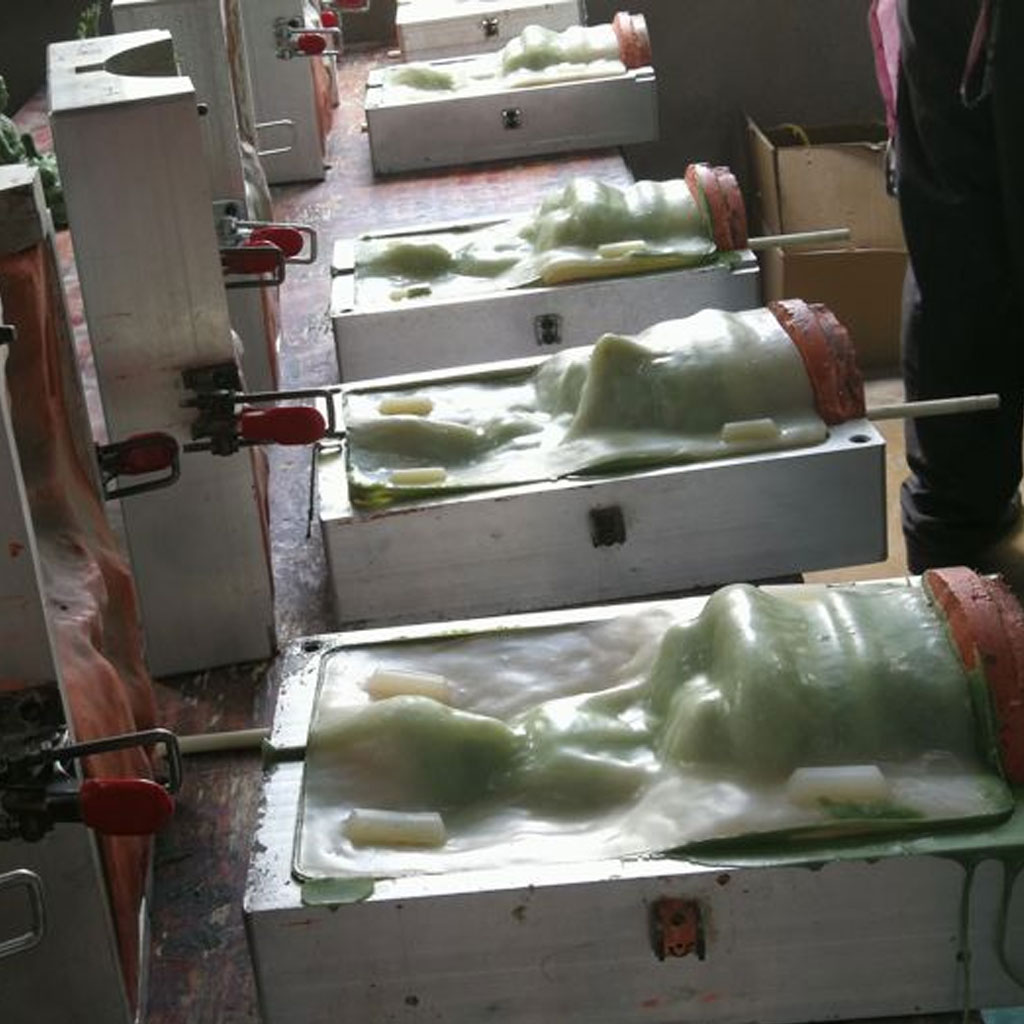
BE-CU Foundry is dedicated to casting lost wax molds and is an earlier manufacturer in China with rich experience. The factory has introduced the advanced design technology of medium temperature wax injection mold, with reasonable material selection, high-precision production and other manufacturing technologies, and on the basis of modern advanced mold making equipment, it has made positive achievements for domestic valve and pump product enterprises over the years. s hard work.Our factory undertakes the manufacture and molds making of various materials such as aluminum, steel, and brass.According to the actual samples and drawings, we can make various mechanical accessories, various water pumps, special-shaped wheels, large and small valves, and lost wax molds of pipe fittings. The molds produced by BE-CU Foundry have reasonable process, easy demoulding, and the technical performance of the products has reached the industry standard. go hand in hand. Our factory produces various series of molds, if users need other models, they can be processed according to the drawings to meet the needs of users.
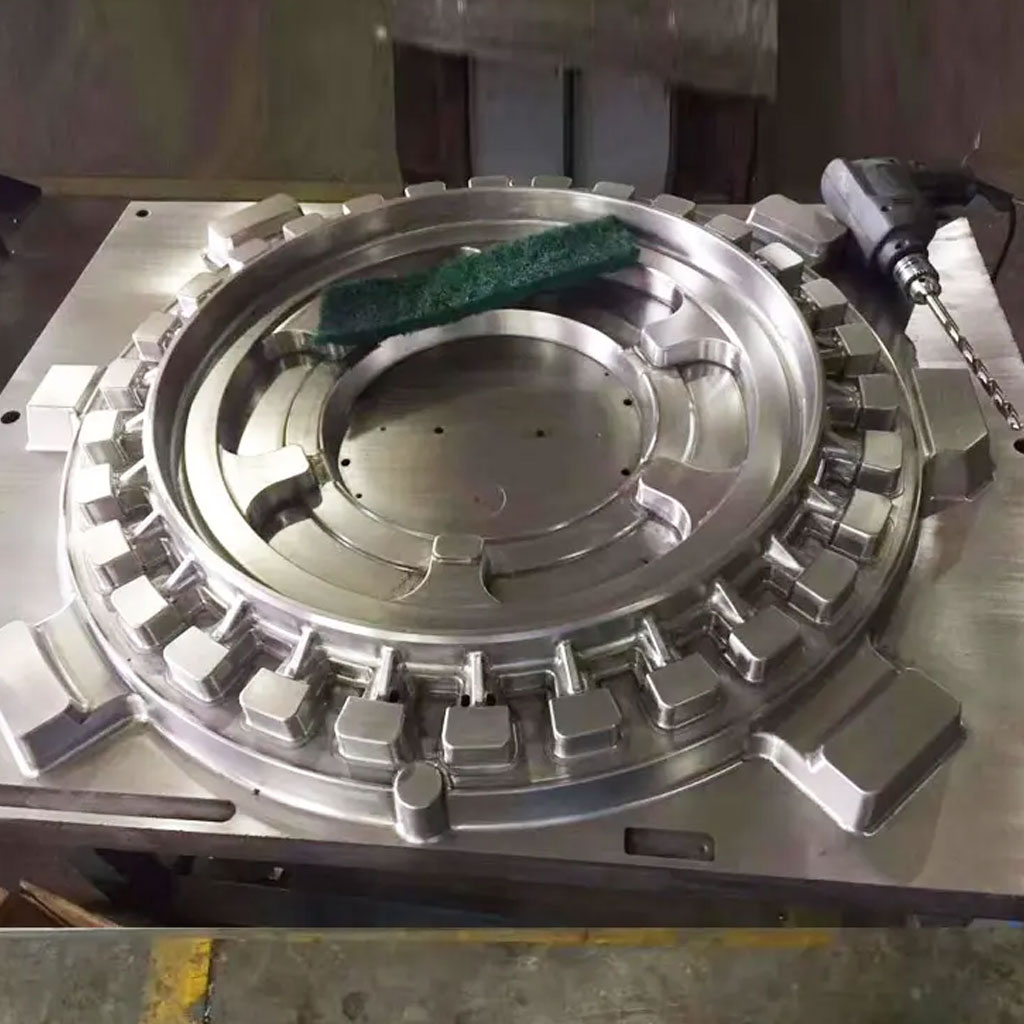
The Process Of Sand Casting Mold Making
The coated sand process is more and more recognized by large foundries. In order to better serve the foundry, the mold drawings of the casting mold county process that have been reviewed and confirmed are arranged by the mold technicians, and special manufacturing procedures are planned and method.
The manufacture and assembly of each part are carried out in the mold shop, and the manufacturing process is closely cooperated with the technical department. Coated sand hot core box mold materials are resin sand HT250. And do heat treatment, which has a very important impact on the service life of the mold. Each part must be carefully inspected and measured, and completed by a special testing room, and the molds are FIT-fitted by experienced technicians according to tolerances. Hot Core Jinmo County has passed the mold test of the coated sand core shooter (coated sand shell core machine) to verify that the function of the mold meets the customer’s requirements.
The workshop is to test the trial production of molds to ensure the continuous operation of the coated sand core shooting machine (shell core machine) and to continuously produce high-quality products, so as to provide customers with convenient and fast services. More importantly, it can communicate and collaborate with customers in time on necessary technology, quality and construction period.
The workshop is to test the trial production of molds to ensure the continuous operation of the coated sand core shooting machine (shell core machine) and to continuously produce high-quality products, so as to provide customers with convenient and fast services. More importantly, it can communicate and collaborate with customers in time on necessary technology, quality and construction period. Finally, the foundry workshop can complete the final inspection of the mold. Under the leadership of professional foundry engineers and technicians, it adopts advanced casting technology and equipment to trial-produce coated sand castings to provide customers with perfect services. BE-CU adheres to the customer-first after-sales service policy, and manages the repair, maintenance and transformation of mold products. And strive to expand service areas.

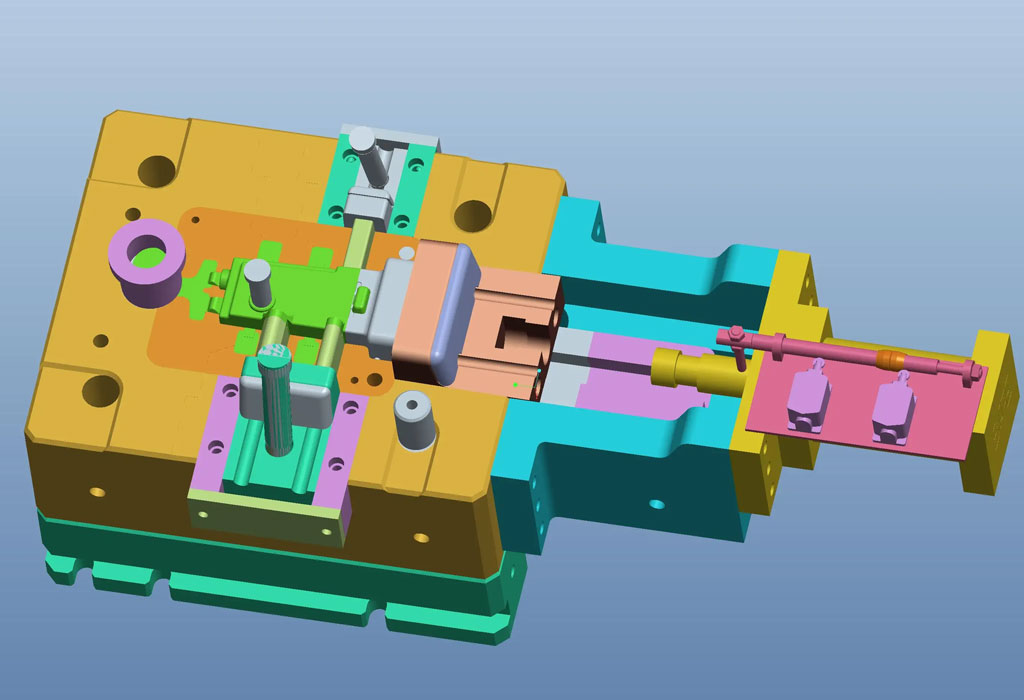
The Process Of Die Casting Mold Making
For small and simple die-casting molds, the cavity is usually machined directly on the fixed mold or movable mold plate, that is, an integral mold plate; for large-scale precision molds with complex shapes, an inlaid mold plate is generally used, that is, the processed cavity is used. The inserts fit into the moulded holes of the template.
The processing of the integral formwork The integral formwork generally uses the forging as the blank, and the processing procedure is: forging → annealing → rough machining → annealing treatment to eliminate internal stress → quenching and tempering treatment → machining → cavity finishing. Its processing procedure is as follows:
- Material preparation: Cut the round bar material on the sawing machine according to the material length.
- Forging: Forging the round bar into a hexahedron.
- Annealing: Eliminate the internal stress of the forging and improve the cutting performance of the blank.
- Roughing: Roughly machine the upper and lower planes on a milling machine or planer, and then use these two planes as the benchmark to process the four sides, leaving a finishing allowance of about 1mm.
- Annealing and quenching and tempering treatment: The cutting amount of rough machining is large, and deformation may occur due to uneven internal stress, so annealing treatment is required before finishing to eliminate the deformation caused by internal stress. Quenching and tempering treatment generally requires a hardness of 35-40HRC
- Grinding plane: On the surface grinder, grind the upper and lower planes and the two sides that are perpendicular to each other.
- Scribing: Based on the two vertical sides, draw out the center position and outline of the cavity, the position of the core, etc.
- Boring: Use a coordinate boring machine to process guide post holes, core holes or mounting holes for sprue sleeves.
- Processing of cavity: If the cavity is rectangular, it needs to be processed on a vertical milling machine.
- Polished cavity.